-
-
News
News Highlights
- Books
Featured Books
- pcb007 Magazine
Latest Issues
Current IssueSales: From Pitch to PO
From the first cold call to finally receiving that first purchase order, the July PCB007 Magazine breaks down some critical parts of the sales stack. To up your sales game, read on!
The Hole Truth: Via Integrity in an HDI World
From the drilled hole to registration across multiple sequential lamination cycles, to the quality of your copper plating, via reliability in an HDI world is becoming an ever-greater challenge. This month we look at “The Hole Truth,” from creating the “perfect” via to how you can assure via quality and reliability, the first time, every time.
In Pursuit of Perfection: Defect Reduction
For bare PCB board fabrication, defect reduction is a critical aspect of a company's bottom line profitability. In this issue, we examine how imaging, etching, and plating processes can provide information and insight into reducing defects and increasing yields.
- Articles
- Columns
- Links
- Media kit
||| MENU - pcb007 Magazine
Estimated reading time: 2 minutes
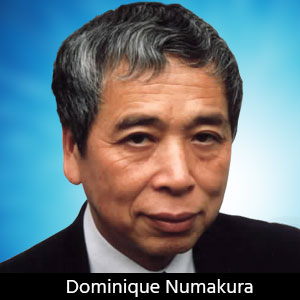
EPTE Newsletter: Next-Generation Flex Circuits—Textile Base Flex
The COVID-19 pandemic remains active throughout the world as Phase 3 clinical trials are underway for many pharmaceutical companies. Large R&D investments from Big Pharma could bear fruit in the coming months as the race for a vaccine continues. Several equipment manufacturers are developing medical devices for both diagnosis and treatment to fight COVID-19. This market could be huge in the near future.
Medical electronics is already a big segment of the industry. New medical devices will require different performance standards than typical consumer electronics, such as smartphones, especially when attached to your body. These new wearable electronic devices require comfort as well as reliability. The device’s base material must be elastic and permeable to allow air and moisture to pass through it while addressing allergies and skin irritations.
Traditional flexible dielectric materials, such as polyimide and PET films, are not suitable to satisfy these medical requirements. Traditional electronics devices focus on performance from stable substrates, and characteristically have high dimensional stability, no permeability, low moisture absorption, and high insulation resistance. This will not work for most of the wearable electronic medical devices, so where do we go from here?
An assortment of textiles was developed over the years purely out of necessity (the mother of all inventions). There are many fibers that are stretchable and permeable, and more than one could be suitable to use in wearable medical devices.
Creating electronic circuits on fabric substrates is not easy. The subtractive processes in manufacturing use wet chemicals. This causes an adverse reaction with textiles, so a dry process is needed of generating circuits on the textile substrates. I am experienced with two types of dry processes: a die stamping process, and screen-printable thick-film circuits.
The die-stamping process uses a specially formed punching die to cut the copper foil with glue and bond the circuits onto textile substrates—a completely dry process. (Feel free to reach out to me for details on this technology).
The second dry-processing technique uses screen-printable thick film circuits in the manufacturing process. The process is very simple. Conductive inks, such as silver and carbon, are screen-printed on a textile substrate and baked. It is not capable to generate fine lines with high conductivity, but it can create stable traces on the fabric’s rough surface using appropriate screen masks. Double-sided and multilayer circuits can be created by repeating the printing processes, and large circuits up to 2x3 meters are available.
Silver and carbon ink are screen-printed to form a pressure sensor array on cotton sheets. The sensor array detects weight distribution continuously while the patient is lying down. An example of this application is shown in Figure 1. The technology is fairly new but used in many applications in the medical and healthcare industries. The technology curve and market upswing will be V-shaped in the near future.
This column originally appeared in the September 2020 issue of Design007 Magazine in the FLEX007 section.
More Columns from EPTE Newsletter
EPTE Newsletter: Travel to Japan During COVIDEPTE Newsletter: A New COVID Surge in Taiwan?
EPTE Newsletter: COVID-19 PCR Test in Japan
EPTE Newsletter: Japan Failing in Vaccine Distribution
EPTE Newsletter: A Long Trip to the U.S.
EPTE Newsletter: Ten Years After Fukushima
EPTE Newsletter: Taiwan Releases 2020 PCB Production Numbers
EPTE Newsletter: The Printed Circuit Industry in China