-
- News
- Books
Featured Books
- smt007 Magazine
Latest Issues
Current IssueWhat's Your Sweet Spot?
Are you in a niche that’s growing or shrinking? Is it time to reassess and refocus? We spotlight companies thriving by redefining or reinforcing their niche. What are their insights?
Moving Forward With Confidence
In this issue, we focus on sales and quoting, workforce training, new IPC leadership in the U.S. and Canada, the effects of tariffs, CFX standards, and much more—all designed to provide perspective as you move through the cloud bank of today's shifting economic market.
Intelligent Test and Inspection
Are you ready to explore the cutting-edge advancements shaping the electronics manufacturing industry? The May 2025 issue of SMT007 Magazine is packed with insights, innovations, and expert perspectives that you won’t want to miss.
- Articles
- Columns
- Links
- Media kit
||| MENU - smt007 Magazine
Estimated reading time: 2 minutes
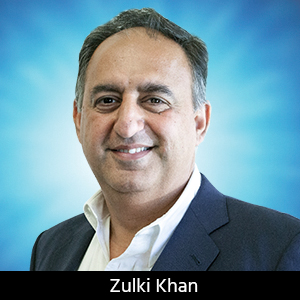
Zulki’s PCB Nuggets: Three Die Attach Methods for Microelectronics Manufacturing
Die attach technology is increasingly being applied in PCB hybrid manufacturing (i.e., combining traditional SMT manufacturing with microelectronics) to comply with the requirements of small PCBs, especially rigid, flex, and combination rigid-flex circuit boards. These smaller boards are used in a variety of IoT, wearable, and portable applications.
A growing number of these smaller boards cannot be completely designed to undergo traditional SMT manufacturing. As a result, they must go through highly specialized microelectronics manufacturing that entails wire bonding and die attach, flip chip, and similar technologies.
In an earlier column, I detailed PCB wire bonding. Here, I’ll explain die attach (Figure 1). As the name implies, it’s the process of attaching a chip or die to a package, substrate, rigid or flex circuit, another package, or a die attached to another die.
Figure 1: Die attach.
The key point to get across here is that die attachments aren’t the same. There are three different die attach methods—epoxy, eutectic, and solder attach—and each possesses important differences.
The epoxy method could be silver epoxy glass or a polyimide-based material. A fine and extremely precise dispenser very accurately dispenses the epoxy. In this case, the substrate is heated to a higher level of temperature, ranging from room temperature up to 200°C, depending on the type of epoxy used. This temperature allows the epoxy to be properly cured so that it adheres to the substrate to precisely create the joint between the substrate and the die.
Eutectic die attach uses a metal layer made of aluminum or gold. Gold has a very high operating temperature ranging from 230°C to 400°C. A eutectic system is a mixture of chemical compounds or elements that form a single composition, which solidifies at a lower temperature compared to these individual elements. These individual elements have considerably higher individual melting points compared to compounds. The fact that eutectic temperature is more manageable and lower compared to the individual pure elements is at the heart of eutectic bonding.
The third die attach method is solder attach, which is similar to SMT manufacturing or SMT joint creation. Solder attach is a common type of die bonding because of better thermal conductivity of the solder material itself. Depending on the different methodologies listed, there could be an extreme variation of temperatures on the die during the die attach process and operation.
Solder attach is an important concept to dissipate the heat, which is generated from the power device—the bond that efficiently creates the joint. When the solder is attached, it is referred to as soft solder attach. Depending on the alloy used, the melting temperature is lower compared to other methodologies. Alloy used in solder attach can either be tin-lead, which melts at 150°C, or indium, which melts at 220°C.
After die attach is complete, wire bonding is performed to create the joint that connects the die to the substrate. These connections are performed by attaching different wires—gold, aluminum, copper, or in some cases, silver—to the die pads to the solder pads on the board or substrate.
Zulki Khan is the president and founder of NexLogic Technologies Inc.
More Columns from Zulki's PCB Nuggets
Zulki's PCB Nuggets: Cleanliness is Next to ReliabilityZulki’s PCB Nuggets: Thermal Compression Bonding for Extra Fine Pitch Flip Chips
Zulki’s PCB Nuggets: WBAN Steps Into PCB Microelectronics Assembly
Zulki’s PCB Nuggets: Photonics Comes to PCB Microelectronics Assembly
Zulki’s PCB Nuggets: Sub-Micron Die Bonding—Don’t Be Misled by Five Micron Placement Standard
Zulki’s PCB Nuggets: Meet the New Player in PCB Microelectronics Assembly—Interposers
Zulki’s PCB Nuggets: How Effective Is Your PCB Microelectronics Assembly?
Zulki’s PCB Nuggets: Five Key Benefits for Onshoring PCB Microelectronics Assembly