-
-
News
News Highlights
- Books
Featured Books
- pcb007 Magazine
Latest Issues
Current IssueThe Hole Truth: Via Integrity in an HDI World
From the drilled hole to registration across multiple sequential lamination cycles, to the quality of your copper plating, via reliability in an HDI world is becoming an ever-greater challenge. This month we look at “The Hole Truth,” from creating the “perfect” via to how you can assure via quality and reliability, the first time, every time.
In Pursuit of Perfection: Defect Reduction
For bare PCB board fabrication, defect reduction is a critical aspect of a company's bottom line profitability. In this issue, we examine how imaging, etching, and plating processes can provide information and insight into reducing defects and increasing yields.
Voices of the Industry
We take the pulse of the PCB industry by sharing insights from leading fabricators and suppliers in this month's issue. We've gathered their thoughts on the new U.S. administration, spending, the war in Ukraine, and their most pressing needs. It’s an eye-opening and enlightening look behind the curtain.
- Articles
- Columns
- Links
- Media kit
||| MENU - pcb007 Magazine
Latest Articles
Ventec: Contextualizing the CHIPS Act
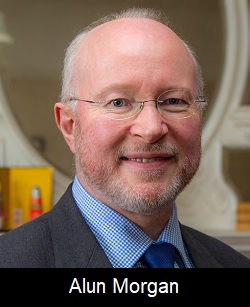
Real Time with… IPC APEX EXPO 2023: Burkle Preps for Biggest Show Ever
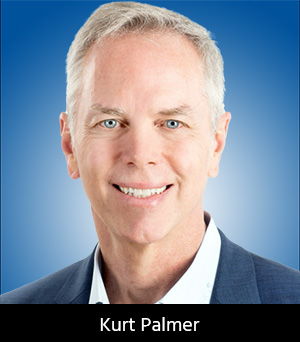
IPC APEX EXPO 2023 Special Session Sneak Peek
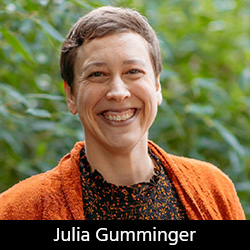
Preventing De-wetting Defects In Immersion Tin Soldering
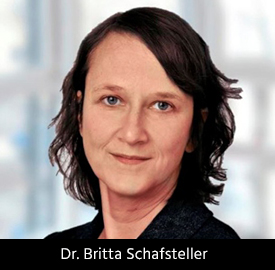
'Happy New Year' Celebrations Around the World
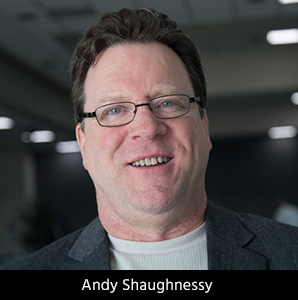
I-Connect007 Editor's Choice: Five Must-Reads for the Week
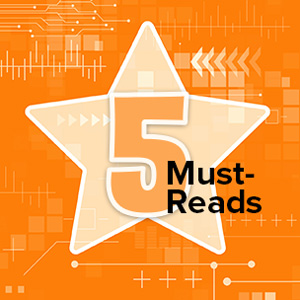
Reconnecting the Social Network
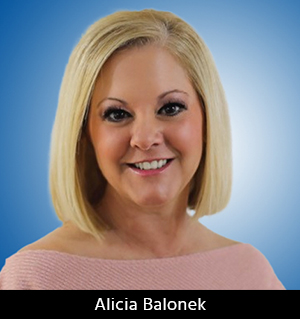
The Five Most-read Design007 News of 2022
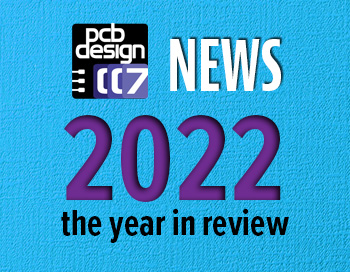
Essemtec: Manufacturing Moves In-house
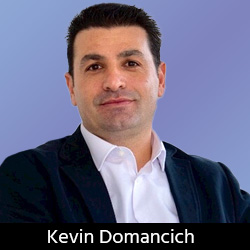
Let’s Get Technical
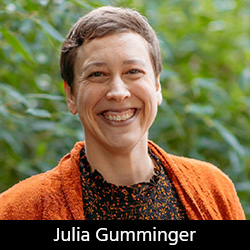
The Five Most-read Design007 Articles of 2022
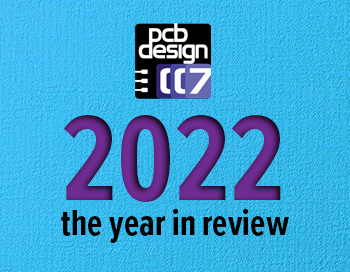
The Most-read I-Connect007 Articles of 2022
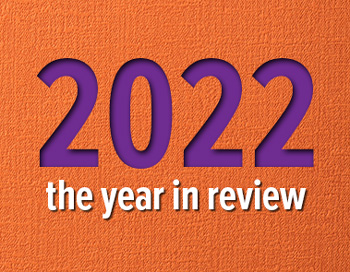
I-Connect007 Editor's Choice: Five Must-Reads for the Week
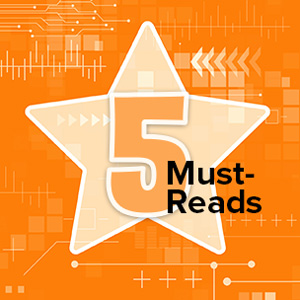
Workflow Challenges in Fabrication
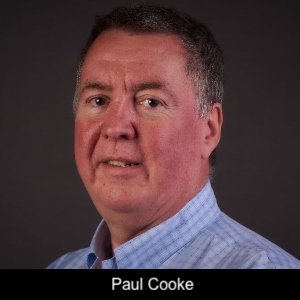
EIPC Technical Snapshot: ‘There Is No Green Without Digital’
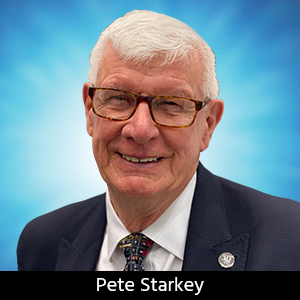
Candor: UHDI Under Development
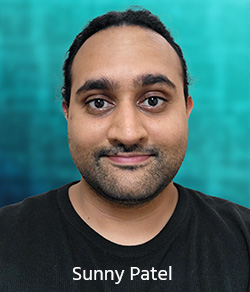
MKS Discusses the Cutting Edge of Technology
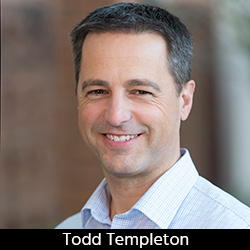
The First India Pavilion
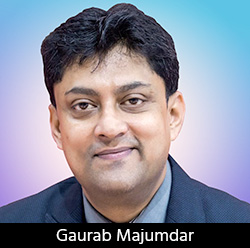
Taiyo: Reopening Europe for Solder Mask
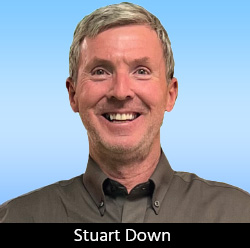
Aismalibar: Cooling Off With Thermal Interface Materials
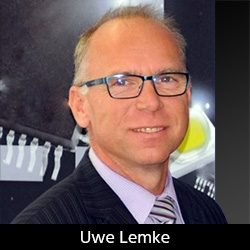
I-Connect007 Editor’s Choice: Five Must-Reads for the Week
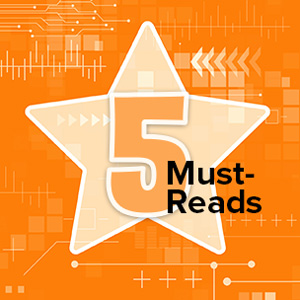
A New Gathering Place for Designers
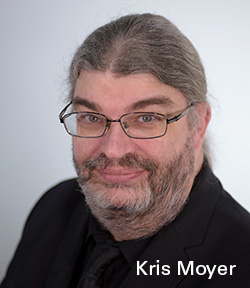
EIPC: Europe’s Energy Disadvantage
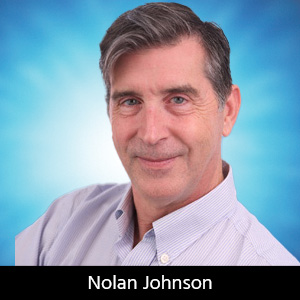
ICT Christmas Seminar 2022: The Caliber of a ‘World Cup’ Event
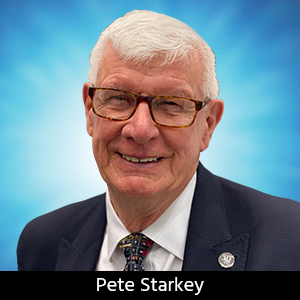
Rogers: Bringing New Materials to Light
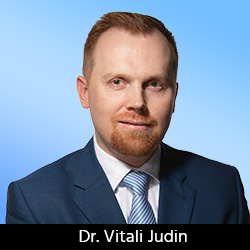