-
- News
- Books
Featured Books
- design007 Magazine
Latest Issues
Current IssueProper Floor Planning
Floor planning decisions can make or break performance, manufacturability, and timelines. This month’s contributors weigh in with their best practices for proper floor planning and specific strategies to get it right.
Showing Some Constraint
A strong design constraint strategy carefully balances a wide range of electrical and manufacturing trade-offs. This month, we explore the key requirements, common challenges, and best practices behind building an effective constraint strategy.
All About That Route
Most designers favor manual routing, but today's interactive autorouters may be changing designers' minds by allowing users more direct control. In this issue, our expert contributors discuss a variety of manual and autorouting strategies.
- Articles
- Columns
- Links
- Media kit
||| MENU - design007 Magazine
Estimated reading time: 4 minutes
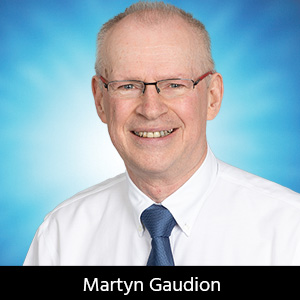
The Pulse: PCB Design Education—What ‘They’ Don’t Tell You
Lots of people are far more qualified than I am to talk about PCB design, but what fascinates me about both PCB and electronic design is the range of disciplines you need to be aware of, especially when moving into high speed/high power/high reliability arenas. For a new designer entering this space for the first time, it can be quite an eye-opener (no wordplay intended) to discover just how many different disciplines are involved in turning a good design into a fit-for-purpose PCB.
Specialist in How Many Disciplines?
One of the changes that has engulfed all industries in the past 50 years is the increasing level of specialisation required. Gone are the days when an engineer could have an idea, design the electronics, lay the board out, and maybe even build and etch the PCB themselves. When Polar was founded in the mid-1970s, that’s just what could happen. And while this is still possible for the most basic of designs, a PCB designer now needs to at least be aware of a whole spectrum of specialist disciplines which will entail dealing with other companies and industry professionals, to determine where, and where not, external advice is needed for a specific design.
Material Choices
The proliferation of materials in the past 20 years means that a new designer is faced with a bewildering choice of materials for any design; the temptation to “mix and match” to ensure best performance/value for money trade-off means a designer will often need to speak to a base materials specialist for OEM work, or their PCB supplier, or a PCB value-added reseller. Many of these companies now employ former fabrication staff with extensive materials knowledge. Stretched supply chains mean these specialist intermediaries can help especially on low volume or prototype orders.
What to Ask?
I often encounter designers who are reluctant to ask about fabrication and materials as they only feel comfortable asking “when they know what to ask.” I also see some new designers who try to infer everything off a material datasheet, and whilst this gets part of the way to the answer, the datasheet is just that—information about a raw material that the fabricator “processes” into a finished product. Just like baking a loaf of bread, the raw ingredients for a PCB are not the same as the finished product. Pretreatment for adhesion and pressing impact the raw material in a way which will be fabricator dependant and will differ from the raw material specs. Not quite as extreme as trying to make a sandwich out of a bag of raw flour, but you get the picture. If you don’t know what to ask, there are plenty of YouTube resources that cover PCB topics, along with the networks related to industry bodies like IPC and EIPC. These organizations aim to bring together networks of specialists with disciplines from chemistry through metallurgy, drilling, high-speed signalling, reliability, and thermal capability.
More and More
As technology pushes higher speed, more density and more durability, and legislation restricts the use of some materials, there seems to be ever more to contend with from a designer’s perspective. As I mentioned, the only way to deal with this is to discuss requirements for each design with the appropriate source of knowledge from each discipline. The key for a new designer is to be aware that, depending on the design, non-electronic parameters interplay with the design outcome. It is quite fascinating to me that so many disparate disciplines need to work in harmony to produce the most fit-for-purpose design at the most economical cost.
Sometimes the Laws of Physics Work in Your Favour
Fortunately, sometimes technology drives in a direction to make life easier; the drive to ever-shrinking designs means that often high-speed traces can be kept quite short—so short that some parameters which need careful treatment on a larger scale can be of low enough impact to be ignored. Insertion loss is one case where loss is directly proportional to trace length, so keeping traces short can mean you can perhaps build on a lower grade base material. If the traces are very short compared with the highest frequency content, maybe characteristic impedance is not an issue there either.
A Sticky Problem
On the highest-speed interconnects, it is well known that copper roughness impacts the signal losses, and complex modelling is needed to calculate the impact, but the roughness is a “necessary evil” to keep the board from delaminating in the assembly process. Here, the chemists are working their magic to provide treatments and processes that chemically bond the copper to the dielectric, and emerging processes for bonding smooth copper could ease one task from the list of design considerations over the coming years.
Conclusion
A new PCB designer, apart from knowledge of layout—which is after all the job description—needs to be aware and ready to discuss a range of peripheral influencers on the PCB’s characteristics, many of which would seem to the casual observer to have no connection whatsoever to electronic interconnect. However, from an industry which measures time in inches, and thickness in ounces, that surely should come as no surprise.
This column originally appeared in the August 2021 issue of Design007 Magazine.
More Columns from The Pulse
The Pulse: Design Constraints for the Next GenerationThe Pulse: Ultra Upgrade Unknowns—What’s Coming for UHDI?
The Pulse: Commonsense Cost Cutting
The Pulse: Overconstraining: Short, Slim, and Smooth
The Pulse: Drilling Down on Documentation
The Pulse: New Designer’s (Partial) Guide to Fabrication
The Pulse: Simplest Stackups Specified
The Pulse: Rough Roughness Reasoning