-
- News
- Books
Featured Books
- smt007 Magazine
Latest Issues
Current IssueWhat's Your Sweet Spot?
Are you in a niche that’s growing or shrinking? Is it time to reassess and refocus? We spotlight companies thriving by redefining or reinforcing their niche. What are their insights?
Moving Forward With Confidence
In this issue, we focus on sales and quoting, workforce training, new IPC leadership in the U.S. and Canada, the effects of tariffs, CFX standards, and much more—all designed to provide perspective as you move through the cloud bank of today's shifting economic market.
Intelligent Test and Inspection
Are you ready to explore the cutting-edge advancements shaping the electronics manufacturing industry? The May 2025 issue of SMT007 Magazine is packed with insights, innovations, and expert perspectives that you won’t want to miss.
- Articles
- Columns
- Links
- Media kit
||| MENU - smt007 Magazine
Estimated reading time: 4 minutes
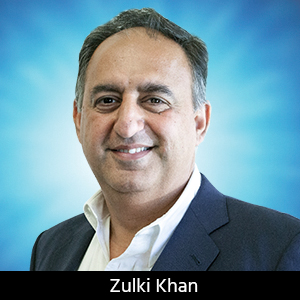
Zulki’s PCB Nuggets: Urgent Call for Ventilators—PCB Technology at the Ready
An urgent call is out to medical equipment makers that thousands—even millions—of ventilators are in the greatest demand in our history due to the worldwide COVID-19 outbreak.
Some traditional medical equipment makers haven’t pursued the ventilator business nor have a lot of top manufacturing companies like Tesla, GM, and others that are poised to produce ventilators. For them, it will be a steep learning curve.
But what they must embrace at the start is that PCBs are the basic electronics foundation for ventilators. Considering that electronics, device packaging technologies, and PCB SMT and microelectronics assembly have considerably advanced, these new ventilator makers—as well as traditional ones—must weigh a number of key PCB design, assembly, and manufacturing factors.
Given the severity of the coronavirus, quality is at the top-most requirement for this emerging flood of new life-saving ventilators. How does the ventilator OEM determine how to look for and gauge quality for PCBs, which are a ventilator product’s underpinnings?
Two other critical requirements ventilators demand are repeatability and reliability. For PCBs going into ventilators, those three requirements must be fully and conscientiously practiced at layout, fabrication, and assembly stages. At the same time, compliance with ISO 13485 not only complements those requirements, but also adds further muscle to assure quality, robustness, repeatability, traceability, and reliability. Therefore, it’s vital that ventilator OEMs assure that they are getting their product support from vendors who are ISO 13485:2016 compliant, as well as ISO 9001:2015 and RoHS compliant.
To help ensure quality, ISO 13485 is all about potential risks involved and mitigating these during and after the building of medical products, like ventilators. It is a specific ISO standard serving as a comprehensive management system for the design and manufacture of medical devices. Like other ISO standards, its focus is on continuous improvement in process and quality systems. Also, an emphasis on cleanliness procedures is placed and clearly listed as medical products undergo various development and production stages.
When it comes to assembly, reliability plays an especially important role. There are no shortcuts for the successful assembly of ventilator PCBs. The thermal profile is crucial. A particular profile must be correctly designed and implemented for a given PCB. One size does not fit all, and all thermal profiles aren’t created equal. Further, the CM or EMS provider must exercise special expertise when hybrid products containing leaded and lead-free components are subjected to re-flow. If care is not applied, an entire PCB project can be damaged, and those boards must be scrapped.
Also, properly defining a stencil design and solder paste dispensing is equally as important as a correct thermal profile. If the right paste, stencil, and correct profile are used, then about three-quarters of potential issues at the rework and touch-up rework phases are eliminated.
In addition, an assortment of advanced systems and equipment ensures quality and reliability. AOI is used to make sure of consistency; X-rays provide assurances that all joints are proper (Figure 1); and first article inspection (FAI) makes inspection and QC more reliable, repeatable, and faster. The more use of automation, the less human intervention is required, thus eliminating human error.
Figure 1: X-ray machine.
But let’s get back to ISO 13485 to expand it further. It demands considerable traceability. PCBs must be serialized and allocated in terms of batches. This means products being built can be traced by lot and batch codes. Even components populating PCBs must be traced.
A well-documented paper trail serving as the basis for traceability leads back to suppliers and manufacturers associated with those components. If there is an issue with those components during PCB design or assembly, that paper trail goes to those suppliers.
ISO 13485 also requires inspection documentation, process validation for sterile medical products like ventilators, and verification of how effective preventive and corrective actions are. Moreover, the standard determines the sequence and interaction of processes involving a medical product’s design and assembly An EMS provider, a CM, or an OEM are expected to maintain a file identifying all documents that define product specifications and quality management system requirements.
It’s also important to note that medical PCB assembly electronics require a different set of criteria than PCBs for commercial applications. For ventilator PCB assembly, this is crucial for ventilator OEMs to know. The Federal Drug Administration (FDA) requires specific documentation, especially verification of certain processes. Complying with FDA-approved documentation is considerably easier when an EMS provider or CM is ISO 13485 certified because ISO 13485 requires that in-depth traceability.
Lastly, an experienced EMS provider should always maintain a constant check on its assembly processes and procedures. The idea is to sustain assembly strengths at the highest levels possible to efficiently produce quality ventilators. Plus, those processes are made repeatable with minimal effort so that there are no surprises at QC stages.
Zulki Khan is the president and founder of NexLogic Technologies Inc.
More Columns from Zulki's PCB Nuggets
Zulki's PCB Nuggets: Cleanliness is Next to ReliabilityZulki’s PCB Nuggets: Thermal Compression Bonding for Extra Fine Pitch Flip Chips
Zulki’s PCB Nuggets: WBAN Steps Into PCB Microelectronics Assembly
Zulki’s PCB Nuggets: Photonics Comes to PCB Microelectronics Assembly
Zulki’s PCB Nuggets: Sub-Micron Die Bonding—Don’t Be Misled by Five Micron Placement Standard
Zulki’s PCB Nuggets: Meet the New Player in PCB Microelectronics Assembly—Interposers
Zulki’s PCB Nuggets: How Effective Is Your PCB Microelectronics Assembly?
Zulki’s PCB Nuggets: Five Key Benefits for Onshoring PCB Microelectronics Assembly