-
- News
- Books
Featured Books
- design007 Magazine
Latest Issues
Current IssueProper Floor Planning
Floor planning decisions can make or break performance, manufacturability, and timelines. This month’s contributors weigh in with their best practices for proper floor planning and specific strategies to get it right.
Showing Some Constraint
A strong design constraint strategy carefully balances a wide range of electrical and manufacturing trade-offs. This month, we explore the key requirements, common challenges, and best practices behind building an effective constraint strategy.
All About That Route
Most designers favor manual routing, but today's interactive autorouters may be changing designers' minds by allowing users more direct control. In this issue, our expert contributors discuss a variety of manual and autorouting strategies.
- Articles
- Columns
- Links
- Media kit
||| MENU - design007 Magazine
Estimated reading time: 4 minutes
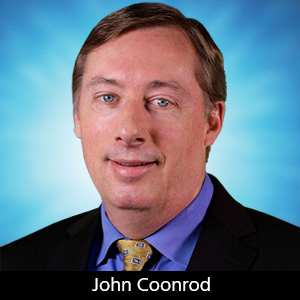
Lightning Speed Laminates: Things to Consider When Creating a Circuit Material Library
There are multiple libraries of information nowadays for a PCB fabricator. A circuit material library for the fabricator can be advantageous for multiple reasons. Sometimes these libraries are intended to be used for electrical predictions, such as impedance, insertion loss or other issues. Other times the information found in the circuit material libraries are used to assist with thermal issues, potential reliability concerns, circuit construction stackups, and some processing issues.
When a PCB manufacturer is creating and building a circuit materials library, there are some property values which should be defined by the circuit fabricator while other property values should be obtained from the circuit material supplier. As general statements, the circuit material property values which can be affected by the PCB fabricator should have data that was collected by the fabricator using their specific processes. The circuit material properties which are unaffected by circuit fabrication can be obtained from the circuit material supplier.
The common circuit material properties which can be affected by the fabricator are related to some of the electrical evaluations which the circuit manufacturer performs. It is common for a PCB supplier to perform impedance testing on the final circuit, as a “go/no-go” test for shipping the product. The material properties which relate to impedance are dielectric constant (Dk), substrate thickness, and copper thickness. Most PCBs today are using plated through-hole (PTH) technology, which means the final and overall copper thickness of the circuit can be influenced by the PCB fabrication process. The substrate thickness issue depends on the circuit construction, and in the cases of a foil lam construction, the thickness control is influenced somewhat by the PCB fabricator.
The Dk of the material is relatively fixed by the material supplier, however for some materials there can be a slight alteration of the Dk value due to material interaction with certain PCB processes. With these considerations in mind, the PCB fabricator should do studies with these variables, using a circuit material of choice, to define data which can be used in the material library for impedance modeling. The circuit material library will have data that is tailored to the circuit material being processed at that specific PCB fabricator.
The circuit material supplier can certainly assist by giving the fabricator more detailed information for the material properties, as the material is tested at the supplier using the material supplier’s test method. Many of the high frequency circuit material suppliers use the IPC-TM-650 2.5.5.5c test method to report Dk at 10 GHz. This test method is a raw material test and is not affected by circuit fabrication. As an example, the IPC test method uses a clamped fixture and there is some amount of entrapped air to be expected. The entrapped air has a very small effect, but air does have a Dk of about 1. The reported Dk with the clamped test method will often be lower than if the material is tested in circuit form without entrapped air.
Another reason for the PCB fabricator to build their database based on their process is the fabricator will often have a choice of what copper foil to use in a foil lam construction. The bond surface of the copper foil, and specifically the roughness of that surface, can impact the “circuit perceived Dk” or as Rogers Corporation calls it, design Dk. Again, with the PCB fabricator having the ability to alter the circuit performance due to the choice of copper foil, they should be defining the Dk values used per their process and with the copper they use.
The properties which the circuit material library should use from the material supplier are typically things like CTE, Tg, peel strength, moisture absorption, thermal conductivity, etc. These properties are innate to the material and they are typically not affected by the PCB fabrication process. Peel strength could be the exception on this list, where certain PCB processes can cause this property value to change. Peel strength (or bond strength) may be a good property value for the fabricator to gather information from the material supplier and then perform their own study and compare results with the material supplier.
When using data from a material supplier, the PCB fabricator should be very familiar with the test methods used by the supplier. A noteworthy example would be the material property of thermal conductivity. Thermal conductivity can be determined by several different test methods and the results may or may not be appropriate for how the circuit fabricator will apply the data. One test method for thermal conductivity used for laminate evaluations will include the effects of copper. A different test method will not include the effects of the copper. Since copper has a very high thermal conductivity, the influence of copper can make the results significantly different when comparing these two test methods for an evaluation of the same laminate. Depending on how the PCB fabricator will use the thermal conductivity information, they may or may not want to have the copper effects included.
It is always good advice for the PCB fabricator to work closely with the material supplier and that is especially true when the fabricator is developing a material database.
This column originally appeared in the February 2021 issue of Design007 Magazine.
More Columns from Lightning Speed Laminates
Lightning Speed Laminates: Millimeter-wave Properties and PCB Design ChallengesLightning Speed Laminates: Optimizing Thermal Management for Wireless Communication Systems
Lightning Speed Laminates: Test Vehicles for PCB Electrical Material Characterization
Lightning Speed Laminates: Optimum Thermal Stability Considerations
Lightning Speed Laminates: Thermal Management Isn’t Getting Easier
Lightning Speed Laminates: Benefits of High-Performance Hybrid Multilayer PCBs
Lightning Speed Laminates: An Overview of Copper Foils
Lightning Speed Laminates: The Importance of Circuit Features for Millimeter-Wave Applications