-
- News
- Books
Featured Books
- design007 Magazine
Latest Issues
Current IssueProper Floor Planning
Floor planning decisions can make or break performance, manufacturability, and timelines. This month’s contributors weigh in with their best practices for proper floor planning and specific strategies to get it right.
Showing Some Constraint
A strong design constraint strategy carefully balances a wide range of electrical and manufacturing trade-offs. This month, we explore the key requirements, common challenges, and best practices behind building an effective constraint strategy.
All About That Route
Most designers favor manual routing, but today's interactive autorouters may be changing designers' minds by allowing users more direct control. In this issue, our expert contributors discuss a variety of manual and autorouting strategies.
- Articles
- Columns
- Links
- Media kit
||| MENU - design007 Magazine
Estimated reading time: 5 minutes
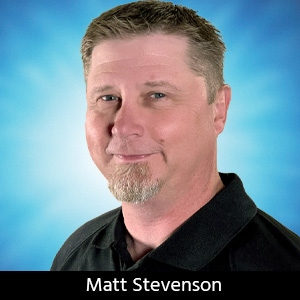
Connect the Dots: The Board Thickness Challenge
Size constraints, functional requirements, and environmental factors can make selecting PCB thickness difficult. Here we will examine best practices for choosing board thickness that results in quality, highly functional PCBs.
It’s Not Always as Easy as 1.57 mm
Industry standard or your design tool’s default board thickness are great places to start, but designers increasingly must consider using a custom board thickness. There are several factors to consider as you determine if a commonly used thickness will work. How thick does the board need to be to work? How thin must it be to fit into the device? What are its function and operating environment?
Thinner boards offer more flexibility and are preferable if keeping the device weight lower is a priority. Thicker is better if durability is an issue, because thick PCBs are less brittle and won’t break as easily. They also weigh more, run hotter, and will not work for many applications or assembly types. To determine thickness, you must consider how functional requirements will impact the number of layers you’ll need, as well as what signal and via types are needed.
The board’s operating environment is an equally important consideration. Is your board going into a wearable or handheld device that operates in a regulated environment or is it part of a Mars rover?
When your manufacturer receives a design, they can evaluate it before production to ensure its manufacturability and functionality, but very seldom are manufacturers made aware of how the board will eventually be used. It’s unlikely they’ll be able to judge whether a board, as designed, is too thick or too thin for the device it goes into or the environment in which it operates.
If, after evaluating these factors, you’re still not sure if a standard or common thickness will work for your design, here are some guidelines to help you choose what will work best for your board.
So, You Think You Need a Custom Thickness?
If you have read any of our other Design007 Magazine articles, you’re probably aware that we consider PCB design as much an art form as a science. As devices demand more and more from boards, PCB design becomes less straightforward. So, if determining thickness is proving difficult during the design phase, we recommend also considering these relevant factors.
First, can your PCB be manufactured as designed? Your manufacturer will have production tolerances. If your board is too thick or too thin, you’ll find yourself back at the drawing board.
PCB design is a game of millimeters. Thinner PCBs take up less space, so if you are building a device that will fit in your hand, go as thin as necessary to accommodate the space. And once inside the assembly, will it be adequately protected to function properly?
Protection from the operating environment is largely about extreme cold or heat. Heat that can threaten functionality doesn’t always come from operating in an environment like a car engine or industrial grade oven. Components themselves can generate enough heat to cause an issue, so be sure to determine if you need to prioritize thermal transfer or insulation as you contemplate board thickness.
PCB weight can be an issue more often than you might think. Is your board part of a cellphone, Bluetooth headset, or tablet device? Thinner boards are lighter and can help give your device that trim figure we all appreciate.
Pay careful attention to your connections. PCB edge connectors or PCB trace-based connectors, for example, require a board with thickness matched to fit in the mating portion of the connector. Some through-hole parts have pin lengths that limit board thinness.
Keep your ear to the ground for frequency concerns. Layer-to-layer thickness will affect signal integrity, crosstalk, impedance calculation, and signal loss. For high frequency signals, impedance control is a factor in determining the right thickness of your board.
There are trade-offs with board flexibility. Will your product be subjected to excessive shock and vibration? Thin boards that flex can cause broken connections or components, so be sure it’s properly supported in your assembly.
Decision Time: Thick or Thin?
Though the list of design considerations can theoretically go on forever, drawing conclusions about these factors will help with peace of mind about PCB thickness during the transition from design to prototyping. Following are our general recommendations about when to prioritize thicker or thinner boards.
Thicker Boards
- Your board needs to be durable or isn’t well protected in the assembly—or both
- Because of its size, the PCB needs to be stiff
- Your components require a certain amount of thickness
- You have a high layer count, more than six
- Your board is going in a tight space
- PCB weight is an issue
- If heat is a concern, thinner boards are better at dissipating heat. That’s because vias are shorter and pass through a smaller amount of insulation
- If your vias are very small and the board is too thick, drill bits will break before they make it through the board, making manufacture slower and more costly
Thinner Boards
Since cost is always a factor in our industry, we should note that standard thicknesses are less expensive. But if a standard thickness is not right for your design, we highly recommend customizing. Initial cost savings can go up in smoke if the boards aren’t durable enough because they’re too thin or prone to overheating because they are too thick.
Remember What You Learn About Board Thickness
And write it down. As you consider thickness in your design more often, we encourage crafting an easily replicated checklist approach to make this challenge easier in the future. Group what you learn into categories for easy reference. We recommend:
- Manufacturer tolerances
- Operating environment
- Thermal issues
- Size and weight constraints
- Frequency considerations
- The relationship between connections and board thickness
Your design can be spot on in every respect, but if it’s the wrong thickness it will likely fail and create costly rework. Before you send your design to your manufacturer, be sure your board is the right thickness for your needs.
This column originally appeared in the July 2021 issue of Design007 Magazine.
More Columns from Connect the Dots
Connect the Dots: Sequential Lamination in HDI PCB ManufacturingConnect the Dots: The Future of PCB Design and Manufacturing
Connect the Dots: Proactive Controlled Impedance
Connect the Dots: Involving Manufacturers Earlier Prevents Downstream Issues
Connect the Dots: Stop Killing Your Yield—The Hidden Cost of Design Oversights
Connect the Dots: Designing for Reality—Routing, Final Fab, and QC
Connect the Dots: Designing for Reality—Surface Finish
Connect the Dots: Designing for Reality—Solder Mask and Legend