Estimated reading time: 4 minutes
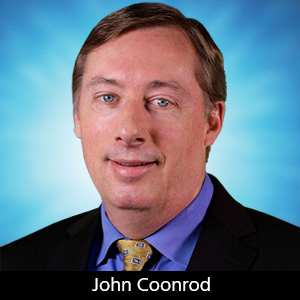
Lightning Speed Laminates: Why High-Frequency Materials Have Different Dk Values
When an engineer researches high-frequency circuit materials, they will notice there are many offerings of what appears to be the same material type but with different Dk values. One might ask, “Why are so many different Dk values desired?” The answer is not straightforward, but there are very good reasons for these different materials. This column will give a quick overview of the need for these materials with different Dk values, as related to different high-frequency applications.
Insertion loss is often considered with many high-frequency applications and is made up of four components: conductor loss, dielectric loss, leakage loss, and radiation loss. The conductor loss is related to the circuit conductor; often, the major concern is the surface roughness at the copper-substrate interface.
Dielectric loss is mostly related to the dissipation factor of the circuit material. Leakage loss is associated with the volume resistivity of the dielectric material, which is between the copper planes. Typically, the volume resistivity is very high for high-frequency circuit materials, and due to that good property, leakage loss is not a concern. Although, some high-power applications can have an issue with leakage loss. The last component of insertion loss is radiation loss, and that is how much loss is radiated off the circuit.
Radiation loss is generally not desired because it is an increase of the signal loss, but there is an additional concern with the radiated energy having the potential to corrupt neighboring circuitry. There are many different items that can cause radiation loss to vary, including circuit design, substrate thickness, PCB fabrication anomalies, the Dk of the substrate, and frequency. In general, a high-frequency circuit material with a low Dk can have increased radiation loss, and a higher Dk material will have less radiation loss. However, there are cases where higher radiation loss is desired, and that would be for antenna applications where they have circuit patterns intended to transmit (radiate) energy at a certain frequency. In the case of antenna applications, you will typically find that a lower Dk material is used, but there are exceptions.
There is another attribute of Dk that relates to circuit size. In general, circuits using materials with a lower Dk value will have a longer wavelength than circuits using material with a higher Dk value. Many RF applications are very sensitive to wavelength, and the designs of the circuit features are very often based on a fraction of wavelength. As an example, a circuit structure intended to resonant will often be designed to have a physical size that relates to half the wavelength for the intended frequency of resonance.
Expanding on this example, if an RF circuit design is intended to have a resonant peak at 3.6 GHz, it uses 20-mil material; the Dk value of the material is 3.66, so the resonator element should be about 0.97” (24.6mm) in length. However, with that same comparison and the only difference is material with a Dk value of 6.4, the length of the resonator element will reduce to be 0.77” (19.6 mm).
That is a size reduction of about 20%, and if a material is used with a Dk value of 11.2, that will give a size reduction of 37%. These different resonator sizes, using materials with different Dk values, will still yield a resonant peak at 3.6 GHz. However, with the decreased resonator size, the other circuit features will also decrease; in some cases, that is not desired. There can be many trade-offs to consider when choosing materials with different Dk values.
Another thought for Dk differences involves considering coupled features. In RF engineering, there are often circuit features coupled together by their electric fringing fields. These coupled circuit features are used to design and implement many different types of RF filters, directional couplers, and impedance matching networks. The strength of the coupled fields between these circuit features is often critical, and the intensity of the coupled fields will vary with a Dk dependency.
A high-frequency circuit using coupled technology and a material with a lower Dk value will have less field intensity than using a circuit material with a higher Dk value. Basically, a circuit material with a higher Dk will cause the fields to concentrate, and they will not spread over a larger area, but they will have higher intensity in a small area. This also goes back to the concept of radiation, where I commented that circuits using materials with high Dk do not radiate as much as circuits using a lower Dk because the fields are more concentrated within the circuit for the high Dk material.
This was a quick overview of different things to consider when using high-frequency circuit materials with different Dk values; however, there can be many other issues to consider for different PCB applications. The designer should consult their high-frequency circuit material supplier when dealing with the details of their particular application and understand what the optimum material choice would be for their circuit design.
John Coonrod is technical marketing manager at Rogers Corporation. To read past columns or contact Coonrod, click here.
More Columns from Lightning Speed Laminates
Lightning Speed Laminates: Millimeter-wave Properties and PCB Design ChallengesLightning Speed Laminates: Optimizing Thermal Management for Wireless Communication Systems
Lightning Speed Laminates: Test Vehicles for PCB Electrical Material Characterization
Lightning Speed Laminates: Optimum Thermal Stability Considerations
Lightning Speed Laminates: Thermal Management Isn’t Getting Easier
Lightning Speed Laminates: Benefits of High-Performance Hybrid Multilayer PCBs
Lightning Speed Laminates: An Overview of Copper Foils
Lightning Speed Laminates: The Importance of Circuit Features for Millimeter-Wave Applications