-
- News
- Books
Featured Books
- design007 Magazine
Latest Issues
Current IssueProper Floor Planning
Floor planning decisions can make or break performance, manufacturability, and timelines. This month’s contributors weigh in with their best practices for proper floor planning and specific strategies to get it right.
Showing Some Constraint
A strong design constraint strategy carefully balances a wide range of electrical and manufacturing trade-offs. This month, we explore the key requirements, common challenges, and best practices behind building an effective constraint strategy.
All About That Route
Most designers favor manual routing, but today's interactive autorouters may be changing designers' minds by allowing users more direct control. In this issue, our expert contributors discuss a variety of manual and autorouting strategies.
- Articles
- Columns
- Links
- Media kit
||| MENU - design007 Magazine
Estimated reading time: 5 minutes
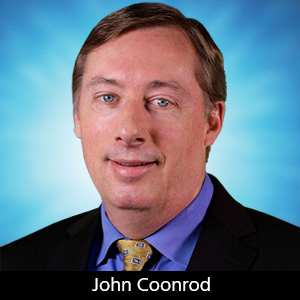
Lightning Speed Laminates: Understanding Material Interactions With PCB Fab Processes
Having a good understanding of the circuit material that a designer is working with, along with the potential PCB fabrication influences, is essential for having a successful first-time evaluation of a new circuit design. If a designer only considers the basic material properties of Dk and Df, that may not be enough information to have a successful first round of evaluations.
The Dk and Df values that are found on a material datasheet are typically generated with a non-circuit test method, which is usually a raw material test that is using some type of fixturing. If that same material is evaluated in circuit form, it is very common that the Dk and Df values will be different because the propagating wave on the circuit may have different influences than in a test fixture. Understanding how a circuit material behaves in circuit form can be very valuable to the circuit design process for achieving better circuit performance for the evaluations of a new design.
A topic that has been getting more attention over the past several years is copper surface roughness. The copper surface of concern is at the substrate-copper interface as the laminate is made and not the air side of the laminate. However, depending on how the circuit is made, the copper surface on the air side of the laminate can play a role in the impact that the surface roughness has on circuit performance. The copper surface roughness effect has been found to influence insertion loss, phase response, and propagation speed.
In a very general sense, when the speed of an electromagnetic wave is analyzed, a slower velocity will indicate a higher Dk value of the wave propagation medium. If two similar circuits are evaluated for the extraction of the material’s Dk value, the circuit with the slower wave speed (or increased propagation delay) will report a higher Dk value.
There are other circuit and material properties which can slow the propagating wave, besides the Dk of the material. The copper surface roughness can slow the wave and cause the Dk extraction from the circuit evaluation to report a higher Dk than what the material possesses. We conducted a simple experiment years ago that conclusively showed the influence of copper surface roughness on the Dk extraction process. Figure 1 provides a simple overview.
Figure 1 shows the results of testing laminates in circuit form, using the microstrip differential phase length method, which uses microstrip transmission line circuits of different lengths. Before the laminates were made, the copper surface roughness was evaluated using a non-contact laser profilometer, and the average roughness values are reported in the legend of the chart.
After determining the surface roughness of these four different types of copper, the same dielectric material was used to make four laminates. The laminates were fabricated into microstrip circuits and evaluated for effective dielectric constant based on phase angle measurements. The effective dielectric constant (the Y-axis of Figure 1) is the dielectric constant that the wave experiences. For a microstrip circuit, it is a combination of the dielectric constant of the substrate and air.
Figure 1 shows four distinct trends of an increased Dk curve for an increased copper surface roughness. Basically, circuits using a smooth copper (red curve) will not slow the wave much, and the reported effective Dk will be closer to the ideal value. A circuit using copper with a much rougher surface (blue curve) will slow the wave significantly, and the reported effective Dk value will be much higher than the ideal effective Dk value of the substrate-air combination.
Keep in mind that the same dielectric material was used for collecting data reported in this chart, and there is a difference of 0.3 for effective Dk, which is due to differences in copper surface roughness only. This is very important because if the dielectric material is evaluated in a fixture without copper roughness effects, the Dk values will be significantly different than shown in this chart. Additionally, if a thicker substrate is used, which implies the copper planes are farther apart, the influence of copper surface roughness is reduced, and the reported effective Dk value will decrease. The copper roughness effects can be very important to understand for determining the proper Dk value to use for circuit design and simulation.
There is a complication in which the circuit design and construction can be more or less sensitive to the copper surface roughness effects. The microstrip circuit example given is relatively easy to understand for the effects of copper surface roughness. However, for a stripline circuit, which has four substrate-copper interfaces, the influence of surface roughness on circuit performance is more complicated. The stripline circuit can have very different surface roughness effects due to how the circuit is constructed. A stripline circuit fabricated using a foil lam construction can have a very different copper roughness influence than a stripline made as a core lam construction.
There is also the potential influence of some PCB fabrication processing effects on the extracted Dk of a material when tested in circuit form. One of these influences can be the copper plating thickness and its normal variation. Another influence can be the final plated finish and its variation. The copper plated thickness and its variation, as well as the final plated finish and its variation, can have a significant impact on circuit features that are edge coupled.
These potential influences on circuit performance, which can affect the extracted Dk value of the material, will depend a lot on the circuit design and construction. Most designers consider the final plated finish in relation to insertion loss differences; however, the plated finish can certainly impact the phase response of the circuit, which can alter the extracted Dk value of the material from a circuit evaluation.
The bottom line for getting good results for a first-time evaluation of a new circuit design is for the designer to understand the material properties, test methods, and influences of circuit fabrication for their particular design concept. These are a lot of issues to consider, and it is best to have the designer work closely with their material supplier and the PCB fabricator to ensure the best results for the initial circuit evaluation of a new design.
This column originally appeared in the December 2020 issue of Deisgn007 Magazine.
More Columns from Lightning Speed Laminates
Lightning Speed Laminates: Millimeter-wave Properties and PCB Design ChallengesLightning Speed Laminates: Optimizing Thermal Management for Wireless Communication Systems
Lightning Speed Laminates: Test Vehicles for PCB Electrical Material Characterization
Lightning Speed Laminates: Optimum Thermal Stability Considerations
Lightning Speed Laminates: Thermal Management Isn’t Getting Easier
Lightning Speed Laminates: Benefits of High-Performance Hybrid Multilayer PCBs
Lightning Speed Laminates: An Overview of Copper Foils
Lightning Speed Laminates: The Importance of Circuit Features for Millimeter-Wave Applications