-
- News
- Books
Featured Books
- pcb007 Magazine
Latest Issues
Current IssueSales: From Pitch to PO
From the first cold call to finally receiving that first purchase order, the July PCB007 Magazine breaks down some critical parts of the sales stack. To up your sales game, read on!
The Hole Truth: Via Integrity in an HDI World
From the drilled hole to registration across multiple sequential lamination cycles, to the quality of your copper plating, via reliability in an HDI world is becoming an ever-greater challenge. This month we look at “The Hole Truth,” from creating the “perfect” via to how you can assure via quality and reliability, the first time, every time.
In Pursuit of Perfection: Defect Reduction
For bare PCB board fabrication, defect reduction is a critical aspect of a company's bottom line profitability. In this issue, we examine how imaging, etching, and plating processes can provide information and insight into reducing defects and increasing yields.
- Articles
- Columns
- Links
- Media kit
||| MENU - pcb007 Magazine
Estimated reading time: 3 minutes
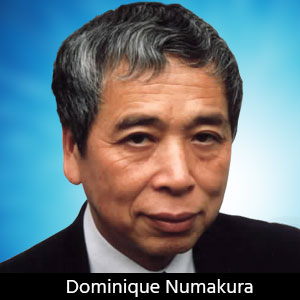
The Drive for Transparent Circuits
DKN Research develops many types of unique electronic circuits. Some products in our portfolio include ultra-thin conductor circuits as small as 0.2 microns, metal-free circuits, and some circuits up to 20 meters long. Our staff fields many inquiries for packaging of new electronic devices. Lately, there is a lot of interest in transparent flexible circuits. The increase in interest is driven by the recent market expansion of display and optical devices.
One example of this is the touchscreen display for tablet PCs and smartphones. When Apple launched the iPod Touch, touch screen displays became the benchmark for the industry. The flexible circuits found inside must be transparent so the user can see the LCD panel. Unfortunately, the most popular substrate material used in flexible circuits is polyimide film, because it is brown in color and not optically transparent. Circuit manufacturers use PET films instead of polyimide films because its heat resistance is remarkably lower than polyimide film. Circuit manufacturers had to develop a low-temperature process using the correct materials to make this a success. After many trials, PET films are the standard substrate material for touchscreen displays in mobile devices.
Many applications for industrial and aerospace devices demand both transparency and heat resistance. Up until now, this was not possible. Recently, a Japanese plastic manufacturer developed a process using transparent polyimide film as the main substrate for flex circuits in a volume application setting. This will remove a technological barrier for heat resistance and is a huge progress for transparent circuits.
Many are asking if transparent flexible circuits are practical on a commercial scale. The answer could be yes, if we can push through one more barrier: identifying a transparent conductor. Copper foils are the major conductor material for printed circuit boards, but they are not transparent. Indium tin oxide (ITO) was used as an alternative transparent conductor for most of the display devices, because it can be sputtered at relatively low temperatures. Its conductivity is much lower compared to metallic copper, so many researchers are trying to develop conductive organic molecules for this purpose. Other researchers are considering the use of carbon nanotubes or graphene as the transparent conductor; unfortunately, their conductivities are not much greater than ITO, and other problems need to be addressed before any commercial application is considered. Currently, silver nanowire and thin metallic mesh screen may be the key, even though those materials are not transparent. Creating appropriate opening turns the materials transparent with higher conductivities. This is not the perfect solution, but it is practical. That’s why I am optimistic that transparent flexible circuits are practical on a commercial scale.
A few smaller challenges that need to be addressed center on cover materials and adhesive materials. These secondary materials can be made transparent with a few minor changes based on their current performances.
We can now create several types of heat-resistant, transparent flexible circuits by using a few different combinations. The only thing I can’t tell you is how much all of this will cost—the cost structures for most of the materials have not been determined.
To read back issues of the newsletter, click here.
Headlines of the Week
1. Yaskawa Electric (major equipment manufacturer in Japan) 7/2
Has commercialized a new spot-welding robot, MOTOMAN-VS100, for automobile assembly. It features seven rotating modes.
2. Fuji Electric (major electric company in Japan) 7/2
Has rolled out a new steam generation heat pipe. It can utilize low-temperature waste water.
3. Hitachi (major electric and electronics company in Japan) 7/3
Has begun volume production of one-chip distortion sensors utilizing a metal-bonding technology for automobile applications.
4. AIST (R&D organization in Japan) 7/7
Has developed an ultra-high-density capacitor device using mono-layer carbon nano tube. The size can be one thousandth of an aluminum capacitor.
5. Toshiba (major electric and electronics company in Japan) 7/8
Has developed a new multilayer magnetic memory system. It will enlarge the memory capacity of hard disc drives significantly.
6. Mitsubishi Electric (major electric company in Japan) 7/14
Has commercialized a new heavy-duty robot series. The largest robot can handle 70 kg.
7. AIST (R&D organization in Japan) 7/10
Has been co-developing a new hydrogen base power generation system using aluminum waste materials.
8. Mitsubishi Motors (major automobile manufacturer in Japan) 7/10
Has agreed to start commercial base field test of the electric power storage system with French companies. The test will be conducted in Paris, France.
9. Daikin (equipment manufacturer in Japan) 7/14
Has begun field testing a micro hydroelectric power generation system that utilizes the power of city water and sewage.
10. Rohm (major device manufacturer in Japan) 7/14
Has developed the world’s smallest (2mm x 2mm) pressure sensor, BM1385GLV, with a high precision for mobile devices and wearable devices.
To read the full articles, click here.
To reach Dominique K. Numakura, visit www.dknresearchllc.com or email dnumakura@dknresearch.com.
More Columns from EPTE Newsletter
EPTE Newsletter: Travel to Japan During COVIDEPTE Newsletter: A New COVID Surge in Taiwan?
EPTE Newsletter: COVID-19 PCR Test in Japan
EPTE Newsletter: Japan Failing in Vaccine Distribution
EPTE Newsletter: A Long Trip to the U.S.
EPTE Newsletter: Ten Years After Fukushima
EPTE Newsletter: Taiwan Releases 2020 PCB Production Numbers
EPTE Newsletter: The Printed Circuit Industry in China