-
- News
- Books
Featured Books
- smt007 Magazine
Latest Issues
Current IssueWhat's Your Sweet Spot?
Are you in a niche that’s growing or shrinking? Is it time to reassess and refocus? We spotlight companies thriving by redefining or reinforcing their niche. What are their insights?
Moving Forward With Confidence
In this issue, we focus on sales and quoting, workforce training, new IPC leadership in the U.S. and Canada, the effects of tariffs, CFX standards, and much more—all designed to provide perspective as you move through the cloud bank of today's shifting economic market.
Intelligent Test and Inspection
Are you ready to explore the cutting-edge advancements shaping the electronics manufacturing industry? The May 2025 issue of SMT007 Magazine is packed with insights, innovations, and expert perspectives that you won’t want to miss.
- Articles
- Columns
- Links
- Media kit
||| MENU - smt007 Magazine
Estimated reading time: 5 minutes
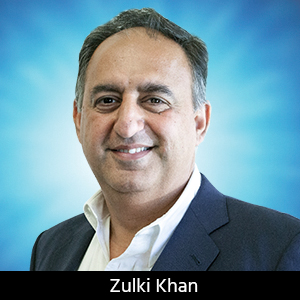
Zulki’s PCB Nuggets: Soft Electronics Pose PCB Microelectronics Assembly Challenges
Medical electronics has made significant technological strides in the last few years. Mostly, electronic devices used in medical equipment have become smaller, yet more complex and powerful. Meanwhile, PCBs have moved from traditional large rigid boards to considerably smaller rigid and combinations of rigid and flex circuit boards, even to the point that bare chips and wire bonding are used during the PCB microelectronics assembly of these tiny boards.
Accordingly, EMS providers and contract manufacturers have had to make PCB assembly adjustments, adopt new ways of thinking, retraining its personnel, and investing in newer, more advanced assembly and manufacturing equipment to set up PCB microelectronics assembly to deal with those smaller devices and boards.
Even with these PCB assembly advances, the demands being placed on medical electronics continue without ceasing because the medical profession requires newer, more innovative products to perform better and more advanced patient care. Against that backdrop, today’s medical research findings promise to take medical electronics to an unprecedented level, in a completely different direction, and in a different dimension not before seen. You can call it a definite paradigm shift because it involves soft and not hard components, which PCB assembly has traditionally dealt with.
Evidence of that has already emerged. Take, for example, the research work performed at MIT. Reports coming out of MIT research engineering labs detail the design of a so-called light-sensitive hydrogel, and it is extolled as a new avenue to revolutionize medical procedures. There is no doubt that there is something very special about this new development from the medical perspective, and it’s giving us pause in our industry.
That light-sensitive hydrogel can be integrated with medical devices that doctors insert into the human body to treat, diagnose, or monitor disorders. Once those devices are no longer needed, they can then be dissolved inside the body by exposing them to light from an ingestible LED. Therefore, this automatic elimination process saves doctors from performing endoscopic surgery to remove such devices.
This light-sensitive hydrogel for ingestible medical devices was the most recent development involving this particular hydrogel material. Five years earlier, however, another group of MIT engineers [1] developed “a rubbery material, mostly composed of water, designed to bond strongly to surfaces, such as gold titanium, aluminum, silicon, glass, and ceramic.” They called this material hydrogel, but this research centered on external human body applications.
It was described as a “water-based Band-Aid that senses temperature, lights up, and delivers medicine to the skin,” according to published reports [1]. Researchers said that it could also be used externally because they claim it has certain characteristics that are similar to human skin.
They called it a Band-Aid, in this instance, because this stretchable and flexible material could be applied to various parts of the body, like an elbow or a knee. A key advantage is the hydrogel keeps embedded electronics functional, robust, and intact. This is largely due to the fact it has good bonding strength like gold, titanium, aluminum, or silica gel, which are normally used in conventional PCB assembly.
Is It Too Far Out?
To many in PCB assembly and manufacturing, this business about new developments like light-sensitive hydrogel, ingestible, and insertable medical devices may be too far out in the future. Traditional large and small PCB assembly houses may be solely focused on day-to-day customer PCB production, and they’re not thinking about how to perform this new assembly and how to collaborate with the medical OEMs driving these newer technologies.
But to those with a keen interest in the future of medical electronics, it’s a good time to conduct preliminary meetings with those visionary medical OEMs. Certain aspects have to be considered when entering this new paradigm shift. For starters, data exchanges about chemical compounds should be on the discussion agenda.
Then, more specifically, discussions must be centered around how to create the microelectronics circuitry needed to embed it in the hydrogel. Further, exploratory talks should concentrate on ensuring that connectivity remains the same and that the hydrogel’s thickness is enough to implant micro-devices like flip-chips, die-attach, or micro-electromechanical systems (MEMS) into those hydrogels. That’s important to let us know that body functions can continue to properly perform and still allow the inserted medical device to be able to monitor in real-time the required diagnosis, analysis, or conditions of the body.
Furthermore, the usual concepts of conventional PCB assembly will require extremely close scrutiny and analysis. This study will help to determine if the usual ways of PCB assembly can apply to the new requirements that a soft hydrogel technology pose. This scenario presents questions as to how to incorporate electronics with signals floating from point A to point B. It also introduces the question of how to process different aspects of electronics into a jelly-like material. That step is critical to make sure those electronics work through sensors, MEMS, and biosensors and allow signal monitoring needed to observe human body conditions.
Other questions come into the mix. What about the circuit board itself? Will it be similar to a flex circuit, which features agility and nimbleness and isn’t a hard surface compared to FR-4 or other rigid material? Further, instead of soldering the components on a substrate, can an epoxy gel or something similar be effective? How long can signal wires operate effectively before starting to degrade? Controlling electromagnetic signals will be another point of careful evaluation while ensuring signal to noise ratio (SNR) in hydrogel embedded devices are within the tolerance listed in the spec sheet.
This is a whole new ballgame where you have different chemical and mechanical properties associated with new “soft electronics materials.” Plus, there’s also the issue of device selection and associated questions pertaining to LED brightness, its heat, and thermal expansion. And perhaps there may be new types of electronics devices that are more conducive for interacting with hydrogel material.
In short, we’re confronted with a brand-new thing. Navigating through this unknown phase and processes will be a true challenge for our industry. That’s why it’s never too early to begin collaborating with medical OEMs.
Reference
- J. Chu, “Stretchable hydrogel electronics,” MIT News Office, December 7, 2015.
Zulki Khan is the president and founder of NexLogic Technologies Inc.
More Columns from Zulki's PCB Nuggets
Zulki's PCB Nuggets: Cleanliness is Next to ReliabilityZulki’s PCB Nuggets: Thermal Compression Bonding for Extra Fine Pitch Flip Chips
Zulki’s PCB Nuggets: WBAN Steps Into PCB Microelectronics Assembly
Zulki’s PCB Nuggets: Photonics Comes to PCB Microelectronics Assembly
Zulki’s PCB Nuggets: Sub-Micron Die Bonding—Don’t Be Misled by Five Micron Placement Standard
Zulki’s PCB Nuggets: Meet the New Player in PCB Microelectronics Assembly—Interposers
Zulki’s PCB Nuggets: How Effective Is Your PCB Microelectronics Assembly?
Zulki’s PCB Nuggets: Five Key Benefits for Onshoring PCB Microelectronics Assembly