-
-
News
News Highlights
- Books
Featured Books
- smt007 Magazine
Latest Issues
Current IssueWhat's Your Sweet Spot?
Are you in a niche that’s growing or shrinking? Is it time to reassess and refocus? We spotlight companies thriving by redefining or reinforcing their niche. What are their insights?
Moving Forward With Confidence
In this issue, we focus on sales and quoting, workforce training, new IPC leadership in the U.S. and Canada, the effects of tariffs, CFX standards, and much more—all designed to provide perspective as you move through the cloud bank of today's shifting economic market.
Intelligent Test and Inspection
Are you ready to explore the cutting-edge advancements shaping the electronics manufacturing industry? The May 2025 issue of SMT007 Magazine is packed with insights, innovations, and expert perspectives that you won’t want to miss.
- Articles
- Columns
- Links
- Media kit
||| MENU - smt007 Magazine
Estimated reading time: 4 minutes
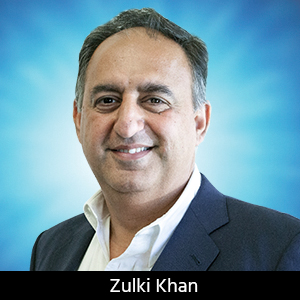
Zulki’s PCB Nuggets: Meet the New Player in PCB Microelectronics Assembly—Interposers
Today, everything is shrinking and getting smaller, as I have written about in earlier columns. Now, a new player is coming in to help make PCB real estate more available on small flex and flex-rigid circuits undergoing microelectronics assembly.
That new entrant is an interposer, which is a type of connector that takes connections from one side of the substrate or board or material to the other side. It is an electrical interface between one socket and another, for the purpose of spreading the connection to a wider pitch or to route the connection to a different path. A key benefit of designing an interposer is the ability to increase the density of the package whereby more components can be stacked, thus reducing the overall footprint of the final package.
An interposer takes one platform, substrate, or IC, and shrinks the size, while maintaining the functionality and performance, and shrinking the size by one-half, one-fourth, or one-third. As a result, you can use the smaller die or smaller substrate with the exact same form factor and functionality, thereby giving your precious real estate a lot more room to put other devices and components in your product. This means that a smaller package can perform considerably better even with a smaller physical footprint.
Interposers are becoming much more common these days; everybody is looking to save the real estate on the board. And as such, they're looking to reduce the size of the physical die or the placement of this device. Hence, the interposer.
In Figure 1, an interposer is used in this semiconductor application, increasing the package density and reducing the size.
Figure 1: Interposer increases BGA package density and reduces size. (Source: Wikipedia Creative Commons)
There are seven associated factors that ensure interposer efficiency and effectiveness.
- Assure the manner input/output (I/O) signals are used on both sides of the interposer to make the connections optimal. When done correctly, it increases the signal integrity (SI) and performance of the package as well.
- Determine the best method of fanning out the signals at different layers and different sections of the board. This includes calculating accurate trace and space widths, size of the vias used, and type of fan-out techniques. A package like a BGA with fine pitch balls needs to be fanned out using 2-3 mil traces, which can make the manufacturing more challenging. There must be a balance of trace widths/spaces, keeping in mind manufacturing limitations.
- Be mindful of good blind and buried via design practices and performance budgets, as needed while designing the interposer, making interposers more effective.
- Distribute the signal throughout the interposer area so that signals flow through properly, as well as make a uniform signal in terms of transmission and return paths. This would require matching trace lengths within 5–10% of each other.
- Keep the impedance control length matching uniform, and make sure there are no neck downs; be wary of dog boning or taking the traces out from the smaller areas of a BGA pad, because these neck downs create uneven traces. Be aware that traces smaller than 1–2 mils wide are more difficult to manufacture.
- Ensure that the interposer can be manufactured, whatever the intricate number of BGA layers and traces you create during the design phase. For example, traces meant for organic substrate like FR-4, polyimide, or Rogers can be of three mils or more; for an inorganic substrate interposer, traces could be one mil or even less in some cases. Inorganic substrates are typically made up of small polymers or molecules, glass, or silicon.
- Consider your fabrication material. In some cases, FR-4 may not be the best material with which to design an interposer due to thermal, electrical, and mechanical characteristics and limitations. In those cases, different materials like Arlon, Rogers, Teflon, or Bismaleimide Triazine (BT) material are candidates for use. Designers may find these other materials to be more conducive to the making of interposers.
Keep in mind that, whatever you chose, the material must be capable of dealing with those small geometries in your design. It also must withstand several heat cycles going through reflow ovens and different temperature ranges. In some cases, you may need to put stiffeners on the interposer to keep it flat and co-planar for the substrate to properly adhere to the die creating optimal assembly. This is especially true for large BGAs. Remember, you will have to design the stiffener along with the substrate design.
Therefore, the PCB microelectronics assembly house must be up to date on a variety of the latest design approaches and nuances associated not only with an interposer design, but also the interposer’s application. The assembly house must be properly equipped with state-of-the-art systems and equipment along with highly trained engineers and technicians to be able to assemble these interposer designs successfully.
Zulki Khan is the president and founder of NexLogic Technologies Inc.
More Columns from Zulki's PCB Nuggets
Zulki's PCB Nuggets: Cleanliness is Next to ReliabilityZulki’s PCB Nuggets: Thermal Compression Bonding for Extra Fine Pitch Flip Chips
Zulki’s PCB Nuggets: WBAN Steps Into PCB Microelectronics Assembly
Zulki’s PCB Nuggets: Photonics Comes to PCB Microelectronics Assembly
Zulki’s PCB Nuggets: Sub-Micron Die Bonding—Don’t Be Misled by Five Micron Placement Standard
Zulki’s PCB Nuggets: How Effective Is Your PCB Microelectronics Assembly?
Zulki’s PCB Nuggets: Five Key Benefits for Onshoring PCB Microelectronics Assembly
Zulki's PCB Nuggets: Onshoring for PCB Microelectronics Production?