-
- News
- Books
Featured Books
- smt007 Magazine
Latest Issues
Current IssueWhat's Your Sweet Spot?
Are you in a niche that’s growing or shrinking? Is it time to reassess and refocus? We spotlight companies thriving by redefining or reinforcing their niche. What are their insights?
Moving Forward With Confidence
In this issue, we focus on sales and quoting, workforce training, new IPC leadership in the U.S. and Canada, the effects of tariffs, CFX standards, and much more—all designed to provide perspective as you move through the cloud bank of today's shifting economic market.
Intelligent Test and Inspection
Are you ready to explore the cutting-edge advancements shaping the electronics manufacturing industry? The May 2025 issue of SMT007 Magazine is packed with insights, innovations, and expert perspectives that you won’t want to miss.
- Articles
- Columns
- Links
- Media kit
||| MENU - smt007 Magazine
Estimated reading time: 4 minutes
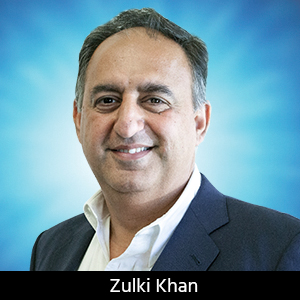
Zulki's PCB Nuggets: Take a Deep Dive Into U.S. Medical Device Production
Our country has welcomed a new administration in Washington D.C. Again, as in previous administrations, a major part of the new president’s agenda is to bring back to the U.S. manufacturing that has long been handed over to overseas giants.
Let’s revisit that subject now for newer perspectives on practices and different angles involving offshore conventional SMT manufacturing. It’s well known and documented that U.S. OEMs factor in cost, lead times, and intellectual property (IP) security when deciding whether to keep production stateside or sub it out to a low-cost overseas center.
However, there are new angles, new thinking emerging for medical OEMs to consider in order to keep production in the U.S. vs. overseas. The foremost thinking (biggest challenge) associated with those angles focuses on whether the product can be produced cost effectively in a timely fashion, so it’s distributed in the supply chain for a given medical device OEM.
We must admit that overseas production houses are exceptionally well organized for making production quantities in terms of using well-proven processes, delivering product details, having a disciplined infrastructure, and providing low-cost labor.
Therefore, it is prudent for medical OEMs to take an extra measure of time to understand and fully realize the capabilities an EMS provider offers in the U.S. Certainly, personally visiting their facilities is at the top of that list. But it’s not just one visit. It should involve several visits to get an in-depth understanding for the manufacturing capabilities, especially when it comes to microelectronics.
More than that, medical OEMs need to take a deep dive into claims an EMS provider makes. Sure, they can claim they can supply certain levels of quantities at certain price points, resolve certain complex logistic issues, and provide certain turn times for product manufacturing and distribution.
That deep dive means you must make sure you do a complete, detailed audit driven by process, quality, and supply chain teams. A comprehensive audit in all those and other areas allows you to properly verify and certify that a certain U.S. production house is indeed capable of doing those types of quantities.
By performing these detailed audits with multiple OEM teams to qualify a specific vendor, all the shortcomings and deficiencies of EMS companies are uncovered.
A deep dive also involves a comprehensive analysis of an EMS provider’s processes, protocols, and infrastructure capabilities. This step verifies they can make the product they claim they can provide. However, that analysis cannot be seen on the surface. Rather, you need proof you can see, which is the exact reason you as an OEM customer needs to conduct these detailed audits.
This is where manufacturing process instructions, or MPIs, come in to verify each detail in the different documents and subdocuments which are needed to make the product. Reviewing these detailed MPIs assures the claims that an EMS company makes can, in fact, be fulfilled.
Also, medical OEMs need to look into an EMS provider’s capabilities for scaling up or scaling down production. This means that when you’re doing forecasting you realize that production demand has changed from month to month, quarter to quarter, and in some cases, even a few weeks at a time.
So, the question becomes, how capable is the EMS company for scaling up or scaling down the demand? If scaled down, what are the pitfalls? What are the cost considerations? What are lead time constraints if product capacity on the line is increased, for example, 20 or 30%? How strong are the execution teams at EMS companies to handle these production quantity changes?
You also must consider product costing that comprises of two factors: bill of material (BOM) cost, and labor. Of course, labor is cheaper overseas compared to the U.S. But, here in the U.S., how can EMS providers mitigate some of the labor cost for production quantities? Also, what about BOM cost? Do U.S. EMS companies have some value-added capabilities?
For example, do they offer what’s known as “extreme combing through” or scrubbing? Scrubbing the BOM or substitution replacement is a way to determine the lowest possible cost component substitutes. How good are their component engineering teams?
Also, what about automation? As the top technology world leader, the U.S. is increasingly putting automation in place in virtually every major manufacturing plant. In some cases, automation is making its move into medium- to large-PCB manufacturing floors.
Automation plays its role by performing bulk projects together. Automation and robotics are used to assure labor content is as low as possible when manufacturing the product.
Automation needs to be done very carefully as well because when it comes to traditional SMT manufacturing, there are many steps and touch points from humans that need to be carefully studied before making automation decisions.
Some U.S. companies are taking the lead to make automation advances and changes in their production lines. In effect, U.S. manufacturing leaders are not only competing with offshore manufacturers, but more importantly, they are setting the model for U.S. PCB assembly and manufacturing houses to offer their medical OEM customers the opportunity to remain stateside and move expeditiously from prototyping to production.
Zulki Khan is the president and founder of NexLogic Technologies Inc.
More Columns from Zulki's PCB Nuggets
Zulki's PCB Nuggets: Cleanliness is Next to ReliabilityZulki’s PCB Nuggets: Thermal Compression Bonding for Extra Fine Pitch Flip Chips
Zulki’s PCB Nuggets: WBAN Steps Into PCB Microelectronics Assembly
Zulki’s PCB Nuggets: Photonics Comes to PCB Microelectronics Assembly
Zulki’s PCB Nuggets: Sub-Micron Die Bonding—Don’t Be Misled by Five Micron Placement Standard
Zulki’s PCB Nuggets: Meet the New Player in PCB Microelectronics Assembly—Interposers
Zulki’s PCB Nuggets: How Effective Is Your PCB Microelectronics Assembly?
Zulki’s PCB Nuggets: Five Key Benefits for Onshoring PCB Microelectronics Assembly