-
- News
- Books
Featured Books
- smt007 Magazine
Latest Issues
Current IssueSupply Chain Strategies
A successful brand is built on strong customer relationships—anchored by a well-orchestrated supply chain at its core. This month, we look at how managing your supply chain directly influences customer perception.
What's Your Sweet Spot?
Are you in a niche that’s growing or shrinking? Is it time to reassess and refocus? We spotlight companies thriving by redefining or reinforcing their niche. What are their insights?
Moving Forward With Confidence
In this issue, we focus on sales and quoting, workforce training, new IPC leadership in the U.S. and Canada, the effects of tariffs, CFX standards, and much more—all designed to provide perspective as you move through the cloud bank of today's shifting economic market.
- Articles
- Columns
- Links
- Media kit
||| MENU - smt007 Magazine
Estimated reading time: 4 minutes
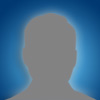
Contact Columnist Form
Conclusion: The Outsourcing Option
By Ray P. Prasad
"Set up a team armed with in-house selection procedure and a detailed questionnaire to select quality suppliers."
In this column we will discuss examples of questions to assess supplier capabilities in manufacturing and quality.
Questions to determine a supplier's manufacturing capability should relate to capacity and use of the manufacturing equipment, material control and handling methods, equipment operating procedures, equipment maintenance and calibration schedules, and operator training. Questions on these and similar matters should cover each type of equipment in use at the supplier's facility.
The type of equipment a supplier uses can give a good idea about capabilities. How the equipment is organized is a good indicator of the contractor's awareness of manufacturing processes. Good quality in-line equipment is preferable to batch equipment for automation. Is the supplier set up for quick turn, if applicable? Is in-line production equipment used for prototype jobs? If yes, does it create delivery slippage on quick turn?
As a general guideline, if in-line production machines are used for "quick-turn" prototype work, the supplier is not set up for quick turn. Delivery problems will be found either on the quick turn or production lot or both. On the other hand, flexible tooling that can be set up quickly for small jobs indicates that the supplier truly is set up for quick turn prototypes. What other equipment is con-sidered, as well as why the firm bought a particular brand and model also are considerations.
Observe the equipment's performance in operation. How often is it down for repair? How accurate is pick-and-place equipment? Does the X-Y table move during placement? Does that cause misplacement? Is the pick-and-place data transferred electronically or is the "teach in" method used for programming? "Teach in" is a sure sign of future problems. How closely can the solder profile be controlled? Is there a unique profile for each product? If not, why?
Does the screen printer print well and consistently? How effective is soldering and cleaning equipment in resulting in good, clean boards? Batch vs. in-line cleaning for surface mounting should be investigated closely. With tighter spacing among components and lower standoff heights above board, in-line cleaning systems with sufficient nozzle pressure are effective in providing boards free of solder balls and flux residues. If no-clean solder paste and wave flux are used, how are solder balls avoided or removed? Has the touch-up rate increased with no-clean flux and paste? How was the transition made to no-clean? No-clean is not a "drop in" process. It requires considerable groundwork to make the switch.
If high-volume rework is important, does the supplier have an automated rework system for removing and replacing components such as BGAs, CSPs and fine pitch? How is reflow of adjacent components prevented while reworking boards where components are tightly packed?
Finally, having the best equipment is no guarantee of excellent yields. Have all the equipment and processes been characterized? Does documentation exist for equipment operation and maintenance? Are the operators knowledgeable about the documentation?
Most supplier problems are encountered in the quality assurance area. Does the supplier know what yields are? Is process control used to monitor and control defects? Is the inspection done before reflow in a proactive approach or after the fact (post-reflow)?
Here are some questions for assessing whether the supplier can deliver consistent quality and whether the firm has good process control as well as documentation in place to meet commitments:
- Are areas sensitive to electrostatic discharge (ESD) clearly identified?
- Do all personnel and visitors wear approved ESD-protective clothing and wrist straps?
- Are all work surfaces, dissipative or conductive, grounded through a resistor?
- Are conductive or antistatic containers issued to transport sensitive materials?
- Are ESD-sensitive areas and containers periodically audited for conformity to documented ESD guidelines?
- Are documented workmanship standards maintained, if applicable?
- Is there a document control procedure?
- Is a minimum distribution list for new specifications maintained?
- How is defect logging accomplished?
- Are work instructions, production equipment and appropriate work environments in place for SMT processes?
- Are workmanship standards available?
- Is a corrective action system maintained, and does it provide preventive measures?
- Is there a feedback loop?
- Is statistical quality control (SQC) used?
Reasons for outsourcing include lower cost, supplier expertise or capital investment postponement. Set up a team armed with in-house selection procedure and a detailed questionnaire to select quality suppliers.
- Choose the supplier for the long haul.
- Choose as few suppliers as possible.
- Put long-term agreements in place.
- Share your vision with your partner.
- Treat supplier personnel as part of your design and manufacturing team.
- Seek vendor input at the schematic stage.
- Ensure design for manufacturability (DFM) compatibility.
- Get supplier buy-off before new designs.
- Build the relationship slowly but steadily.
Ray P. Prasad is an SMT Editorial Advisory Board member and author of the textbook Surface Mount Technology: Principles and Practice. Additionally, he is president of BeamWorks Inc. and founder of the Ray Prasad Consultancy Group. Contact him at P.O. Box 219179, Portland, OR 97225; (503) 297-5898; Fax: (503) 297-0330; E-mail: smtsolver@rayprasad.com; Web site: www.rayprasad.com.
More Columns from Various Archived Columns
Slash Sheet Chaos: Is What You See, What You Get?Moisture in Materials: Avoiding Process Gremlins
Material Witness: Beat the Heat--A Non-Math Intro to Thermal Properties
Material Witness: Considerations in Using TC Materials for PWBs
Material Witness: Are Your Materials Up to the Challenge?
Material Witness: Thermal Oxidation of Materials, Part I
Material Witness: Thermal Oxidation of Materials, Part II
Material Witness: R.I.P. Speedboard C