-
- News
- Books
Featured Books
- design007 Magazine
Latest Issues
Current IssueProper Floor Planning
Floor planning decisions can make or break performance, manufacturability, and timelines. This month’s contributors weigh in with their best practices for proper floor planning and specific strategies to get it right.
Showing Some Constraint
A strong design constraint strategy carefully balances a wide range of electrical and manufacturing trade-offs. This month, we explore the key requirements, common challenges, and best practices behind building an effective constraint strategy.
All About That Route
Most designers favor manual routing, but today's interactive autorouters may be changing designers' minds by allowing users more direct control. In this issue, our expert contributors discuss a variety of manual and autorouting strategies.
- Articles
- Columns
- Links
- Media kit
||| MENU - design007 Magazine
Estimated reading time: 4 minutes
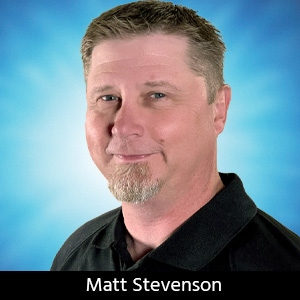
Connect the Dots: The ABCs of Clean Schematics
The production team is always excited when the first shipment of boards for a new electronic device comes back from the PCB manufacturer. Anticipation builds as the engineer connects the first set of components, puts everything together, and gets ready for that first test.
But when something goes wrong—a tiny pop, a sizzle, a puff of smoke, or nothing happens at all—the mood can turn from excitement to frustration. The engineer performs a postmortem and discovers a pinhole melted into the integrated circuit (IC), and then the culprit (a missing decoupling capacitor) led to a completely predictable voltage spike.
Where did the process go wrong? The engineer is certain that they put the capacitor in the right place. However, on closer examination, perhaps it is not close enough to the IC pad. Is it the fault of the PCB designer? Chances are that the designer will claim that they put the capacitor right where the schematic said it should be.
In a case like this, the fix is easy. The designer and the engineer get on the same page and produce a new design in 15 minutes. Unfortunately, the current batch of boards is now only useful as a set of coasters—delaying the project and potentially creating budget overruns.
This is a common issue for electronics manufacturers, and it is completely avoidable.
Good Schematics Are Good Communication
When engineers start to put together projects, the schematics are vital to good communication with the PCB designer. Theirs is a team effort. The schematic is where the engineer thinks through the project. However, by the time they hand it off to the designer, it needs to be a clean, comprehensible document that isn’t vague and doesn’t confuse. Most importantly, the engineer needs to communicate everything the PCB designer needs to design the right board for the project.
Best Practices Are There for a Reason
We all know that best practices exist, but real-world circumstances often lead to cutting corners. Saving time by ignoring best practices—like performing one last design check before submitting to the manufacturer—is just going to cost more time and money later. Even though it seems exhausting and repetitive, best practices involve starting at high-altitude block diagrams and then breaking each block into schematic sheets, checking flow and accuracy carefully, and then finally designing the board.
After that, a best practice has the engineer and designer picking over the design carefully, ensuring that it matches the specs—before it goes to the PCB manufacturer.
Designers Will Do What You Tell Them to Do
Engineers need to remember that designers don’t read minds; they read schematics. The engineer may understand implicitly the locations for all their bypass capacitors, but they can't rely on the designer's interpretation to properly place the elements. Instead, locate devices in roughly the manner of the final design to help the designer avoid bad interconnects, placement assumptions, or other errors.
It never hurts to provide the designer with explanatory notes about the elements. You will never hear a designer say that the engineer provided too much guidance for their work.
For example, utilize good naming conventions for connections or net names. Automated labels from design software are rarely helpful or intuitive. Create labels a human can understand.
Leverage Your Tools, But Don’t Use Them as a Crutch
Sometimes, engineers will give implicit connections using port symbols for the entire schematic. Unfortunately, this practice leaves no trail for the designer to follow. While the engineer may have saved a couple of minutes, the designer spends more time sorting out the nest of connections.
Let the software be on your side. It tracks and confirms those connections for a reason. This may feel like an obstacle for the engineer, but for the overall project, these tools are a lifeline.
The design rule check (DRC) is another example where the tool exists, but results may get ignored in the interest of saving some time. Too often, issues are ignored because they seem unimportant. However, over time these errors build up and create a confusing mess that may obscure errors that are truly important. One of your team's best practices should be generating a DRC report that reads no warnings and no violations.
More Recommendations for Clean Schematics
In addition to the broader best practices of fostering good communication and not relying too much on technology, the following are key methods that help ensure a clean schematic and a manufacturable, functional PCB design.
- Design the schematic in the design program and label all connects with comprehensible net names—no auto-generated names
- Lay out the schematic in a manner that clarifies locations
- Label the schematic so that the next person can understand it
- Create an environment where designers are comfortable asking for clarification if they are uncertain how to proceed
- Use the DRC and address the warnings and violations it reports
Well-designed schematics will save time, money, and frustration both for your current project and future endeavors. If your schematic is nice to look at and easy to understand, your team can utilize blocks for other similar projects down the road. Teams that commit to good schematic practices win the long game.
Commit to Best Practices and Good Process
We all want to create great final products. Designers want to make great boards. Engineers want to make great schematics. To get there, we also need to think about making the work of the next person easier. When you commit to best practices, clear communication, and clean schematics, everyone benefits.
This column originally appeared in the October 2022 issue of Design007 Magazine.
More Columns from Connect the Dots
Connect the Dots: Sequential Lamination in HDI PCB ManufacturingConnect the Dots: The Future of PCB Design and Manufacturing
Connect the Dots: Proactive Controlled Impedance
Connect the Dots: Involving Manufacturers Earlier Prevents Downstream Issues
Connect the Dots: Stop Killing Your Yield—The Hidden Cost of Design Oversights
Connect the Dots: Designing for Reality—Routing, Final Fab, and QC
Connect the Dots: Designing for Reality—Surface Finish
Connect the Dots: Designing for Reality—Solder Mask and Legend