-
- News
- Books
Featured Books
- design007 Magazine
Latest Issues
Current IssueProper Floor Planning
Floor planning decisions can make or break performance, manufacturability, and timelines. This month’s contributors weigh in with their best practices for proper floor planning and specific strategies to get it right.
Showing Some Constraint
A strong design constraint strategy carefully balances a wide range of electrical and manufacturing trade-offs. This month, we explore the key requirements, common challenges, and best practices behind building an effective constraint strategy.
All About That Route
Most designers favor manual routing, but today's interactive autorouters may be changing designers' minds by allowing users more direct control. In this issue, our expert contributors discuss a variety of manual and autorouting strategies.
- Articles
- Columns
- Links
- Media kit
||| MENU - design007 Magazine
Estimated reading time: 2 minutes
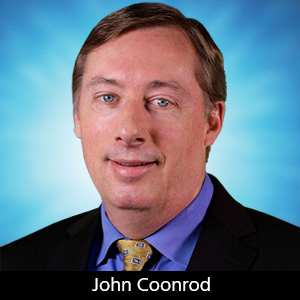
Lightning Speed Laminates: Not all PTFE Laminates are the Same
Polytetrafluoroethylene (PTFE) laminates are the original high-frequency laminate, and they have been around for many decades. I have heard people talk about PTFE laminates as if they are all the same and have the same capabilities and limits, but that is very misleading. I’ll give a few examples of the many things to consider when choosing a PTFE laminate.
A couple of issues to consider are circuit fabrication and high-frequency performance issues. If a circuit is made with pure PTFE, it could have exceptional high-frequency performance. However, making a circuit out of a pure PTFE laminate is not a trivial matter, for a variety of reasons. It is very soft, which means dimensional stability is highly questionable and drilling can be difficult. If smear occurs during the drilling process for a PTFE laminate, the only option is to throw away the circuit because nothing can desmear PTFE. It has extremely high coefficient of thermal expansion (CTE) so PTH via reliability and soldering can be a concern. Nothing likes to adhere to PTFE, which means having electroless copper adhere to a drilled hole-wall can be challenging. The thermal coefficient of Dk (TCDk) is very high, which means the Dk will change significantly with a change in temperature. Also, the thermal conductivity is very low, which for some high-power applications can be detrimental to thermal management. And there are more considerations. However, if you mix the right stuff with PTFE, you can overcome most of these obstacles.
The first attempt to make PTFE friendlier to the PCB fabrication process was to have it reinforced with layers of woven-glass fabric, fiberglass. The woven-glass reinforcement certainly helps the mechanical aspect of dimensional stability, and it significantly improves the CTE. Additionally, the glass may give a minor improvement to the drilling process and electroless copper adhering to the through hole-wall for preparation to copper plating. The glass reinforcement may improve the TCDk and thermal conductivity properties of the laminate.
Over time, there have been other improvements to PTFE laminates. For instance, adding ceramic filler was a really good idea. However, it can’t be just any ceramic filler; if the right ceramic is not selected, some properties will benefit, and other properties will degrade. When the right ceramic filler is used, the CTE is improved dramatically, TCDk improves greatly, and thermal conductivity increases. The improvement to CTE allows these types of laminates to be used in multilayer applications where PTH reliability is important. The presence of the ceramic filler can also improve the copper plating preparation steps.
When the right ceramic filler and woven-glass are combined in a PTFE-based laminate, the circuit fabrication and RF performance issues can be overcome. The woven glass helps to rigidize the laminate and make it more dimensionally stable. The proper combination of ceramic filler and woven glass can improve the CTE, TCDk, and thermal conductivity, and allow simpler drilling and PTH preparation processing.
To read this entire column, which appeared in the April 2018 issue of Design007 Magazine, click here.
More Columns from Lightning Speed Laminates
Lightning Speed Laminates: Millimeter-wave Properties and PCB Design ChallengesLightning Speed Laminates: Optimizing Thermal Management for Wireless Communication Systems
Lightning Speed Laminates: Test Vehicles for PCB Electrical Material Characterization
Lightning Speed Laminates: Optimum Thermal Stability Considerations
Lightning Speed Laminates: Thermal Management Isn’t Getting Easier
Lightning Speed Laminates: Benefits of High-Performance Hybrid Multilayer PCBs
Lightning Speed Laminates: An Overview of Copper Foils
Lightning Speed Laminates: The Importance of Circuit Features for Millimeter-Wave Applications