-
- News
- Books
Featured Books
- smt007 Magazine
Latest Issues
Current IssueWhat's Your Sweet Spot?
Are you in a niche that’s growing or shrinking? Is it time to reassess and refocus? We spotlight companies thriving by redefining or reinforcing their niche. What are their insights?
Moving Forward With Confidence
In this issue, we focus on sales and quoting, workforce training, new IPC leadership in the U.S. and Canada, the effects of tariffs, CFX standards, and much more—all designed to provide perspective as you move through the cloud bank of today's shifting economic market.
Intelligent Test and Inspection
Are you ready to explore the cutting-edge advancements shaping the electronics manufacturing industry? The May 2025 issue of SMT007 Magazine is packed with insights, innovations, and expert perspectives that you won’t want to miss.
- Articles
- Columns
- Links
- Media kit
||| MENU - smt007 Magazine
Estimated reading time: 6 minutes
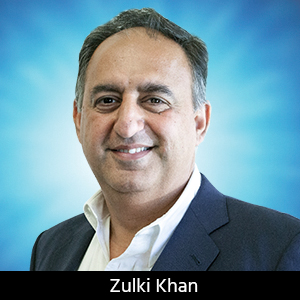
Zulki’s PCB Nuggets: Is U.S. Production Ready for Advanced Medical Devices?
The outlook appears promising in 2021 for electronics OEMs to bring some or most of their manufacturing back to the U.S. In particular, medical electronics OEMs may be able to move forward with their prototypes into pilot, medium, and high runs right here on American soil. And it may be sooner than later due in large part to the advances in PCB microelectronics assembly and perhaps a helping hand from the U. S. Government.
Let’s take a look at what is driving those advances in microelectronics and what is now possible. There is an abundance of news reporting on such advanced medical devices as wearables, portables, and insertable and ingestible products in the planning and development stages. Those types of new products require technologies associated with PCB microelectronics assembly, such as wire bonding, chip on board (CoB), flip chip, and die attach, among others.
Therefore, the stage is now set for prototype quantities as proof of concept to move on to pilot, medium, and high runs so that the intellectual property (IP) of these state-of-the-art medical devices is safe and staying here in the U.S. Pilot runs deal with a few hundred to a few thousand units; depending on the product, medium runs could be a few thousand to tens of thousands of units; and high runs involve hundreds of thousands in quantity.
Let’s go through these assembly and manufacturing stages and check out PCB microelectronics assembly challenges and what is possible (may lay in store) for medical OEMs. Or put another way, what is involved in transitioning medical electronics PCBs from small prototype quantities into volume production?
Get in the Right Mindset
Proof of concept at the outset of prototyping isn’t so much focused on ease of production and testability. Instead, the emphasis is more toward process development to find a workable solution and a fully functioning product. This process typically can extend into two to three iterations, either in traditional SMT manufacturing or in PCB microelectronics labs.
This is especially true for microelectronics assembly that has a cleanroom environment with extra sensitive material and special equipment for assembling medical insertable and ingestible devices. So, at the earliest prototype stages, the PCB assembly mindset must change. That means focusing on ease of production and testability rather than on process development. This would be difficult to practically implement, as proof of concept is the desired outcome rather than product maturity and process development. The next best thing would be to make the process mature and stable at the tail end of the prototype development.
Although it may sound confusing, there must be assurances that the process is solid when transitioning from prototype to pilot runs. Dies, for example, need to be in a specific format for pick-and-place machines to pick these up in the cleanroom. For example, when performing prototypes, there may or may not be a preference for the way dies are picked up. But for production, a well-defined process is absolutely necessary with even the minutest detail worked out.
A diced wafer can be pulled through vacuum and placed on an interposer, substrate, or PCB. That is acceptable for five, 10, 15 or even 100 units. But when it comes to production, there are several aspects that need to be considered and incorporated into production runs for the pick-and-place stages for pick and place details along with fiducial marks on dies and substrates.
Number one, dispensing material needs to be fully automated, regardless whether epoxies or other materials are being dispensed on the board, substrate, or underneath the dies. This requires carefully dialing the dispensing parameters and making sure these substances are not under or over dispensed.
Number two, especially when it comes to PCB microelectronics, an infrastructure combining machines and capabilities is critical to automatically pick up dies for production runs. These are dies that should be picked up from a common carrier, like waffle or gel pack rather than diced dies from a wafer. Also, there needs to be a pick-and-place high-speed die attach machine, as well as high-speed wire bonding equipment, to make sure production run speeds are properly maintained.
Also, having the microelectronics assembly process conveyorized or in-line like in traditional SMT manufacturing makes it production friendly. In a conveyorized microelectronics assembly, you can have a dispenser, pick-and-place machine, and wire bonder. Everything is conveyorized and in-line so that one function after another can be performed without physical human intervention. This makes the whole process optimized, fast, efficient, and reliable. But, still, there are other things needed to make these production stages happen smoothly, efficiently, and optimally.
Jigs, tools, and fixtures are needed to make the flow of different processes in multiple formats go through easily. You might have a fixture, jig, or tool that can do one product or placement at a time when dealing with small prototype quantities of 10 to 20 to 30 units. However, when you’re talking about a few hundred to a few thousand units, specialized tools and fixtures that take multiple products need to be produced to make the production optimized. We also have to look at the PCB—whether it’s a flex board for ingestible or insertable devices, bio-degradable material for ingestible devices, or rigid-flex—to make sure they are manufactured in optimized panels, rather than one-up.
Also consider that these are very tiny circuit boards, and they are processed in panel form. Ten or so are on a panel that undergoes dispensing, pick and place, and wire bonding. Compared to traditional assembly, in this instance 10 boards are undergoing this assembly step versus one assembly at a time.
The same process is repeated one time in a one-up setup versus the same process repeated for a panelized 10-unit product, essentially saving time and money. Therefore, special tools, jigs, and fixtures need to be created to be able to make the transition at the same time from prototype to pilot, medium, and production runs.
Further, it’s important to utilize automated tools and robotics as much as possible. Robotics, with its vision system in particular, makes the process a lot easier for placement accuracy. Those assembly systems measure with a laser beam to keep accuracy intact, which is especially critical for microelectronics involving CoB, flip chip, and wire bonding.
We are talking about accuracies in sub-mils and in some cases, microns. Sometimes, one- or two-micron accuracies are needed to make those portable and wearable devices. Robotics and automated equipment would make it a lot easier for making the transition from prototype to production.
At the same time, we must make sure that we have batch modules for testing the devices after the whole assembly is performed as part of the final quality assurance process.
When production units are completed, sample size for testing must be defined. This involves how testing small-to-medium run products can be tested in a short period of time. In some cases, test fixtures and test programs must be made, which can test and measure different units at the same time. This allows production to run efficiently and in a very small period.
Keeping IP in the U.S.
In summary, our industry has made significant headway toward production units for advanced medical products such as wearable, portable, ingestible, and insertable devices. We’ve got the knowhow and equipment for the necessary PCB microelectronics assembly and manufacturing. But even more CAPEX is necessary to assure production stays in this country, and can be performed conveniently and as easily as possible.
Keeping these products in the U.S. protects the medical OEM’s IP since there is virtually no theft when it comes to manufacturing within the U.S. due to stringent laws. These are strong safeguards that are available to OEMs. Plus, the other major benefit is that logistics and supply chains are here in the U.S. OEM personnel can eliminate costly and time-consuming travel back and forth between the U.S. and offshore countries where production has been located.
This column originally appeared in the January 2021 issue of SMT007 Magazine.
More Columns from Zulki's PCB Nuggets
Zulki's PCB Nuggets: Cleanliness is Next to ReliabilityZulki’s PCB Nuggets: Thermal Compression Bonding for Extra Fine Pitch Flip Chips
Zulki’s PCB Nuggets: WBAN Steps Into PCB Microelectronics Assembly
Zulki’s PCB Nuggets: Photonics Comes to PCB Microelectronics Assembly
Zulki’s PCB Nuggets: Sub-Micron Die Bonding—Don’t Be Misled by Five Micron Placement Standard
Zulki’s PCB Nuggets: Meet the New Player in PCB Microelectronics Assembly—Interposers
Zulki’s PCB Nuggets: How Effective Is Your PCB Microelectronics Assembly?
Zulki’s PCB Nuggets: Five Key Benefits for Onshoring PCB Microelectronics Assembly