-
-
News
News Highlights
- Books
Featured Books
- pcb007 Magazine
Latest Issues
Current IssueSales: From Pitch to PO
From the first cold call to finally receiving that first purchase order, the July PCB007 Magazine breaks down some critical parts of the sales stack. To up your sales game, read on!
The Hole Truth: Via Integrity in an HDI World
From the drilled hole to registration across multiple sequential lamination cycles, to the quality of your copper plating, via reliability in an HDI world is becoming an ever-greater challenge. This month we look at “The Hole Truth,” from creating the “perfect” via to how you can assure via quality and reliability, the first time, every time.
In Pursuit of Perfection: Defect Reduction
For bare PCB board fabrication, defect reduction is a critical aspect of a company's bottom line profitability. In this issue, we examine how imaging, etching, and plating processes can provide information and insight into reducing defects and increasing yields.
- Articles
- Columns
- Links
- Media kit
||| MENU - pcb007 Magazine
Estimated reading time: 2 minutes
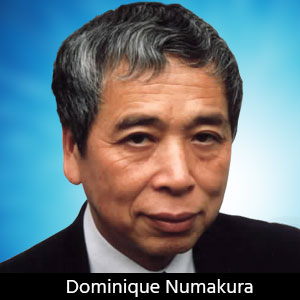
EPTE Newsletter: Next-Generation Flex Circuits—Monocoque Printed Circuits
Several weeks ago, I released a short column about monocoque printed circuits, a new 3D circuit technology using thermoplastic materials considered next-generation technology for printed circuits. The circuit traces are built on thermoplastic sheets and bent using a heating process. The new technology reduces wiring space in mobile electronic devices and eliminates flexible circuits and wire harnesses. I received many inquiries, specifically requesting detailed technical information. A few companies commented about their success with this same circuit technology. There is much interest from design engineers looking for practical 3D wiring material for compact electronic devices, such as smartphones and digital cameras. Let’s take a brief look at this new 3D circuit technology.
More than 30 years ago, a flex circuit manufacturer in New England developed bendable circuits and modified the standard technology for flex circuits. A plastic resin was introduced as a base layer for copper foil laminates. The laminates were chemically etched to generate copper circuits, and these circuits could be bent to form 3D wiring. Unfortunately, the base material was not stiff enough, so 3D circuits were eliminated in many applications.
Almost the same time 30 years ago, the basic concept for molded interconnect device (MID) circuits was created to build 3D circuits on plastic parts. The process of creating 3D components was already established through molding or injection using traditional plastic resins. Component manufacturers found it difficult to generate electronic circuits on plastic components. They tried with newer technologies (metalizing and laser scribing) but were unsuccessful due to the limited capabilities of these technologies.
An easy solution came to light using silver ink printing for thick-film circuit technology. It looks like a Columbus egg. The process is very simple (Figure 1). Silver-based conductive ink is screen-printed on a thermoplastic sheet to create electronic circuits. Single-layer circuits are easy to make. Double-layer and multilayer circuits are practical as they are made on a film base substrate with via holes. Through-holes are easy to make using a traditional thick film process. The baking temperature should be relatively low to generate a higher yield. Appropriate ink materials are selected for the thermal process. The second step of the process is to place the work in a die set after pre-heating. A vacuumed forming could make a better shape for the thicker substrates. We are successful using PET sheets, PEN films, acrylic sheets, polycarbonate sheets, and more. There may be additional plastic resins available.
3D circuit technology is not universally available because of mechanical stresses during the forming process. The forming on the corners requires a radius greater than 2 mm, and the silver traces should be wider than 0.3 mm. We are preparing a design guide for 3D circuits.
The best feature of this 3D circuit technology is the wiring built-in plastic parts. The plastic parts will serve as mechanical framing and wiring—hence the name monocoque printed circuits. The use of supplemental flexible circuits and wire harnesses are not required; the space required for wiring is reduced without an increase in cost. There are no special technologies or manufacturing equipment required, but experience using specific materials is necessary.
Editor’s note: Read?Part 1,?Part 2,?Part 3, and Part 4?on monocoque printed circuits.
This column appeared in the August issue of Design007 Magazine in the FLEX007 section.
More Columns from EPTE Newsletter
EPTE Newsletter: Travel to Japan During COVIDEPTE Newsletter: A New COVID Surge in Taiwan?
EPTE Newsletter: COVID-19 PCR Test in Japan
EPTE Newsletter: Japan Failing in Vaccine Distribution
EPTE Newsletter: A Long Trip to the U.S.
EPTE Newsletter: Ten Years After Fukushima
EPTE Newsletter: Taiwan Releases 2020 PCB Production Numbers
EPTE Newsletter: The Printed Circuit Industry in China