-
- News
- Books
Featured Books
- design007 Magazine
Latest Issues
Current IssueProper Floor Planning
Floor planning decisions can make or break performance, manufacturability, and timelines. This month’s contributors weigh in with their best practices for proper floor planning and specific strategies to get it right.
Showing Some Constraint
A strong design constraint strategy carefully balances a wide range of electrical and manufacturing trade-offs. This month, we explore the key requirements, common challenges, and best practices behind building an effective constraint strategy.
All About That Route
Most designers favor manual routing, but today's interactive autorouters may be changing designers' minds by allowing users more direct control. In this issue, our expert contributors discuss a variety of manual and autorouting strategies.
- Articles
- Columns
- Links
- Media kit
||| MENU - design007 Magazine
Estimated reading time: 3 minutes
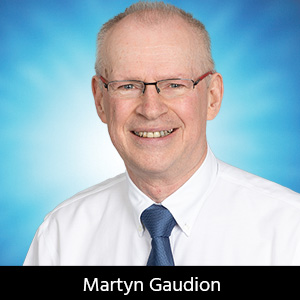
Crosshatching Compromise
Sometimes engineering results in some uncomfortable compromises; this is often the case with PCBs as the mathematical methods used by the modelling tools are based on "ideal" physical properties of materials rather than the actual physical materials in use. In previous articles I have referred to this when considering the effects of glass woven reinforcement in base materials – the differing properties of the glass and the resin contribute to variations in electrical characteristics – given the scale of traces now in common use. The topic is well known and much written about. However, this month’s "Pulse" is on the subject of crosshatched ground planes (sometimes referred to as mesh ground planes) in transmission line structures.
This is another area where a necessary compromise between what the academics would treat as "ideal" and what has to be fabricated to make a practical board - I am referring to crosshatch (mesh) ground planes most often found on flex and flexrigid PCBs. "Not ideal," say the academics, “adding a crosshatch will lengthen the return path and cause all sorts of problems at higher frequencies.”
However, first and foremost, flex circuits by definition should be mechanically flexible! If you try to construct a stripline with solid ground planes above and below the line (see Figure 1) the cross section looks similar to an I-beam which is a mechanically very stiff structure, so whilst the signal integrity would arguably be enhanced, the board would fail mechanically in a very short time.
To meet this challenge, it is possible – and commonplace – to use crosshatching to achieve a transmission line structure on a flex circuit and trade some signal integrity for durability. Fabricators, though, should consult with the EE responsible for the design to ensure that the hatch pattern is not too large to have significant impact at the upper frequencies.
Just as for glass woven structures, the adoption of crosshatching means that the final structure is likely to have a broader tolerance from the modeled structure than a straightforward design using solid planes. However, it is always worth keeping the saying of George E.P. Box (Professor Emeritus of Statistics University of Wisconsin) in mind, "Essentially, all models are wrong, but some are useful." In the case of crosshatching, modeling should reduce the number of prototypes you need to turn to achieve the desired transmission line characteristics.
One other reason for using crosshatching on flex is that often the structures are very thin and in order to achieve the desired impedance this can result in very narrow traces. Again, this means that impedance tolerance will broaden; the use of hatching will allow the fabricator to deploy wider traces and hence more predictable and tighter impedance tolerance.
As I write this, I am wondering whether - and maybe some engineers do - coplanar structures could be used in place of crosshatch - the transmission line could then
be constructed on a single layer, therefore overcoming the "I beam" mechanical constraints of striplines and to a lesser extent microstrips. If any Si gurus are reading this, I would be delighted to hear your response.
I have on occasion also seen crosshatching used in rigid designs, again to enable a designer to fabricate realistic line widths, though a more common practice is for the designer to reference the transmission line, not to the adjacent ground, but to open an aperture in the adjacent ground and reference to a lower layer, subject to ensuring that no other high speed lines traverse the aperture causing resultant horrible transmission line discontinuities.
In summary, there is no right or wrong when deciding which route to take; the necessary adjustments need to be made to ensure the design is fit for purpose and that, like all engineering tasks, means loosening tolerances in some areas to allow you to tighten them in more critical ones. The task does become increasingly statistical when you are working to ensure that the design will remain in specification through the normal range of production variation.
More Columns from The Pulse
The Pulse: Design Constraints for the Next GenerationThe Pulse: Ultra Upgrade Unknowns—What’s Coming for UHDI?
The Pulse: Commonsense Cost Cutting
The Pulse: Overconstraining: Short, Slim, and Smooth
The Pulse: Drilling Down on Documentation
The Pulse: New Designer’s (Partial) Guide to Fabrication
The Pulse: Simplest Stackups Specified
The Pulse: Rough Roughness Reasoning