-
- News
- Books
Featured Books
- smt007 Magazine
Latest Issues
Current IssueWhat's Your Sweet Spot?
Are you in a niche that’s growing or shrinking? Is it time to reassess and refocus? We spotlight companies thriving by redefining or reinforcing their niche. What are their insights?
Moving Forward With Confidence
In this issue, we focus on sales and quoting, workforce training, new IPC leadership in the U.S. and Canada, the effects of tariffs, CFX standards, and much more—all designed to provide perspective as you move through the cloud bank of today's shifting economic market.
Intelligent Test and Inspection
Are you ready to explore the cutting-edge advancements shaping the electronics manufacturing industry? The May 2025 issue of SMT007 Magazine is packed with insights, innovations, and expert perspectives that you won’t want to miss.
- Articles
- Columns
- Links
- Media kit
||| MENU - smt007 Magazine
Estimated reading time: 4 minutes
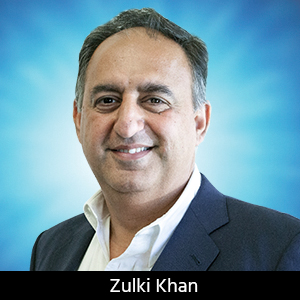
Zulki’s PCB Nuggets: Add Hi-rel to ISO 13485 for More Robust Ventilator PCBs
Consider that today, the supply chain for new ventilators required for COVID-19 patients may have several questionable links based on rushed and illogical decisions being made at all levels. Here, the buck stops with the ventilator OEM that may be duped into designing in PCBs that may not have undergone the rigors of FDA and ISO 13485 requirements, and thus, lack sufficient quality and reliability.
In my last column, I covered the importance of meeting FDA and ISO 13485 standard quality and reliability requirements for ventilators and other medical equipment. But there’s still more that ventilator OEMs need to put into practice, specifically in the high-reliability or “high-rel” area to further add to ISO 13485.
Going Above and Beyond
“Hi-rel” is most often associated with mil/aero PCB applications. But those same practices are synonymous with the high reliability expected for medical electronics, and again, in particular, to medical ventilators.
In both cases—mil/aero and medical equipment—added tolerances are built into processes and procedures as the foundation of hi-rel PCBs. In other words, it’s going above and beyond the regular ones applied to commercial PCBs. Here, the savvy ventilator OEM plugs in additional reliability at PCB design, fabrication, and assembly. Various key steps at each stage get an extra five to 20% reliability factor.
Let’s take PCB assembly, for example, where a number of small and large hi-rel steps can be performed to ensure nothing is left to chance. But at the same time, those steps in total crank up reliability to a hefty 60–65%.
Solder paste printing is a major one where fully automated pick-and-place machines with advanced vision systems are critical to properly align fiducial marks. These are very small registration marks printed on PCBs, which help vision machines to recognize and place the components optimally on the PCBs.
Also, at this solder printing stage, it’s important that either the printer efficiently measures the proper amount of dispensed solder paste on an empty pad or a standalone paste height inspection machine is used for that purpose (Figure 1).
Figure 1: A paste height inspection machine efficiently measures the proper amount of dispensed solder paste on an empty pad.
Component placement is then performed, followed by automated optical inspection (AOI) right before reflow. AOI ensures all placements are proper, and there are no angles, skews, misplaced components, and/or polarity problems as it pertains to polarized components. If and when issues arise here, they’re easy to fix by adjusting SMT placement without making any further changes. This is a critical PCB assembly step that plays a key role in regulating quality and reliability.
A correct thermal profile is also at the top of this hi-rel list. For commercial standard products, one to two iterations of the first article are executed to verify the thermal profile is correct. However, a hi-rel PCB requires three to four iterations of the first article to make sure an optimal profile is perfectly created and subsequently verified.
Increasing board reliability also includes applying conductive thermal compound to help dissipate heat more efficiently, soldering swages with heavy gauge wires to the pad and PCB, pre-tinning stranded wires when required to ensure sufficient solder, as well as a conformal coating when the application demands it.
The conductive thermal compound does several things to beef up hi-rel. For starters, it makes this assembly step 10% more reliable by dissipating heat more efficiently into the ambient. Plus, it reduces vibration, which can create lead solder cracking and effectively dissipates heat from adjoining components, too.
Flange mounts are normally press-fit on a commercial PCB. However, with a hi-rel PCB for medical ventilator applications, once flange mounts are press-fit, each swage is hand soldered with heavy gauge wire to the pad and the PCB. This assembly step minimizes vibration. Reliability, at these points on the PCB, is increased by an estimated five to 10%.
Pre-tinning involves dipping stranded or braided wire into hot melted solder, removing it, and drying, allow the solder formation to solidify. In short, soldering transforms stranded wire into one solid wire, eliminating air gaps and allowing current flow to be more stable. As a result, electromagnetic interference (EMI) effects and attenuation are reduced. Reliability is thus increased by another 5–10%.
Next, if certain components dissipate more than one watt of heat, they can use a spacer between the heat sink and the component itself. It permits component heat to be thermally dissipated, rather than permitting it to adversely affect all the circuits on that PCB.
This spacing also acts as stress relief, meaning that if the PCB and its end product are smashed or dropped in extreme conditions, there will still be sufficient clearance to protect components and keep the product operating. An estimated 10–15% reliability increase is realized by applying this spacing.
Lastly, savvy hi-rel PCB assembly houses working with medical equipment OEMs design solder stencils allow perfect solder flow dispensing on the PCB pads. This assembly step increases reliability by an estimated five to 10%. Moreover, for acceptable quality levels (AQL), medical equipment, and ventilator PCBs—just like mil/aero boards—must undergo 100% inspection to assure 100% reliability compared to the commercial standard of 0.65.
In summary, like EMS providers and CMs have always been vigilant about counterfeit components, medical ventilator OEM purchasing must be extra careful not to let unsuitable PCBs and components from entering their supply chain. Not only that, but those buyers should also ensure that their PCB purchases are backed by compliance with FDA regulations, ISO 13485 standard requirements, plus the added bonus of hi-rel from a reputable EMS provider.
Zulki Khan is the president and founder of NexLogic Technologies Inc.
More Columns from Zulki's PCB Nuggets
Zulki's PCB Nuggets: Cleanliness is Next to ReliabilityZulki’s PCB Nuggets: Thermal Compression Bonding for Extra Fine Pitch Flip Chips
Zulki’s PCB Nuggets: WBAN Steps Into PCB Microelectronics Assembly
Zulki’s PCB Nuggets: Photonics Comes to PCB Microelectronics Assembly
Zulki’s PCB Nuggets: Sub-Micron Die Bonding—Don’t Be Misled by Five Micron Placement Standard
Zulki’s PCB Nuggets: Meet the New Player in PCB Microelectronics Assembly—Interposers
Zulki’s PCB Nuggets: How Effective Is Your PCB Microelectronics Assembly?
Zulki’s PCB Nuggets: Five Key Benefits for Onshoring PCB Microelectronics Assembly