-
-
News
News Highlights
- Books
Featured Books
- smt007 Magazine
Latest Issues
Current IssueWhat's Your Sweet Spot?
Are you in a niche that’s growing or shrinking? Is it time to reassess and refocus? We spotlight companies thriving by redefining or reinforcing their niche. What are their insights?
Moving Forward With Confidence
In this issue, we focus on sales and quoting, workforce training, new IPC leadership in the U.S. and Canada, the effects of tariffs, CFX standards, and much more—all designed to provide perspective as you move through the cloud bank of today's shifting economic market.
Intelligent Test and Inspection
Are you ready to explore the cutting-edge advancements shaping the electronics manufacturing industry? The May 2025 issue of SMT007 Magazine is packed with insights, innovations, and expert perspectives that you won’t want to miss.
- Articles
- Columns
- Links
- Media kit
||| MENU - smt007 Magazine
Estimated reading time: 5 minutes
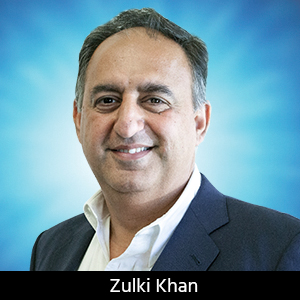
Zulki’s PCB Nuggets: Consider Low-Temp Solder for PCB Microelectronics Assembly
As I’ve often said, growing numbers of OEMs are producing small, more portable devices, especially medical electronics OEMs that are pioneering insertable and ingestible medical devices. With these newer, smaller devices coming on the market, EMS providers and contract manufacturers (CMs) must adjust their PCB assembly technologies to comply with these demands. Thermal profiling and the use of the correct solder paste, in this instance, become an even more critical step than before in conventional SMT and the newer microelectronics assembly.
In today’s day and age, when many products are shrinking, PCB, component, and packaging sizes matter considerably. That’s why caution has to be taken when products like these are subjected to high-temperature reflow cycles. It’s important to consider low-temperature profiling. It is more effective if you can reflow components and solder pastes at lower temperatures and with lower thermal profiles, if possible.
But first, it’s a good idea to revisit various reflow temperature ranges. Lead-free solder, like SAC305, is 235–245°C peak temperatures; leaded solder is about 180–185°C. Meanwhile, you have to take into consideration chemical mixtures in low-temperature lead-free solder pastes. The most common compositions are tin/bismuth and tin/bismuth/silver. Peak reflow temperatures associated with tin/bismuth solder paste range from 165–195°C compared to tin/lead solders at 220–240°C.
A key benefit is the peak reflow temperature of between 165–195°C that provides a Delta of 50° C between SAC305 and low-temperature bismuth-based solder, thereby subjecting the boards and components to lower temperature cycles and keeping the temperatures in more of a “safe zone.”
To review, some of the issues that can crop up when applying higher-temperature thermal profiles and reflow during the assembly of PCBs include:
- Board warpage
- Chances of creating larger voids and head-in-pillow are higher in BGA and QFN packaging
- Greater chance of board delamination
Now, let’s take a look at this low-temperature bismuth-based solder paste and its use for a thermal profile. It can reduce peak reflow temperature requirements to as low as 165–180°C. Also, sizes of voids and head in pillow flaws on bottom terminated devices are reduced since there is a 50°C Delta between a low-temperature peak profile versus the SAC305 peak profile. Plus, low-temperature solder paste allows considerably less thermal exposure. The less a board is exposed in terms of high temperature, the better it is for the boards and components, which increases long-term reliability.
For example, the quality of an FR-4 or Rogers board can experience deterioration and possible delamination when it unnecessarily undergoes three to four thermal cycles instead of two, which can be sufficient. Those extra thermal cycles can possibly deteriorate component longevity and the epoxy resin inside the FR-4 material.
There are also negative sides to using low-temperature bismuth-based solder paste. There’s a tendency/possibility of cracking during cool down. To alleviate that problem, low-temperature solder (LTS) can be cooled down at a slower gradient. You cannot rapidly cool it down because it becomes brittle and can break. This means you have to carefully create the thermal profile from peak to cool off period. You have to make sure the temperature is not dramatically dropped, but instead gradually.
It takes more slump when you’re creating the thermal profile because tin-bismuth alloy, such as Sn42Bi58, creates more wetting when the slump is calculated properly and is done accurately. In SAC305, it is more forgiving when you are increasing or decreasing the temperature. But LTS is not as forgiving, and you have to create the profile and maintain the profile in a much better-controlled way.
Less Thermal Shock
By applying low-temperature solder paste, the board sustains less of a thermal shock compared to SAC305, which is around 235–245°C versus 160–170°C. This is a huge Delta. In the long run, medical device PCBs, for instance, perform considerably better, more reliable, and much longer.
Let’s go a little deeper into LTS and ask, “Why is this specifically needed?” Take medical electronics OEMs as an example. The new products they are launching together with the chips/devices being used cannot handle high temperatures for either the wire bonding or the packaging involved or otherwise.
But also consider that some OEMs have gradient melting point limitations for their terminations at considerably lower temperatures. In cases like that, care has to be taken about the type of low-temperature solder paste to be used. That’s why it is important that the EMS provider or CM work closely with the customer to coordinate and approve these critical thermal profiling points before running the product through SMT lines.
Another key point to consider is that solder paste companies offer different compositions involving tin, silver, copper, and bismuth for the thermal cycle. Here’s where the EMS provider and OEM customer need to closely collaborate about solder paste composition and characteristics, carefully reviewing the datasheets for these low-temperature solder pastes from their manufacturers.
Drop shock is one other aspect to investigate closely. This involves testing to determine how these assemblies are going to hold up when they are dropped from a certain distance to the ground or applying a certain amount of force to make sure if there are no cracks in the assembly, thereby making them reliable.
These solder joints are tested by thermal shocking, drop shock, and mechanical strength for vibrations. If these are projects that are used in a hazardous environment, you have to make sure that they can withstand mechanical strength once the product is fully assembled.
The OEM, EMS company, or CM needs to ensure that although the composition of bismuth is more in the alloy for low-temperature profiles and low-temperature solder paste, the joint created and assembly level or the microelectronic level for chip on board are still as sturdy as lead-free or leaded assemblies. Product usage is not going to change because the solder paste or thermal profile is changed.
In conclusion, there are certain considerations that need to be investigated before a low-temperature thermal profile paste can be selected for both SMT and microelectronic assemblies.
Zulki Khan is the president and founder of NexLogic Technologies Inc.
More Columns from Zulki's PCB Nuggets
Zulki's PCB Nuggets: Cleanliness is Next to ReliabilityZulki’s PCB Nuggets: Thermal Compression Bonding for Extra Fine Pitch Flip Chips
Zulki’s PCB Nuggets: WBAN Steps Into PCB Microelectronics Assembly
Zulki’s PCB Nuggets: Photonics Comes to PCB Microelectronics Assembly
Zulki’s PCB Nuggets: Sub-Micron Die Bonding—Don’t Be Misled by Five Micron Placement Standard
Zulki’s PCB Nuggets: Meet the New Player in PCB Microelectronics Assembly—Interposers
Zulki’s PCB Nuggets: How Effective Is Your PCB Microelectronics Assembly?
Zulki’s PCB Nuggets: Five Key Benefits for Onshoring PCB Microelectronics Assembly