-
- News
- Books
Featured Books
- design007 Magazine
Latest Issues
Current IssueProper Floor Planning
Floor planning decisions can make or break performance, manufacturability, and timelines. This month’s contributors weigh in with their best practices for proper floor planning and specific strategies to get it right.
Showing Some Constraint
A strong design constraint strategy carefully balances a wide range of electrical and manufacturing trade-offs. This month, we explore the key requirements, common challenges, and best practices behind building an effective constraint strategy.
All About That Route
Most designers favor manual routing, but today's interactive autorouters may be changing designers' minds by allowing users more direct control. In this issue, our expert contributors discuss a variety of manual and autorouting strategies.
- Articles
- Columns
- Links
- Media kit
||| MENU - design007 Magazine
Estimated reading time: 4 minutes
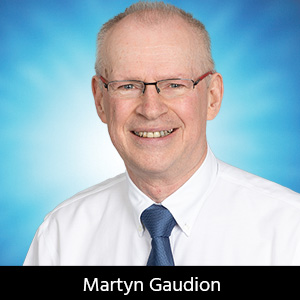
Signal Integrity – the ‘S’ Words
Three words, or rather, phrases are in the process of entering the vernacular of the PCB industry, albeit one phrase is already familiar, but taking on a different meaning. All start with S and all relate in one way or another to signal integrity.
IPC D24 met recently to discuss measurement standards for transmission line losses; in the background of the debate an underlying question echoed around the meeting space, “Yes this is how we measure, but what can the fabricator do to ensure their boards pass, whichever loss measurement test is adopted?” The first step here is to start to understand the language of signal integrity and some of the new effects that interplay in the juggling act of fabricating high quality, yet cost effective PCBs.
So let’s take a look at the three “S” phrases, namely, S-parameters, surface roughness and skin effect. The first, S-parameters, allow an engineer to record the transmission line performance over a range of frequencies. The second, surface roughness, is a key driver in signal integrity because of its impact on signal losses; the effect of surface roughness is magnified by the third term, skin depth, because of the tendency of electrical currents to flow at ever shallower depths in a conductor as frequency increases.
S-parameters describe the behaviour of passive networks at a fixed frequency; fully named scattering parameters, in layman’s terms you can perhaps more think of “scattering” from an optical perspective – what happens when a ray of light passes from one medium to another. In RF terms the scattering parameters describe what happens when an e-m wave travels from a transmission line of one impedance to an unknown (passive) line. “At a fixed frequency?” I hear you ask, “but surely digital transmission lines are inherently broadband?” Correct! and in the case of high speed serial transmission with very long data words the bandwidth of a serial link can be very broad indeed. So you will find that lines are characterised over a broad range of frequencies. This requires measuring or modelling at hundreds or thousands of finite frequency steps. For ease of use the S-parameters are often saved in a common file format called a Touchstone™ file; occasionally the Touchstone file is called an “.snp” file after its file extension, the n referring to the number of ports: .s1p, one port, i.e. a termination, .s2p, a single ended transmission line, .s3p, a microwave mixer and .s4p, a four port line, i.e. a differential pair. The only commonly experienced forms from a high speed digital perspective are the .s2p and the .s4p. The S-parameters describe how much signal is reflected, transmitted from each end of the line and the phase shift of the respective signals. To learn a little more, this application note will get you off to a good start.
The second “S” is for surface roughness, something you may think is more the domain of Paul Reid’s “Reid on Reliability” column, as the PCB industry has long needed to consider the level of roughness required to promote adhesion in the lamination process and hence ensure good reliability. However, as frequency goes up, and the more signal travels on the outside of the conductor (more detail in the skin depth explanation later) the more surface roughness impacts on signal losses.
Fortunately the foil and laminate suppliers have been hard at work in this area and are now delivering ranges of materials which offer surprisingly smooth profiles whilst still delivering the adhesion performance required for excellent reliability.
Still reading? So far you have seen how S-parameters describe the transmission line performance over the range of frequencies of interest to the designer and how surface roughness impacts the losses in the transmission line. To wrap up this October column, let's take a look at why the current chooses to run closer to the surface of the conductor as the frequency increases, this phenomenon is called the skin effect.
This diagram graphs the amplitude of conduction current against depth (z) into a conductor. There is a conduction current of density Jx, (where J0 is the current density at the surface). The distance δ is the value of z at which |Jx| = J0/e. This is also the same value at which the rectangular area δJ0 in the diagram equals the area under the exponential curve. δ is known as the Skin Depth. For a little more depth on the subject (no pun intended) have a look at this application note.
Skin effect is not unique to ultra high speeds; skin effect is present on all AC transmission systems. However, at lower frequencies the skin depth (the average depth at which the current flows) is much greater than the thickness of the copper foil. At 60Hz power line frequency, though, the skin depth is about 8mm, so power line distribution engineers still need to keep it in mind. Back in the digital world, skin depth on copper is only 2 microns at 1GHz, so not much copper cross section to carry the current there! Microwave engineers used to compensate for this by using wide traces but from a high speed digital perspective, chip geometries and desired routing densities mean that skin depth is always going to play in signal losses, hence the move to smoother copper with alternate adhesive promotion treatments.
So there you have it, three word pairs that have crept up on the fabrication and design industry and will no doubt continue to be of interest as the high speed signalling method of choice moves increasingly to high speed differential pairs on lossy transmission lines.
More Columns from The Pulse
The Pulse: Design Constraints for the Next GenerationThe Pulse: Ultra Upgrade Unknowns—What’s Coming for UHDI?
The Pulse: Commonsense Cost Cutting
The Pulse: Overconstraining: Short, Slim, and Smooth
The Pulse: Drilling Down on Documentation
The Pulse: New Designer’s (Partial) Guide to Fabrication
The Pulse: Simplest Stackups Specified
The Pulse: Rough Roughness Reasoning