-
-
News
News Highlights
- Books
Featured Books
- pcb007 Magazine
Latest Issues
Current IssueSales: From Pitch to PO
From the first cold call to finally receiving that first purchase order, the July PCB007 Magazine breaks down some critical parts of the sales stack. To up your sales game, read on!
The Hole Truth: Via Integrity in an HDI World
From the drilled hole to registration across multiple sequential lamination cycles, to the quality of your copper plating, via reliability in an HDI world is becoming an ever-greater challenge. This month we look at “The Hole Truth,” from creating the “perfect” via to how you can assure via quality and reliability, the first time, every time.
In Pursuit of Perfection: Defect Reduction
For bare PCB board fabrication, defect reduction is a critical aspect of a company's bottom line profitability. In this issue, we examine how imaging, etching, and plating processes can provide information and insight into reducing defects and increasing yields.
- Articles
- Columns
- Links
- Media kit
||| MENU - pcb007 Magazine
Estimated reading time: 4 minutes
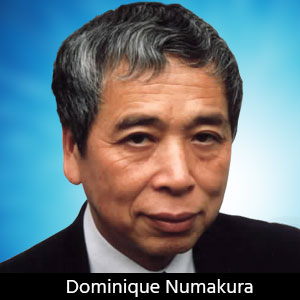
Deadly Blast in China
Earlier this month, there were two massive explosions in the port of Tianjin, northern China. As soon as officials blamed the explosions on negligent activity, my thoughts immediately went back to my consulting days in China.
The Chinese companies that I provided consulting services to were manufacturers of printed circuit boards. I was tasked with visiting their manufacturing plants and providing recommendations to improve quality and productivity at the plants. I was given complete access to every area in the plant, and allowed to interview all the staff, from laborers to senior managers. Unfortunately, the language barrier proved to be difficult when interviewing most of the employees.
I reviewed not only manufacturing processes, but also scrutinized the inspection and packaging lines, warehouse operations, and other related facilities. Conditions at the plant were sub-par. Most of the equipment and machinery were very old, and it was common to see puddles of chemicals leaking from pipes. The conveyers vibrated so much that a lot of material was damaged during transit. The clean rooms were monitored through windows, but this didn’t stop the operators from eating, drinking and smoking; there were enough blind spots to hide in.
Safety was not a primary concern when storing raw materials and chemicals. Most were piled up to the ceiling in storage rooms without any organization, while other materials were kept in aisles between conveyer belts. Even more surprising was the use of elevators for chemical storage space when no other room was available. It was not uncommon to see chemicals spilling out of broken containers and left to dry on their own.
There was a lot of wasteful spending on machinery. I came across two brand-new NC drilling machines still in the original packaging. I found out that a few parts and manuals were missing, and no one could figure out how to bring the machines on line. The process manager had to outsource the drilling.
The floors throughout the plant were dirty and stained with chemical remnants. There were only two clean and organized areas in the whole building—the reception area and the president’s office. The rest of the administrative offices were in poor condition—broken furniture, cluttered desks—complete chaos. Ironically, one mid-level manager told me the furniture was very cheap and did not last long because it was made in China!
I completed my report and presented it to the company’s president of operations. He did not read the report; instead, he asked me to review it with the plant manager. The plant manager reviewed the report, but was not open-minded to any improvements listed within it. He was full of excuses and blamed most of the machinery problems on the maintenance department, blamed the facility cleanliness on the janitorial department, and shifted blame onto the procurement manager for storage problems. He also blamed the procurement manager for purchasing sub-par, low-cost materials from local vendors (Chinese).
Most of the workers recognized all these problems, but had no say in fixing or improving conditions. Worker morale continued to erode and was reflected in the quality of production.
The quality of products made in China has improved over the years, but factory and worker conditions may not be keeping up. Without safeguards in the workplace, tragedies are bound to happen in plants that work with hazardous and flammable chemicals.
To read back issues of the newsletter, click here.
Headlines of the week
(Please contact haverhill@dknreseach.com for further information of the news.)
1. Panasonic (Major electronics company in Japan) 8/6
Has started volume production of curved touch panel screens for automobiles. They provide more design freedom in the cabin.
2. Yamaha Motors (Major motor cycle manufacturer in Japan) 8/6
Has founded a new subsidiary, YMVLSV (Yamaha Motor Venture & Laboratory Silicon Valley Inc.), for R&D for vehicles, robotics, and industrial solutions.
3. Mitsubishi Chemical (Major chemical company in Japan) 8/7
Has started marketing of see-through type organic solar cell film. Mitsubishi expects a remarkable market at modern buildings in downtown areas.
4. AIST (R&D organization in Japan) 8/12
Has developed a new flexible but tough transistor with mono-layer carbon nanotube. It could be valuable for the wearable sensor devices.
5. TIT (Technical institute in Tokyo, Japan) 8/17
Has developed a tiny low temperature plasma jet with metallic titanium using a 3D printing process. It could be valuable for medical devices.
6. Sumitomo Electric (Major cable manufacturer in Japan) 8/21
Has developed a new coaxial cable, capable of 40 Gb/sec for next generation Thunderbolt. It is USB-compatible. Sumitomo plans volume production starting March 2016.
7. Yokohama Rubber (Major rubber product supplier in Japan) 8/21
Has commercialized a new color filter film “YF-Z Series” for displays and industrial applications. The films cut blue lights with 350–400 nm wave length.
8. RIKEN (R&D organization in Japan) 8/21
Has co-developed a new FPP (Fine Particle Peening) process. It makes nano-size dimples mechanically on solid surface without laser and photolithography.
9. Toshiba (Major electric & electronics company in Japan) 8/24
Has commercialized a new intelligent power module “TLP 2704” with thin SO6L plastic package for FA equipment. Mounting height: 2.3 mm.
10. AIST (R&D organization in Japan) 8/26
Has co-developed a new heat insulation alumina film through simple nano-fiber sol process with Kawaken Fine Chemical. It reflects over 70% of visible and IR light.
To read the full articles, click here.
To reach Dominique K. Numakura, visit www.dknresearchllc.com or email dnumakura@dknresearch.com.
More Columns from EPTE Newsletter
EPTE Newsletter: Travel to Japan During COVIDEPTE Newsletter: A New COVID Surge in Taiwan?
EPTE Newsletter: COVID-19 PCR Test in Japan
EPTE Newsletter: Japan Failing in Vaccine Distribution
EPTE Newsletter: A Long Trip to the U.S.
EPTE Newsletter: Ten Years After Fukushima
EPTE Newsletter: Taiwan Releases 2020 PCB Production Numbers
EPTE Newsletter: The Printed Circuit Industry in China