-
- News
- Books
Featured Books
- design007 Magazine
Latest Issues
Current IssueProper Floor Planning
Floor planning decisions can make or break performance, manufacturability, and timelines. This month’s contributors weigh in with their best practices for proper floor planning and specific strategies to get it right.
Showing Some Constraint
A strong design constraint strategy carefully balances a wide range of electrical and manufacturing trade-offs. This month, we explore the key requirements, common challenges, and best practices behind building an effective constraint strategy.
All About That Route
Most designers favor manual routing, but today's interactive autorouters may be changing designers' minds by allowing users more direct control. In this issue, our expert contributors discuss a variety of manual and autorouting strategies.
- Articles
- Columns
- Links
- Media kit
||| MENU - design007 Magazine
Estimated reading time: 4 minutes
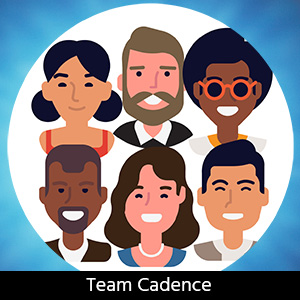
All Systems Go! Comprehensive Thermal Analysis of a System Design
In recent years, driven by the demand for smarter electronics, device designers have witnessed enormous scaling of large and hyperscale integrated circuits (ICs) and embraced development directions toward high density and reliability. These devices have increasingly higher thermal performance requirements—both transient and steady-state—and meeting them is becoming increasingly complex and time consuming.
Thermal Integrity and Challenges
Today, ensuring thermal integrity of an electronic device is a multi-dimensional problem. It straddles both the active (transistors and ICs) and passive (resistors, capacitors, and inductors) components, as well as the associated mechanical connectors and thermal dissipation elements. With all these mounted on one or more PCBs, ensuring thermal integrity across this full spectrum of components and related materials is a major and growing challenge. Not addressing thermal issues leads to thermal stress and early failure. As a designer, the typical challenges you face are:
- Performance is driving the need for accuracy, and hence the demand, for 3D thermal modeling of the system including all the components—active, passive, and mechanical
- Inability to accurately model the conduction, convection, and radiation of heat throughout the system
- Simulating and analyzing the thermal behavior of the system, both transient and steady state is becoming impossible with the proven legacy solutions because they are unable to scale to absorb the growing density and complexity of today’s system designs
- The lack of accurate electrothermal co-simulation often leads to field failures
- Extensive prototyping is a major drag on cost and time to market
Proper thermal management calls for design measures that must be taken based on the other operational environment conditions, such as temperature, humidity, power, thermal fluid density, volume, heat sink, etc., to ensure even distribution of temperature and reasonable rise within regulated limited values. It is essential to model the conduction, convection, and radiation of heat throughout the system. This in turn means that it’s necessary for you to model airflow inside and outside of the system, while understanding that the dynamics of this flow and its capacity to remove heat will be modified by the thermal environment it encounters.
A major underlying problem with legacy system analysis tools is the fact that they were conceived and developed in the era of single-core computing, which means they just don’t scale well, even if they are running on multi-core systems with multiple threads running on each core.
Figure 1: Airflow analysis.
Overcoming Thermal Challenges
Let’s consider an example where a transistor is required to operate at a certain peak power output and maintain an optimal temperature by applying all the thermal handling enhancements along with RSENSE-installed targets (that are required to have the minimum allowable temperature).
Figure 2: FEA with CFD.
In the above scenario, legacy tools help you determine the temperature on the surface of the component but lack the capacity and performance to solve inside the components to determine the temperature gradient down to the transistor. In addition, running a true 3D electromagnetic is a challenge due to the cross-software compatibility issues. When the design includes 3D-ICs, it becomes a major challenge for legacy tools.
Overcoming thermal challenges undoubtedly requires multiphysics simulation technology, which can solve thermal complexity while simplifying the process of varying test limits and inputs. When powered by solvers architected for massive parallelization while not sacrificing on accuracy, you get the ability to analyze large systems that couldn't be analyzed previously.
System-level thermal analysis of all electronic devices requires both finite element analysis (FEA) and computational fluid dynamics (CFD) approaches to ensure the effects of conduction, convection, and radiation are all taken into consideration. Since the accuracy of modeling and analysis is important for ensuring thermal integrity, using one thermal analysis solution with both solvers is an advantage. Yet another capability that is becoming a critical advantage for designers is to use an accurate 3D thermal solver that is natively integrated with the implementation solutions, ICs, packages, and PCBs.
Conclusion
Most electrical simulations can be replaced if you have a complete electrothermal co-simulation solution for the full hierarchy of electronic systems, from ICs to physical enclosures. This will enable seamless progression by establishing CFD and 3D modeling in the prototyping stage, achieving significant process improvement in predicting board performance and eliminating iterations during prototyping, and reducing time-to-market and cost.
An effective and efficient thermal solution takes an integrated set of tools and flows to address scalability, performance, and accuracy in the design and analysis of systems, both at the component and at the system levels. For today’s system-level high-frequency product designs, users need SoC and system-level tools that can support:
- Massively parallel execution to deliver faster and accurate solutions
- Seamless integration with IC, package, and PCB implementation platforms, which can accelerate and simplify design iterations
- Transient as well as steady-state analysis that can enable accurate electrothermal co-simulation
- Total system analysis using a combination of FEA and CFD approaches
Suketu Desai is senior director of product engineering, Multiphysics System Analysis Group, Cadence Design Systems Inc.
More Columns from All Systems Go
All Systems Go: Auto-Detecting Over- and Under-Derated PartsAll Systems Go: Time Traveling to 2030 for ML-Augmented PCB Design
All Systems Go: Accelerate Your PCB Designs with Machine Learning
All Systems Go: Can You Design Without Electronic Data Management?
All Systems Go! Supply Chain Woes—Which Comes First, the Design or the BOM?
All Systems Go! Find and Fix Thermal PCB Problems Sooner Than Later
All Systems Go! Ensuring Power Integrity—Explore, Design, and Verify
All Systems Go! Bridging the Gap Between Design and Analysis