-
- News
- Books
Featured Books
- smt007 Magazine
Latest Issues
Current IssueWhat's Your Sweet Spot?
Are you in a niche that’s growing or shrinking? Is it time to reassess and refocus? We spotlight companies thriving by redefining or reinforcing their niche. What are their insights?
Moving Forward With Confidence
In this issue, we focus on sales and quoting, workforce training, new IPC leadership in the U.S. and Canada, the effects of tariffs, CFX standards, and much more—all designed to provide perspective as you move through the cloud bank of today's shifting economic market.
Intelligent Test and Inspection
Are you ready to explore the cutting-edge advancements shaping the electronics manufacturing industry? The May 2025 issue of SMT007 Magazine is packed with insights, innovations, and expert perspectives that you won’t want to miss.
- Articles
- Columns
- Links
- Media kit
||| MENU - smt007 Magazine
Estimated reading time: 4 minutes
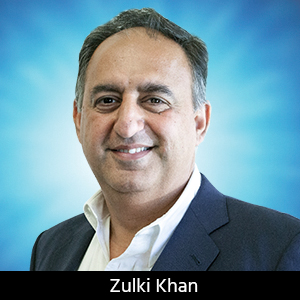
Zulki’s PCB Nuggets: Consider the Integrity of Wire Bonding
As we said in an earlier column, wire bonding plays a central role in PCB hybrid manufacturing, meaning the merger of traditional SMT manufacturing and microelectronics. Reliability and integrity are inextricably intertwined when it comes to wire bonding—especially for small PCBs, including rigid, flex, and the combination of rigid-flex.
While reliability and integrity can be regarded as synonymous as far as PCB manufacturing with microelectronics assemblies is concerned, the integrity of wire bonding takes on other reliability-associated process qualities. Wire bonding is the methodology of interconnecting the wire to the bond pad. In short, wire-bond integrity is about the quality of wire-bond interconnect that determines how good or how bad it is by verifying the dependability and reliability of it.
Three Main Factors
To create the integrity of wire bonding, three main factors need to be implemented on that PCB hybrid manufacturing floor.
First, when the pads are designed for wire bonding in the layout phase, assurances need to be made that wire length is properly calculated and verified. This is a very important step because when the wire loops are performed, technicians have to ensure wire loops are not overly extended. If they are, it creates the probability of wire breaking when bonding is performed or afterward in the field due to a latent flaw in wire bonding.
Also, stacked wire-bond loops need close attention. This becomes extraordinarily tricky and integrity becomes very challenging because now you are dealing with two to three sets—and in some cases, four sets—of wire-bond loops, each of different lengths. These sets of loops cross-cross over each other, going on top of one set of wire bonds on top the second, and then going on top of a third (Figure 1).
Figure 1: Sets of wire loops crisscross over each other.
This loop set crisscrossing creates a series of wire bonds on top of each other. What results is an angle on which the bond is stitched on the pad. That angle has to be carefully and accurately calculated and verified by process engineering. There shouldn’t be too much of a crisscross. Pad length from the first set of wire bonds to the second and third needs to be very accurately and correctly calculated and verified to create a highly acceptable staggered wire bonding product. Unless those factors are kept at the forefront, wire-bond integrity is severely jeopardized.
Second, the proper PCB or substrate surface finish must be selected at the manufacturing level. When it comes to surface finish, you have to make sure the amount of nickel, copper, and gold is properly specified in the fabrication drawing, depending on the application of the end product.
Based on our experience and success, the surface finish choices that worked best for our projects are immersion gold over nickel or ENIG, ENEPIG, and in some cases, immersion silver. These different surface finishes have different strengths, behaviors, and properties according to their chemical composition under which they operate and behave. This means it’s critical to ensure either ENIG or ENEPIG is used for wire bonding.
As far as the surface finish of the PCB is concerned, ENEPIG is suitable for gold wire bonding, aluminum wire bonding, and contact resistance. Sequential deposition of electroless nickel (120–240 microinches) is followed by 2–10 microinches of electroless palladium with an immersion gold flash of 2–6 microinches on the top. For ENIG, the deposition consists of 2–8 microinches of electroless gold plated over 120–240 microinches of nickel.
Third, how do you make sure the wire bonding to be created maintains high levels of integrity? In some cases, the amount of gold is not enough. Other times, the surface is oxidized, especially if the PCB has an immersion silver surface finish. Also, the board has been sitting in a non-humidified environmental control chamber or ambient room temperature for a while, and the surface finish has been contaminated or oxidized. In cases like these, the PCB has to be cleaned with either argon gas, IP solution, or another solvent. The surface finish has to be clean to create a wire bond strong enough to pass strength and pull tests.
A physical pull test measurement is the final judge as to the integrity of the wire bond. Here are the specific numbers a pull test provides to measure the integrity of wire bonding and pass it with flying colors. For example, if you use 1.0-mil gold wire, you need to have wire bond withhold a 3.0 pre-seal and 2.5 post-seal grams force of strength. In the case of 1.0-mil aluminum wire, you must have 2.5 pre-seal and 1.5 post-seal grams force strength. These are for test class C or D per MIL-STD-883 Rev. G.
Conclusion
So far, I’ve covered the aspects and measurements going into ensuring wire-bond integrity. However, there is yet another factor involved—the human factor. Engineers and technicians doing the programming for those wire bonding stitches and loops must be sufficiently experienced to perform effective and optimal programming of the wire bonder.
Zulki Khan is the president and founder of NexLogic Technologies Inc.
More Columns from Zulki's PCB Nuggets
Zulki's PCB Nuggets: Cleanliness is Next to ReliabilityZulki’s PCB Nuggets: Thermal Compression Bonding for Extra Fine Pitch Flip Chips
Zulki’s PCB Nuggets: WBAN Steps Into PCB Microelectronics Assembly
Zulki’s PCB Nuggets: Photonics Comes to PCB Microelectronics Assembly
Zulki’s PCB Nuggets: Sub-Micron Die Bonding—Don’t Be Misled by Five Micron Placement Standard
Zulki’s PCB Nuggets: Meet the New Player in PCB Microelectronics Assembly—Interposers
Zulki’s PCB Nuggets: How Effective Is Your PCB Microelectronics Assembly?
Zulki’s PCB Nuggets: Five Key Benefits for Onshoring PCB Microelectronics Assembly