-
- News
- Books
Featured Books
- design007 Magazine
Latest Issues
Current IssueProper Floor Planning
Floor planning decisions can make or break performance, manufacturability, and timelines. This month’s contributors weigh in with their best practices for proper floor planning and specific strategies to get it right.
Showing Some Constraint
A strong design constraint strategy carefully balances a wide range of electrical and manufacturing trade-offs. This month, we explore the key requirements, common challenges, and best practices behind building an effective constraint strategy.
All About That Route
Most designers favor manual routing, but today's interactive autorouters may be changing designers' minds by allowing users more direct control. In this issue, our expert contributors discuss a variety of manual and autorouting strategies.
- Articles
- Columns
- Links
- Media kit
||| MENU - design007 Magazine
Estimated reading time: 5 minutes
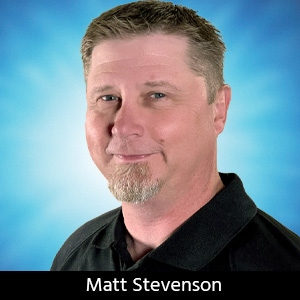
Connect the Dots: What is an Annular Ring?
Let's learn about annular rings, because a greater understanding can help ensure that your PCB designs successfully become physical boards. The annular ring is the space between the drill hole and the edge of the pad—a specified minimum gap around the drill hole. Don't get the impression that an annular ring is a separate part. The term is used to describe the portion of the copper pad that remains after a hole is drilled through the pad. The annular ring of a pad is measured from edge of hole to edge of pad.
Annular rings serve a variety of purposes, and improperly sized annular rings can cause serious PCB concerns. In addition to causing shorts, small or nonexistent annular rings can create significant manufacturing delays and board reliability issues.
What does an annular ring do?
One of the most important aspects of an annular ring is that it keeps a through-hole within the boundaries of a pad. This is crucial for solid construction and connectivity between leads, pads, and traces. An annular ring prevents a plated through-hole from shorting to the ground layer as well. On the outer layer of a PCB, the annular ring helps ensure solid construction of the entire board.
Planning for properly sized annular rings gives the PCB fabrication process room for drift—within tolerances.
In order to plan for sufficiently sized annular rings, these are the recommended pad sizes:
Inner and outer layer pads should be at least 18 mil larger than the finish hole size, though via pads only need to be 10 mil larger (typically the non-via holes are drilled larger than the finished hole size, where vias will be drilled at the finished hole size).
If the design includes any pad to trace junction minimum requirement or a higher IPC inspection class requirement, that will need to be accounted for in the pad design. For example, an 18-mil pad and a 2-mil junction should actually have a 20-mil pad. These sizes should end up creating a 9-mil annular ring target for leads and a 5-mil annular ring for vias to allow for process variation and still meet the requirements.
If you have all the needed numbers from your PCB manufacturer, you can use the following equation to calculate your minimum pad sizes.
L = a + 2b + c
Where:
- L is the required via land size
- a is the internal diameter of the drill hole
- b is the minimum annular ring size
- c is the fabrication allowance or allowed drift for the drills
What happens when annular rings are too small?
It is easy to see why annular ring size can be a problem. Many times, designers want to use the largest through-hole drills to save cost. At the same time, they want to pack their designs tightly so that the required PCB can be smaller. However, larger drill holes mean larger annular ring requirements. Good design requires being aware of the needed trade-offs.
That’s because an annular ring that is too small can cause manufacturing and quality issues. One of the most common is breakout, when the drill hole crosses over the edge of the pad. Breakout can be a serious issue because it can lead to shorts and poor connection between the lead and the pad.
Too-small annular rings can also cause longevity issues for a PCB. While the PCBs may work great at first, the small annular ring could cause a failure somewhere down the line.
Usually, though, when annular rings are too small, the PCB will encounter shorts or just simply won't work. There have been instances where small annular rings caused an "unintended thermal fuse situation"—that's right, the PCB caught on fire.
How common are undersized annular rings in PCB manufacturing?
Ideally, a PCB design will be reviewed for issues like undersized annular rings before it hits the manufacturing floor. This review helps ensure the PCB can be created within IPC specifications. IPC-A-600 covers the acceptability of printed boards, while IPC-6012E governs "rigid printed boards." They both define different classifications for minimum annular ring requirements.
For example, in IPC-A-600, the different classes define requirements as follows:
- Class 3: No breakout, though holes are not centered in the pads; the annular ring measures 2 mil or more.
- Class 2: 90° breakout or less, with the conductor junction measuring 2 mil or more.
- Class 1: 180° breakout or less, as long as the conductor junction is not reduced by more than 30%.
Note that only Class 3 requires some amount of leftover annular ring. A quality-focused manufacturer will do everything it can to meet that requirement.
Unfortunately, undersized or absent annular rings are very common in PCB designs. We sometimes see as many as 30% of jobs in the queue put on hold for annular ring issues. This can delay production for hours while the designer and manufacturer work to resolve the issue.
You can avoid annular ring problems in your PCB designs by carefully considering the drill size and pad sizes you want to use. This can certainly affect cost, but it may be worth the difference. Note that your PCB design software probably has configuration settings for minimum annular ring widths. Make sure these settings match IPC-A-600 Class 3, and you should be ready to go.
Another option you can use to avoid annular ring issues and reduce the chance of breakout is to add teardrops to your pads and traces. This can be a very effective method for reducing annular ring issues.
It’s important to remember that annular rings play a crucial role in PCB functionality and reliability. Poorly planned and under-sized annular rings are a leading cause of PCB manufacturing delay. By realizing these important facts and by planning ahead, you can keep annular rings from derailing your PCB manufacturing plans, budgets, and timelines.
At Sunstone, Matt Stevenson is vice president, Kevin Beattie is a production manager, and Karla Thompson is a CAM manager.
Download The Printed Circuit Designer’s Guide to... Designing for Reality by Matt Stevenson.
This column originally appeared in the May 2023 issue of PCB007 Magazine.
More Columns from Connect the Dots
Connect the Dots: Sequential Lamination in HDI PCB ManufacturingConnect the Dots: The Future of PCB Design and Manufacturing
Connect the Dots: Proactive Controlled Impedance
Connect the Dots: Involving Manufacturers Earlier Prevents Downstream Issues
Connect the Dots: Stop Killing Your Yield—The Hidden Cost of Design Oversights
Connect the Dots: Designing for Reality—Routing, Final Fab, and QC
Connect the Dots: Designing for Reality—Surface Finish
Connect the Dots: Designing for Reality—Solder Mask and Legend