-
- News
- Books
Featured Books
- smt007 Magazine
Latest Issues
Current IssueWhat's Your Sweet Spot?
Are you in a niche that’s growing or shrinking? Is it time to reassess and refocus? We spotlight companies thriving by redefining or reinforcing their niche. What are their insights?
Moving Forward With Confidence
In this issue, we focus on sales and quoting, workforce training, new IPC leadership in the U.S. and Canada, the effects of tariffs, CFX standards, and much more—all designed to provide perspective as you move through the cloud bank of today's shifting economic market.
Intelligent Test and Inspection
Are you ready to explore the cutting-edge advancements shaping the electronics manufacturing industry? The May 2025 issue of SMT007 Magazine is packed with insights, innovations, and expert perspectives that you won’t want to miss.
- Articles
- Columns
- Links
- Media kit
||| MENU - smt007 Magazine
Estimated reading time: 5 minutes
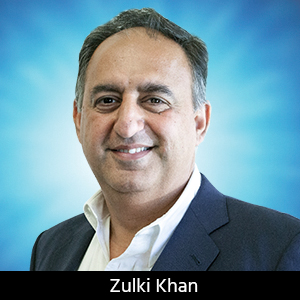
Zulki’s PCB Nuggets: 7 Steps to Successful Assembly for Medical Devices Using Microelectronics
Seven major steps need to be taken to achieve successful SMT and microelectronics assembly for medical electronic devices. These key steps take on special significance for newly emerging implantable and ingestible medical devices and result in medical devices that are robust, smaller, highly reliable, more powerful, and lighter.
- Deploy the right ancillary devices, such as tooling, fixtures, and jigs.
- Decide which process to perform first: SMT or microelectronics.
- Protect sensitive microelectronics areas.
- Properly use epoxies.
- Consider conductive vs. non-conductive epoxy applications.
- Address thermal profiling and heat dissipation.
- Maintain records, inspection tools, and reliability analyses.
Step 1
Since these medical devices go inside the human body, it’s critical to put specialized kinds of tooling, fixtures, and jigs in the microelectronics assembly process so that there no foreign objects or contaminations creep into the product assembly. Examples include stainless steel or anodized fixtures and the use of latex-free gloves during product manufacturing and manual handling.
Tooling has to be precise with very tight tolerances. Jigs need to be made with specialized materials, allowing very tight wiggle room for the flex board so that the medical device stays in place. Further, specialized jigs are vital to ensure the flex board stays completely flat during dispensing of epoxies and pastes, as well as during the pick-and-place process.
Glob topping on microelectronics devices requires different and specialized tools, jigs, and fixtures, as well. Emphasis must also be placed on possible solder splashes and/or flux residues for complete elimination, as well as on extra cleanliness during microelectronics assembly.
Step 2
The next step is deciding whether to perform SMT assembly or microelectronics assembly first. There are different preferences among EMS providers. Some prefer SMT assembly first, while others prefer microelectronics assembly. However, the most prevalent is performing SMT assembly first, while keeping microelectronics assembly areas with utmost cleanliness. It’s critical to protect those areas from residue fluids, solder, fluxes, or paste.
Kapton tape or solvable glues are used to maintain the integrity of those areas by completely covering these sensitive areas. After SMT assembly is completed, those adhesives are taken off. Further, to ensure a clean surface, specialized cleaning called plasma cleaning is sometimes performed.
Step 3
Step three starts where step two leaves off—the importance of protecting sensitive microelectronics areas. Here, assurances are needed for a bio-compatible glob top materials and fluids that can efficiently interact with the human body without adverse effects.
Once SMT and microelectronics assemblies are complete, specialized cleaning, effective glob topping, final rinse, and cleaning are performed. It’s important to note that these and other PCB hybrid manufacturing processes demand extensive experience. Thus, EMS providers with this high level of knowhow are the ones that know how to overcome cleanliness and multi-glob top application and protection challenges.
Steps 4–6: The Trio of Linked Steps
The next three steps are closely linked together, including the proper use of epoxies, applications requiring thermally conductive versus thermally non-conductive epoxies, and thermal profiling and heat dissipation.
The two types of epoxies are thermally conductive and non-conductive. Selecting which one to use in an application involves several factors. Those are curing at room or selected temperatures (either low or high viscosity rating), pot life (or how much life the epoxy has after being mixed), thermal conductivity, and glass transition temperature (Tg).
Epoxies are comprised of one or more compounds or elements, which have to be considered when undergoing curing. An example is the generic epoxy EPO TEK 930 -4. It’s composed of two compounds and is cured at 150° C for 10 minutes, or it could be cured for 80° C for six hours. Operating temperature is an associated factor here. A maximum temperature could be 200°C or 150°C, which also depends on epoxy compounds and their curing conditions.
Pot life ranges from two to six hours or as long as 20–30 days and refers to a certain period of time before an epoxy becomes bad. Generally, epoxy manufacturers cure their own products, and savvy OEM customers provide the PCB house the exact epoxy to be used for their applications.
Thermally conductive epoxy is used when the base of the die has either a ground or solid plane. When current is flowing from point A to point B, the die’s bottom surface is used to migrate the temperature from those two points. However, if the die’s bottom side has no substrate or ground, then thermally non-conductive epoxy is used since no current flows through the epoxy from top of the die to the bottom.
Tg is a gradual and reversible transition in materials from a hard and brittle state into a viscous or rubbery state. Tg is an important aspect during assembly because substrates and epoxies, which are assembled, need to have compatible Tg.
Thermal conductivity, as it pertains to epoxies, is a measure of how quickly the heat dissipates. Values can range from 0.3 or 0.4 watts (W) per Milli-Kelvin (mK) at the lower scale, meaning heat dissipates very slowly, to 1.7 to 2 W/mK at the high side, meaning it quickly dissipates.
When it comes to thermal profiling, Tg has to be considered. Analysis needs to be performed among the substrate, epoxy, and die, using the different datasheets for all of them; then, you decide on the ones most conducive among themselves.
Step 7
Lastly, you must consider records maintenance, inspection tools, and reliability analyses. As part of a new product introduction (NPI) phase, medical device OEMs need to ensure all manufacturing records are kept safe for five to seven years. Those include parts and batch codes, as well as certificates of compliance and approval for all parts and components on PCBs. It’s critical for the OEM to clearly identify manufacturers when and if a medical product is recalled.
Inspection tools include high-powered microscopes. These are highly sophisticated tools that determine wire loop heights and can visually check die-attach coverage. They can also look at pad dimensions on a substrate or PCB to assure consistencies and that bond groups are within allowable guidelines. The importance of inspection tools cannot be underestimated since implantable and ingestible medical products are going inside the human body that has tight tolerances in terms of height restrictions, along with other considerations.
Reliability takes into account both the prototyping and production of medical electronics devices. In the case of prototyping, assurances must be made every single board has 100% reliability. As for production, sampling is performed based on 20%, 40%, and then 50% of the production, depending on its application.
In summary, neglecting any of these key steps can result in a less than optimal implantable or ingestible medical device.
Zulki Khan is the president and founder of NexLogic Technologies Inc.
More Columns from Zulki's PCB Nuggets
Zulki's PCB Nuggets: Cleanliness is Next to ReliabilityZulki’s PCB Nuggets: Thermal Compression Bonding for Extra Fine Pitch Flip Chips
Zulki’s PCB Nuggets: WBAN Steps Into PCB Microelectronics Assembly
Zulki’s PCB Nuggets: Photonics Comes to PCB Microelectronics Assembly
Zulki’s PCB Nuggets: Sub-Micron Die Bonding—Don’t Be Misled by Five Micron Placement Standard
Zulki’s PCB Nuggets: Meet the New Player in PCB Microelectronics Assembly—Interposers
Zulki’s PCB Nuggets: How Effective Is Your PCB Microelectronics Assembly?
Zulki’s PCB Nuggets: Five Key Benefits for Onshoring PCB Microelectronics Assembly