-
- News
- Books
Featured Books
- design007 Magazine
Latest Issues
Current IssueProper Floor Planning
Floor planning decisions can make or break performance, manufacturability, and timelines. This month’s contributors weigh in with their best practices for proper floor planning and specific strategies to get it right.
Showing Some Constraint
A strong design constraint strategy carefully balances a wide range of electrical and manufacturing trade-offs. This month, we explore the key requirements, common challenges, and best practices behind building an effective constraint strategy.
All About That Route
Most designers favor manual routing, but today's interactive autorouters may be changing designers' minds by allowing users more direct control. In this issue, our expert contributors discuss a variety of manual and autorouting strategies.
- Articles
- Columns
- Links
- Media kit
||| MENU - design007 Magazine
Estimated reading time: 4 minutes
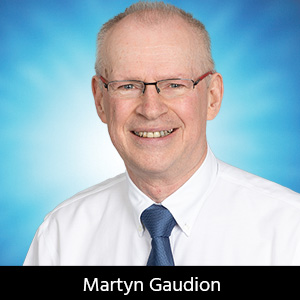
The Pulse: Simulating Stackup and Signal Integrity
Simulation and modelling are long-time friends of the engineer. I recently read The Works of Isambard Kingdom Brunel [1] (Pugsley). The math and modelling that accompanied his civil engineering works almost 200 years ago are quite humbling—even more so given that all his calculations were made by hand, devoid of the luxury of high-speed computing that bathes the engineer of this century in an abundance of tools.
But the purpose of modelling then was the same as now—to reduce the number of prototypes, to predict safety margins for structural loads, and, in Brunel’s case as an engineer, he also had a head for marketing as his mathematical and engineering abilities allowed him to build bridges with fewer materials and shallower curves than had his peers doubting their longevity. However, here we are 200 years later, and high-speed trains and traffic are still using his elegantly designed structures with safety.
Just as with modern engineering challenges, the materials in his hands were not ideal, wrought iron was relatively new, and wooden structures, though well understood, were still natural materials and subject to the ravages of damp and decay over the life of the structure. Brunel had to understand both the math, and the limitations and inherent variability of the materials he deployed. This was especially the case in tunnelling operations where, despite geological surveys, the nature of the material being tunnelled was not always as predictable as expected.
Electronic designs in which the architecture deploys the PCB are also subject to variation, and just like Brunel, when designing a PCB in today’s computer simulated environment, it helps to have a thorough understanding of the foundation you are using to build your design. The unsung hero of electronic designs—the PCB—provides the mechanical, thermal, and electrical platform on which 90% of electronic designs are realised.
Simulation can only be as good as the source data, so the better understanding you have of the materials in your stack, the better the understanding of the effect of the PCB production process on those materials. This puts you a step ahead when you are modelling how the finished product will behave. Modeling stackups involves a mix of disciplines, the simulation tool needs to know the material types, the glass/resin ratios, and the target copper density of the finished design to predict how the materials will press and cure into the final finished height. Locations of drill ends are needed so that plating thickness can be accounted for.
Understanding Materials
Returning to the civil engineering analogy, when tunnelling it’s a matter of life or death, so it is vital to understand the strata you are working in. With PCBs, careful consideration of the substrate materials can yield benefits. Working with spread glass reinforcement as opposed to traditional open weave glass can yield signal integrity benefits as the transmission line runs in a “more” homogeneous medium. But you need to keep in mind the mechanical and fluid flow considerations, as the flat glass—while better for laser drilling and signal integrity— provides a barrier to resin flow across the reinforcement, so you need to ensure adequate resin content to avoid glass stop, or delamination.
Copper Characteristics
Moving from the dielectric medium to the copper plane and signal layers, new designers will often think they can use datasheet values for copper roughness. This is an understandable position if they don’t have a knowledge of the PCB fabrication process, but a glance at Figure 4 shows that the PCB fabrication process adds plated copper to the surfaces containing the drill ends to connect the vias in the PTH process. Therefore, the roughness needed for simulation is that of the plated layer and not of the base material. Simulation can only be as good as the input data fed to the simulator. The data does exist, but it is the job of the designer to know where to look, and when to take that data from a material data sheet, and when it needs to come from the fabricator.
Once the correct input data is available, then even the roughness may be fed into the simulator and the effects on signal integrity modelled with ease.
Figure 7 presents the classic modelling and simulation dilemma. The Huray model is an excellent way of predicting the effect of copper roughness on signal losses along a transmission line, something which is inherently challenging. However, to “feed” the Huray model with good input data requires an SEM image of the finished plated or unplated copper surface. Not everyone has a scanning electron microscope on hand, and so a compromise in estimating the parameters is needed for day to day as opposed to laboratory use. Fortunately, Bert Simonovich of Lamsim Enterprises has provided a method which translates the matte and drum side roughness into Huray input parameters which are “good enough” to make a very usable model for predicting roughness impacted insertion loss.
Simulation Models
Whenever simulating, keep in mind the words of Polar’s favourite eminent British statistician, George Edward Pelham, “All models are wrong—but some are useful.” This is a piece of advice that engineers and fabricators need to take to heart; while the mathematical models we use for modelling save time, make better product, and increase yields, we only get the best from them by applying them with a good understanding of the input data and the limitations of the base materials used, and the manufacturing processes of pressing, plating, curing, and chemical adhesion promotion treatments applied to the finished article.
References
- The Works of Isambard Kingdom Brunel, edited by Sir Alfred Pugsley, Institute of Civil Engineers, London/University of Bristol.
This column originally appeared in the April 2021 issue of Design007 Magazine.
More Columns from The Pulse
The Pulse: Design Constraints for the Next GenerationThe Pulse: Ultra Upgrade Unknowns—What’s Coming for UHDI?
The Pulse: Commonsense Cost Cutting
The Pulse: Overconstraining: Short, Slim, and Smooth
The Pulse: Drilling Down on Documentation
The Pulse: New Designer’s (Partial) Guide to Fabrication
The Pulse: Simplest Stackups Specified
The Pulse: Rough Roughness Reasoning