Estimated reading time: 13 minutes
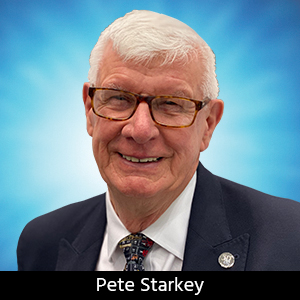
Contact Columnist Form
Printed Electronics: From R&D to Commercialisation
Dr. Steve Jones delivered a thought-provoking keynote presentation at the IeMRC Seminar on Plastic and Printed Electronics in Loughborough, UK on 19 March 2012. Highly acclaimed for the excellence of his many technical presentations, Dr. Jones had by request taken an alternative approach and presented his views from a philosophical, rather than scientific, perspective, reflecting upon the real meanings of invention, innovation and R&D, and the roles of government and industry in the commercialisation of printed interconnects. His presentation caught the attention of the audience and stimulated some energetic discussion.
After the seminar, I-Connect007 Technical Editor Pete Starkey took the opportunity to sit down with Steve Jones and invite him to expand on some of the observations he had made.
Starkey: Steve, that was different but quite enlightening and we heard some very interesting points of view. What do you personally understand as meaningful definitions of invention, innovation, and R&D?
Jones: We have a need to differentiate: R&D is not a single concept. “Invention” refers directly to the creation of an idea or method. This tends to be called “Research/Discovery” and to lie more with universities rather than industry. They try to understand the underlying laws of physics and chemistry. “
Innovation” differs from invention in that innovation refers to the use of a new idea or discovery. This tends to be called “Development” and lies more with industry than universities. Innovation leads to things that are accepted by markets and society. Innovation is the catalyst for growth: from craft shop to factory, from lab to fab. There is a flow from discovery through an engineered manufacturing process to benefits for society. Take as examples light bulbs; incandescent, fluorescent and LED/OLED: telephones; telegraph, landline, cellular and smartphone. There is more than a hundred years down each development chain, but the societal benefits of light and communication have been transformational.
Starkey: Does innovation only flow from newer entrepreneurial companies? Are large companies only capable of incremental improvements to established technologies?
Jones: Let’s look at some landmarks within our lifetime: The first transistor radio went on sale in USA in 1954, the silicon chip was invented in 1958, IBM introduced the PC in 1981, Apple launched the Macintosh in 1984, and the World Wide Web was first made available to the public in 1991. Innovation is the generation and commercialisation of novel ideas, products and processes. The larger technology-based companies recognise the imperative to innovate and tend to have specialised R&D units to promote technological innovation. The strength of these units has traditionally been their ability to innovate incrementally and refine existing products and processes rather than generate radical innovation. It is aimed at mainstream activity and tends to emphasise cost or feature improvements to existing products. Radical, or transformational, innovation produces substantial improvements and radically alters or even creates markets. Printed electronics sits here.
Starkey: So what are the issues for the larger company?
Jones: Radical technologies often look financially unattractive or risky and the markets are ill defined at best. The timeframes are much longer than with incremental innovation and shareholders and stakeholders tend to be risk averse. As successful companies become older they tend to develop shared expectations leading to cultural resistance to change, and this has also been true of universities. Company inertia can also be a factor: Organisational routines are important but hinder in an environment undergoing change. Look at Kodak and ICI for example. You don’t get sacked for saying “no” to risk; you get sacked for saying “yes” and not meeting expectations!
Starkey: What are your views on the roles of government?
Jones: Looking at the UK in the first instance, in the 1970s and 80s there was much debate over support for coal, steel, automotive, shipbuilding, etc., and much money was wasted maintaining traditional monolithic industries without a thought for what the world was doing. The advocates argued that manufacturing played a critical role in generating economic growth and employment opportunities – the critics claimed that government was incapable of making good choices about industry: that it could not pick winners and losers. They were both right but more fundamentally, the critics denied that there was anything special about manufacturing as distinct from other activities in the economy, or that any kind of manufacturing was more valuable than any other: “Potato chips or silicon chips-who cares? They are both chips.”
There is one great difference between yesterday’s concerns about manufacturing and today’s: Digitisation and modularity have made it possible to separate R&D and design from production.
Thirty years ago, Margaret Thatcher et al removed the crutches supporting “big industry” in the UK, revealing its weaknesses and causing its collapse. In the 1940s we had 6 million women in manufacturing alongside 8.5 million men; in the 1980s we had 6 million people in manufacturing, and now the figure is barely 2.5 million and manufacturing has dropped from 25% of GDP to 11% today. We have few big indigenous companies and rely on foreigners opening operations here, for example carmakers like Tata and Nissan.
Latterly, under the last Labour and present Conservative governments, manufacturing has found its way back onto the agenda. The Technology Strategy Board and Research Councils have been vehicles to encourage technology, sector and cluster development. The Technology Strategy Board picks sectors where UK businesses can thrive, and support innovative companies within them. They consider the size of the markets, the capability of the UK to address them, the timing, and the difference their support would make.
Starkey: So that’s government. What about industry?
Jones: Since we have few big companies, sector/cluster development is one way of supporting innovation. In the case of my own company, Printed Electronics Limited, without TSB support in the fields of Printed Electronics and Advanced Manufacturing we would not be here and neither would many of the networks nor the nascent supply chain. I’m a big fan of the TSB!
The Research Councils and the TSB attempt to create an environment in the UK in which innovation is possible and is open to smaller entrepreneurial companies.
Starkey: But can small companies survive in a global economy?
Jones: Well, let’s look at the wider global situation. In the 1980s, the attitude tended to be “Potato chips or silicon chips-who cares? They are both chips.” What has changed in 30 years? Digitisation and modularity have made it possible to separate R&D and design from production. Successful global technology brands have shown that manufacturing can be outsourced and offshored without damaging their ability to innovate. At one time it was possible to codify the different stages of the journey from conception to final product. However, the fragmentation of single company manufacturing led to a totally different landscape. There are few vertically integrated companies left: Apple, HP, Dell, TI and the like have little manufacturing under their roofs. It’s worth noting that much of the above is IT-intensive, and a line that manufactures Dell computers is just as at home manufacturing other computers, or mobile phones, or MP3 players.
If you look at the statistics, in 2000 Europe and Japan each produced twice the output of Southeast Asia and the US produced 10 times their output. In 2011, Southeast Asia produced the equivalent of the combined total of Europe, Japan and the US…China dominates and the growth rate has been phenomenal, although it’s now slowing. And in the supply chain, the big growth has been in EMS and ODM.
Starkey: So it’s effectively the EMS and ODM companies making the electronics rather than the OEMs?
Jones: Yes. Electronics manufacturing service providers manufacture, test, distribute, and provide return and repair services for electronic components and assemblies for original equipment manufacturers. Taiwan’s Foxconn is the biggest; its Chinese turnover is $90 billion and it is the biggest exporter in China. Its China-based subsidiary plans to raise its workforce in China to 1.3 million from the current 920,000 over the next 12 months. And 450,000 workers are employed at the Longhua Science & Technology Park, sometimes referred to as "Foxconn City" or "iPod City." The population of Cambridge is approximately 120,000; Sheffield is approximately 550,000; Birmingham approximately 1,020,000. Apple is Foxconn's biggest customer: Shipments of iPads grew to 14.5 million in Q4 2011 from 12.9 million in 2010. iPhone shipments exceeded 100 million in 2011, up from 53.5 million 2010 and 25.1 million in 2009. Approximately 2 billion mobile phones are likely to be made in 2012 and most of them will not be made by mobile phone companies.
Starkey: And how does an ODM differ from an EMS?
Jones: An original design manufacturer is a company which designs and manufactures a product which is specified and eventually branded by another company for sale. For example,
Quanta Computer Inc. is the largest manufacturer of notebook computers with 34% of the world market valued at $60 billion. Its customers include Apple, Compaq, Dell, Gateway, Hewlett-Packard, Alienware, Fujitsu, Toshiba, Sharp Corporation and Sony.
Starkey: So how will printed electronics compete or even live with the ODMs, EMSs and OEMs?
Jones: Many of the products already mentioned are IT-related and can be manufactured on the same or similar lines. The same is not true for some of the printed electronics products being highlighted: solar cells, OLEDs, sensors, logic, etc. Printed electronics transistors can be printed by spin coating, screen printing, nano-imprint, roll-to-roll, flexo, gravure and inkjet. With the rise of the ODM comes the importance of branding and marketing: You do not need to be a big company to be big in a market. With printed electronics it is possible to functionalise structures, for example, print a battery or interconnects during the manufacturing process. Printed electronic products are immature. Their Technology Readiness Level is 3 to 5 at present, meaning that they are typically at the demonstrator or proof of concept stage. There are lots of ugly babies out there: products or processes that need a lot of human intervention or whose materials are idiosyncratic or expensive will not survive. At this time we have to think niche, new products, moving into areas where electronics has not gone, for example, smart packaging, wearable electronics, or security and anti-counterfeiting. The UK is well placed in printed electronics from a technology stand-point. The TSB and academic institutions have been supportive; there are five centres of excellence for printed electronics and it is acknowledged that the UK and Germany are leaders in the field.
Starkey: What sort of people are required to make printed electronics a success?
Jones: In a new technology area we need people of vision, people who are brave who will drive the industrialisation process from lab to fab. We have got heroes, frontiersmen and engineers. Heroes are called heroes because they tend to be dead: they have crashed and burned in a spectacular way, often with collateral damage. Frontiersmen are called frontiersmen because they tend to be dead: face down in the sand with an arrow in the back - most of us would prefer to be heroes! Engineers will spend all your money and still not make a decision. However, engineers are critical: technology without engineering is a black hole that consumes money. You just need to keep a hand on your money and their throat! Resource is required to keep the wings on and buy a Kevlar shirt. Resource providers take risks but like to envisage a crock of gold, not just a crock. Unfortunately, it takes time to convince both users and investors. We need entrepreneurs and a banking system to support them
Starkey: Tell us about some of the obstacles you have encountered and overcome since you founded Printed Electronics Limited.
Jones: “Printed Electronics” was being hyped back in 2005 but a critical analysis of the underlying technology indicated fundamental gaps in the toolbox. The biggest problem we saw at the time was inkjet machine integration methodologies and technologies: this has not changed and remains the big problem for a fragmented supply chain of small companies. There is a litter of dead integrators who could not make a living out of their platforms. Some people can’t or don’t deliver and not necessarily because they don’t care or are stupid but we only know what we know, not what we don’t. So don’t oversell your capability…I spent several years justifying my existence due to over-hype of printed electronics! But it has changed this past 18 months.
Don’t look to the likes of the Hewlett Packards and Epsons to cascade technologies; it will be in products and processes that have their name on it. Collaboration and cooperation are important for small companies: generally we are pretty good at this in the UK and Printed Electronics Limited has many friends in industry and academia with whom we work. We want to make generic electronics, i.e., anything. We did not want to make batteries or capacitors or develop inks; we want a supply chain similar to RS Components or Farnell where we could buy best in class for a particular customer specification. We would integrate the components because we understand electronic applications ie we look to an EMS/ODM model.
The DTI had the Direct Write call in 2005 and it allowed us to form the company. The pound-for-pound allowed us to put together the facility in Cambridge and we spent four years working with our TSB project partners to understand the core issues, build equipment, and find and develop process solutions. We picked up other TSB projects but the most important thing to come out of these projects was the networking with like-minded people, in companies big and small. Our core activity and business plan is the EMS and ODM route, i.e., work with our partners to develop their products both upstream and downstream
One needs to be heroic and passionate, and explore boundaries but preferably avoid death. Looking through the hype, there were non-trivial issues: with inks and nanoparticles that form the interconnects and components; ink interactions with substrates to form multilayer structures; and the functionalisation of electronic attributes. These issues are still with us six years on, but the potential for printed electronics was and remains huge and not just to replace conventional electronics but to transform where electronics can go.
Starkey: So what’s in the toolbox of Printed Electronics Limited?
Jones: Electronics is a generic term and we need to be able to put printed electronics anywhere and on anything. Generic electronics requires components and interconnections that make up the toolbox. That printed electronics toolbox is pretty bare compared with mainstream electronics, but we can customise products that cannot easily be done using mainstream high-volume processes. We chose inkjet printing as our preferred printing method because it is tool-less, non-contact and lends itself to proof of concept demonstrators. However, more recently we are using screen printing, graphics printing and lasers to form professional looking products, i.e., moving up the TRL ladder
The government’s TSB and Research Councils have put seed money – “patience money” – into printed electronics and a nascent supply chain can be identified. Printed electronics is maturing and moving up the TRL ladder. We are on the cusp of manufacturing printed electronics products. We are slightly pregnant and there is no such thing as being slightly pregnant! Since we do not have a clear manufacturing route and cannot buy off-the-shelf equipment, how are we going to move from demonstrators to production? In the UK, we have access to PETEC, the national centre for process innovation in printed electronics, whose mission is to offer facilities and expertise that help to reduce the level of R&D risk and capital investment while speeding up time to market.
The cost of a printed electronics fab is tens of millions of pounds, much cheaper than conventional fabs but still a lot of money when we have few big companies in the UK that play in the electronics market…we heed a hero! In the short term, the EMS/ODM model works for small companies like Printed Electronics Limited.
Starkey: Steve, we wish you every success. Many thanks for sharing your thoughts, opinions and experiences with us.
More Columns from The European Angle
CircuitData: A New Open Standard for PCB Fab Data ExchangeI Never Realised It Was So Complicated!
The European Angle: Institute of Circuit Technology 43rd Annual Symposium
Ventec International Group's Martin Cotton Celebrates 50 Years in PCB Design
Reporting on the Institute of Circuit Technology Spring Seminar
EuroTech: Raw Materials Supply Chain—Critical Challenges Facing the PCB Industry
EuroTech: ENIPIG—Next Generation of PCB Surface Finish
EuroTech: Institute of Circuit Technology Northern Seminar 2016, Harrogate