-
- News
- Books
Featured Books
- pcb007 Magazine
Latest Issues
Current IssueInventing the Future with SEL
Two years after launching its state-of-the-art PCB facility, SEL shares lessons in vision, execution, and innovation, plus insights from industry icons and technology leaders shaping the future of PCB fabrication.
Sales: From Pitch to PO
From the first cold call to finally receiving that first purchase order, the July PCB007 Magazine breaks down some critical parts of the sales stack. To up your sales game, read on!
The Hole Truth: Via Integrity in an HDI World
From the drilled hole to registration across multiple sequential lamination cycles, to the quality of your copper plating, via reliability in an HDI world is becoming an ever-greater challenge. This month we look at “The Hole Truth,” from creating the “perfect” via to how you can assure via quality and reliability, the first time, every time.
- Articles
- Columns
- Links
- Media kit
||| MENU - pcb007 Magazine
Estimated reading time: 4 minutes
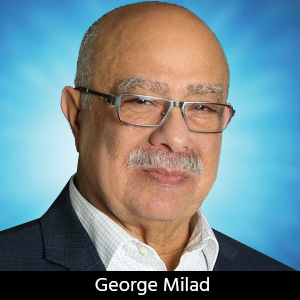
The Plating Forum: Training for Plating Processes in the Electronics Industry
Wikipedia defines training as follows: “Training is teaching, or developing in oneself or others, any skills and knowledge or fitness that relate to specific useful competencies. Training has specific goals of improving one's capability, capacity, productivity, and performance. It forms the core of apprenticeships and provides the backbone of content at institutes of technology. In addition to the basic training required for a trade, occupation, or profession, training may continue beyond initial competence to maintain, upgrade, and update skills throughout working life.”
In the electronics industry, the role of the supplier in training their prospective customer on the ins and outs of a plating process is paramount to the success of any new installation. This is particularly important, as there are very few curriculums in formal educational institutions that directly address the specific skill set needed by our industry.
Plating is a very old industry and has been studied for many generations. Its basic principles are well understood and documented. However, when it comes to the intricate details of plating a circuit board, there is so much to learn and apply.
Most of the plating chemistries in use today in printed circuit shops are proprietary to the specialty chemical supplier. Supplier R&D departments specialize in finding solutions to meet the ever-changing requirements of new circuit board designs. The net result is a series of products that, when used in a specific way, would give the desired outcome. Suppliers do not divulge their trade secrets to their buyers—the circuit shops.
Instead, they describe the product and explain its capabilities to the buyer and supply a detailed data sheet that contains instructions for use, which includes makeup procedures for the electrolyte or the bath, as well as its operating ranges and the expected outcome. They also supply procedures to analyze and replenish the electrolyte during its use, as well as schedules for dump and remake of electrolytes. Electrolyte or bath life is mainly determined by the buildup of by-products that will eventually interfere with the functionality of the chemistry.
The supplier also specifies the type of equipment and any specific controllers or dosing peripherals that are needed for their proprietary system to work. With all this complexity, a well-trained user is a must for success and for achieving the desired end result.
Suppliers have training experts available to their customers. This begins with sales, and eventually, the burden of training falls on the shoulders of the technical service engineer in the lab (in-house) or in the field or at the site.
In-House Training
Most suppliers have laboratories and demonstrate chemical processes set up in their facility. In most cases, a lead person (plater, engineer, or manager) from the buyer would spend a day or two being trained by the application engineer. Training involves a hands-on demonstration of the process and may also entail training on the analytical methods used to control the chemistry of the electrolyte for replenishment and continuous successful operation. The trainer becomes an important resource to the user as different situations arise that may include product evolution, increased capacity, or the addition of new equipment or personnel.
Onsite Training
Onsite training is the other side of the coin. Here, the regional sales and technical service engineer conduct the training. In this setup, there is ample opportunity to train different individuals as needed. Onsite training involves adapting the user’s equipment and personnel to the process being installed.
Onsite training covers different individuals or groups in the shop. It starts with the process engineer who assumes the primary responsibility of overseeing the successful running of the process. In some of the smaller operations, the position of process engineer is absent. The duties of the process engineer are performed by the production manager, who is assisted by lab personnel, as well as the supplier tech service engineer.
Special training is also needed for the production floor personnel, like the platers, who run the process during their shifts. Training on inspection techniques is paramount to ensure that the parts meet in-house QC requirements. A competent, well-trained plater is the gatekeeper for the product coming off the line. They are always the first to recognize any deviance in product quality.
Training of lab personnel on specific analytical techniques is needed to ensure proper analysis and replenishment of the different components of the bath. This is particularly critical if a new analytical tool is introduced into the lab. Setting up the new tool becomes the responsibility of the supplier technical service team. Lab personnel are trained on the setup and maintenance of controllers that are installed on the line. The lab personnel are also trained in setting up dosing systems that may be needed to maintain a steady-state operation. The lab usually has the responsibility for determining the end of life of a bath and scheduling a dump and remake. The lab also oversees the makeup of the new bath.
Communicating the proper operation of any chemical process is critical to the success of the operation. This is achieved by the successful training of different personnel in the production shop by the supplier team. Continuous monitoring of the setup is equally important, and retraining is always needed as changes in equipment, product requirements, or personnel occur.
This column originally appeared in the December 2020 issue of PCB007 Magazine.
More Columns from The Plating Forum
The Plating Forum: Reduction Assisted Immersion Gold for ENEPIG Surface FinishThe Plating Forum: Surface Finish Evolution from Conventional to Advanced
The Plating Forum: Plating in Electronic Applications
The Plating Forum: How the Pandemic Impacted PCB Manufacturing
The Plating Forum: The Significance of IPC ENIG Specification 4552 Revision B
The Plating Forum: The IPC Surface Finish Specifications
The Plating Forum: An Overview of Surface Finishes
The Plating Forum: DIG—The Next Generation