-
-
News
News Highlights
- Books
Featured Books
- design007 Magazine
Latest Issues
Current IssueAll About That Route
Most designers favor manual routing, but today's interactive autorouters may be changing designers' minds by allowing users more direct control. In this issue, our expert contributors discuss a variety of manual and autorouting strategies.
Creating the Ideal Data Package
Why is it so difficult to create the ideal data package? Many of these simple errors can be alleviated by paying attention to detail—and knowing what issues to look out for. So, this month, our experts weigh in on the best practices for creating the ideal design data package for your design.
Designing Through the Noise
Our experts discuss the constantly evolving world of RF design, including the many tradeoffs, material considerations, and design tips and techniques that designers and design engineers need to know to succeed in this high-frequency realm.
- Articles
- Columns
- Links
- Media kit
||| MENU - design007 Magazine
Estimated reading time: 5 minutes
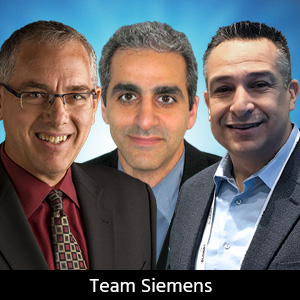
Digital Transformation: Optimizing Co-Design Across Multiple Domains
This series of columns has explored multiple approaches to achieving a digital transformation within the electronics design process. This time I’d like to look at design and collaboration across multiple domains (e.g., electronics, electrical, and mechanical) and how a digital thread enables that.
Higher system speeds have necessitated consideration of signal propagation delay and quality not just within electronics, but through wire harnesses. Tighter form factors have minimized the typical “board in a box,” where a simple rectangular board had enough clearance that there were rarely problems. Rigid-flex circuits often stress cross-domain ECAD/MCAD design with their multiple stackups and bendability. Even if form/fit is achieved, high-performance systems with significant heat dissipation need to ensure adequate air/fluid flow through the structure.
Emerging technologies like additive manufacturing will drive further alignment between domains; for example, there is the potential to print interconnects in automotive body panels instead of using cabling and wire harnesses or electronics molded to the contours of instrumentation panels.
Figure 1: Multi-domain design flow.
The worlds of the electronics, electrical, and mechanical domains are similar and unique at the same time. Electronics design (hardware systems) and electrical design (the wiring between hardware to create larger electronic systems) naturally work together and have often been confused since they’re both called “ECAD,” and both employ electrical engineers who start a design with a schematic. Both electrical and electronics design share common challenges when integrating with mechanical design.
Historically, cross-domain collaboration was inhibited by a number of issues. The different domains had completely different tool chains, user specialties, languages/terms for communication, and databases. This made it difficult to communicate changes while both domains proceeded in parallel. The best that could be expected was email, drawings on post-it notes, or “voice-driven mouse” (assuming they’re in the same facility). Design complexity has also driven use of multi-discipline simulations of the digital twin (e.g., signal/power integrity, electromagnetics, thermal, structural, and acoustics) to minimize iterations and optimize products, but data transition into those tools is inhibited by the same problems. The net result was infrequent communication, with limited or no digital verification. It wasn’t unheard of to wait until system integration to realize things didn’t fit. Aberdeen studies have shown that 59% of complex products will require at least two additional design iterations to address electro-mechanical problems. Sixty-eight percent of companies cite electro-mechanical data synchronization as a significant challenge.
The industry has evolved, providing a digital thread in the form of industry standard formats. Decades ago, DXFs became a common way to pass graphical data, but the information was very limited (often 2D, no intelligence about objects), thus requiring interpretation, so it was typically used only in a one-way path from MCAD to ECAD. STEP enabled more 3D intelligence, including enclosures. IDF was constructed for bi-directional collaboration, but it transferred the entire database without any tracking to identify changes. IDX gave us the ability to send incremental changes and traceability. To optimize collaboration even further, some tool pairs provide data integration beyond even these standard formats. This is a positive step but requires synchronization of all tool releases in the chain. Some companies have created tools that merge domains but lack sufficient depth, so these are limited to generalist use on simpler designs.
Today, most tools support multiple formats, yet adoption of the most advanced approaches is limited. Some of this is due to organizational inertia—it’s difficult to change processes, particularly when custom code may have been created to peanut-butter over inefficiencies. It’s even harder to change if multiple domains are involved, with their siloed teams and unique tool chains.
Yet the promise of optimized co-design across multiple domains enabled by a digital thread is significant. Studies show that best-practice processes can reduce physical prototypes and respins through consistent, iterative communication to avoid rework late in the design process. Engineering efficiency can be significantly increased, reducing development cost and time. First-pass success is much more likely. More robust designs can be created through extensive collaboration and verification.
Let’s review the benefits of optimized cross-domain co-design:
Increased productivity
- Enables “what if” scenarios to avoid time-consuming design iterations
- Allows ECAD and MCAD designers to co-design in their own environments without learning new tools
- Provides more time for new projects due to fewer design iterations
Improved design robustness
- Facilitates the optimization of today’s complex compact form factors
- Ensures higher quality, reliability, and performance with early verification of the digital twin
- Inherently less error prone and therefore reduces risk
Increased collaboration and efficiency
- Provides consistent, iterative communication throughout the development process
- Accelerates decision making to mutually agreed changes
- Left-shifts 3D clearance and collision checking into the ECAD domain
Achievable first-pass success
- Provides an integrated process to avoid rework due to electro-mechanical issues
- Reduces design iterations by verifying design intent throughout the development process
- Increases the probability of meeting the product launch target
So, what does a best-practice deployment look like? Here are a few recommendations:
- Obviously, the tighter the connection between tools in each domain, the cleaner the data transition and the higher the collaboration efficiency. The industry standard for electro-mechanical integration is IDX, facilitating frequent, incremental collaboration. But as noted, even tighter integrations are possible.
- A model-driven approach, with both ECAD and MCAD sharing the same component library, can save significant library creation time and ensure that all of engineering is on the same page.
- 3D ECAD design tools enable layout designers to view what the mechanical engineer is working on without leaving their native environment and verify their design in that context. Likewise, PCB data down to the trace and via levels helps the mechanical engineer accurately model and simulate the board in their environment. On that point, as noted earlier, there are a number of analysis tools available to validate the digital twin before prototype. Ideally, these work directly off the ECAD or MCAD authoring database (a high-fidelity digital twin) to minimize rework. While adopting these tools sounds like extra work, it’s been proven that “virtual prototyping” (analysis and verification during design) saves significant time and cost through respin reduction.
Take a look at your current cross-domain design process with an eye for inefficiencies. It may be “working” today (i.e., nobody’s complaining), but a few steps can dramatically improve your engineering team’s performance.
This column originally appeared in the September 2022 issue of Design007 Magazine.
Additional content from Siemens Digital Industries Software:
- The Electronics Industry’s Guide to... The Evolving PCB NPI Process by Mark Laing and Jeremy Schitter
- The Printed Circuit Designer’s Guide to... Stackups: The Design within the Design by Bill Hargin
- The Printed Circuit Assembler's Guide to... Smart Data: Using Data to Improve Manufacturing?by Sagi Reuven and Zac Elliott
- The Printed Circuit Assembler's Guide to… Advanced Manufacturing in the Digital Age?by Oren Manor
- The Printed Circuit Designer’s Guide to… Power Integrity by Example by Fadi Deek
- Siemens’ 12-part, on-demand webinar series?“Implementing Digital Twin Best Practices?From?Design Through Manufacturing”
- Rountable: RealTime?with...?Siemens and Computrol: Achieving Operational Excellence in Electronics Manufacturing
- You can also view other titles in our full I-007eBooks library.
More Columns from Digital Transformation
Digital Transformation: Leveraging Digital Automation to Accelerate PCB DesignDigital Transformation: Unblocking Innovation With a Component Digital Thread
Digital Transformation: Supply Chain Resilience, Part Two—The Solution
Digital Transformation: Supply Chain Resilience, Part 1—The Supply Chain Problem
Digital Transformation: Enabling a Digital Thread Across IC/Package/PCB Design
Digital Transformation: The Digital Transformation of Advanced Additive Electronics
Digital Transformation: Leveraging Model-Based Engineering to Manage Risk, Part 2
Digital Transformation: Leveraging Model-based Engineering to Manage Risk