-
- News
- Books
Featured Books
- design007 Magazine
Latest Issues
Current IssueProper Floor Planning
Floor planning decisions can make or break performance, manufacturability, and timelines. This month’s contributors weigh in with their best practices for proper floor planning and specific strategies to get it right.
Showing Some Constraint
A strong design constraint strategy carefully balances a wide range of electrical and manufacturing trade-offs. This month, we explore the key requirements, common challenges, and best practices behind building an effective constraint strategy.
All About That Route
Most designers favor manual routing, but today's interactive autorouters may be changing designers' minds by allowing users more direct control. In this issue, our expert contributors discuss a variety of manual and autorouting strategies.
- Articles
- Columns
- Links
- Media kit
||| MENU - design007 Magazine
Estimated reading time: 6 minutes
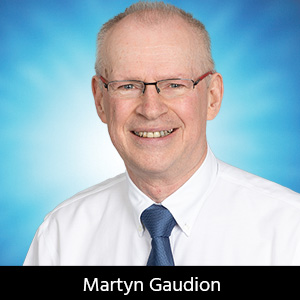
The Pulse: Using Touchstone Files to Build Measurement Confidence
Measuring PCB insertion loss can be time consuming(when compared with impedance testing), and the probes and cables tend to be significantly more costly (and delicate) than those used for characteristic impedance measurement. Nonetheless, given the high capital investment required for test systems, cables, and probes—and the design of the test vehicles themselves—wouldn’t it be nice if you could have a way of looking at your expected results before you put a test probe to a PCB?
I am not talking about simply simulating the result, rather recreating the raw files that can be used to drive the insertion loss test software and feeding the test software with data “as if” it was idealised measurement data.
Wouldn’t it be handy if you could prepare simulated raw files “as if” from a VNA to feed into your de-embedding software to ensure that it processes and the results from the test software are what you expect?
If you have followed this column for some time, you will recall the advice on measurement I have shared before, courtesy of Eric Bogatin:
“To make a good RF measurement, you need some engineering intuition to get a gut feel for what the measurement should be, and you also should model the expected results with a field solver before making the measurement itself.”
My column proposes an extra step made possible using Touchstone files.
Touchstone files are an industry standard ASCII file used across the EDA community for the recording and sharing of network parameter data, such as s-parameters (and more). They are the common output of vector network analysers, and of simulation tools. Originated by EEs in 1984, the file format has lived through a variety of owners and is now under the umbrella of Keysight Technologies. The files themselves have become a de-facto industry standard with their simplicity and lack of variation leading to very widespread usage.
Most fabricators are familiar with impedance measurement and can possibly make impedance measurements with their hands behind their back and their eyes closed. For insertion loss measurements, the list of who can do that is arguably much smaller. One of the reasons is the process of modeling and measurement is inherently more complex, even with attendant software to help, so a non-SI specialist in the fab industry needs all the confidence tools available to have trust in a measurement.
Let’s look at the process difference from modeled to measured. First for impedance:
- Model expected Zo result by entering trace geometry and base material characteristics with a field solver.
- Create suitable test vehicle, typically a four- to six-inch coupon with via connection at each end. The via characteristics are not super critical.
- Test the coupon trace with a suitable TDR or impedance test system.
- Compare 1 with 3. Provided you made what you thought you made, you will have a reasonable chance of good correlation.
Now to the process for insertion loss. The principle is the same but because of the much higher (and lower) frequency content there are some extra steps which can lead to disappointment if you don’t plan.
- Model the expected insertion loss by entering trace geometry, coupon length, and add in loss tangent and appropriate surface roughness to the characteristics.
- Create a suitable test vehicle, typically a pair of differential traces with identical cross-section but one pair shorter than the other; five-inch and 10-inch traces are not uncommon. Most ultra-high-speed architectures are differential, so a pair of differential traces is required. The vias and landing pads need to be specifically designed to an OEM specification or to the advice of the probe manufacturer you choose. Via design is much more critical than with impedance.
- Measure the s-parameters of the two traces over the desired frequency band.
- Post process the s-parameter pair data. Most methods require the test data to be processed by mathematically removing any residual via effects by looking at the difference between the long and short line. This is a complex process: One algorithm for this is Delta-L 4.0, but many other methods exist.
- The post processing software will give you the dB loss per unit length of the trace under test which you can compare with my first point.
What Could Go Wrong?
Quite a lot actually. The VNA operator needs to ensure that the VNA is calibrated to the particular cable setup (and possibly the probe as well). Though Delta-L 4.0 does a pretty good job of removing probe effects, there is still a multi-step process to initially calibrate the VNA before measurement starts with a given setup. The probes deployed are precision RF measurement probes, and either need placing with a probe station, or need to have the coupon design tooled with location holes to ensure the operator is not at risk of misaligning. Also, the differential probes need to be connected to both ends of the short line and gather one set of s-parameters and both ends of the long line. Contrast this with a differential impedance measurement which requires a precalibrated TDR and one differential probe. There are far fewer steps.
I often get asked why a measurement isn’t as expected; without being physically present, even via a weblink, that’s a tough call. What can be done to rule out as many things as possible and build confidence in the complete system? Interestingly, as soon as the user is confident that the system is okay then good measurements become simpler to achieve.
This is where the Touchstone files come in handy. Simply by exporting a pair of 4 port .s4p Touchstone files for the coupon under test from the modeling software, these two files can be fed to the long line/short line post-processing software. With Polar Atlas you can set the input to the Delta-L to be Touchstone rather than the VNA. This simple step allows you to send idealised results for the two coupons direct into the test software. Post-process the results and verify that with “ideal” data the long line/short line post processing works as expected. Once that is proven, the operator can go back, recalibrate the VNA cable setup, and make the measurement again with increased confidence of a quality result.
What kind of situations can this help with? A first time or inexperienced VNA user can be faced with a variety of unfamiliar situations during insertion loss measurement: The VNA needs to be correctly warmed up and stabilised, a calibration procedure needs to be run once the cables are connected with the appropriate artefacts, and care must be taken for all the ports to be connected in the correct order to the correct artefact. With practice, “muscle memory” makes this process easy but first-time users need to take care, and it’s best to do this in a quiet situation without interruption.
Connectors all need to be torqued to the specified level, and whilst this is recommended on TDR measurements, in practice you can get away with manual connections on a TDR. With a VNA, the need to torque connectors is far more critical. Simple errors, like connecting the VNA probes to the short line when you should be probing the long line, are easy to fall into. The ability to dry run the measurement with accurate simulated s-parameters removes a level of doubt and raises an operator’s confidence that good measurements are possible and, indeed, with practice are repeatable and normal.
In conclusion, the ability to insert trusted s-parameter transmission line data directly into the insertion loss processing software in place of raw measurement data raises operator trust in the system when using with “real” data from a VNA.
This column originally appeared in the April 2022 issue of Design007 Magazine.
See this additional content from Polar:
More Columns from The Pulse
The Pulse: Design Constraints for the Next GenerationThe Pulse: Ultra Upgrade Unknowns—What’s Coming for UHDI?
The Pulse: Commonsense Cost Cutting
The Pulse: Overconstraining: Short, Slim, and Smooth
The Pulse: Drilling Down on Documentation
The Pulse: New Designer’s (Partial) Guide to Fabrication
The Pulse: Simplest Stackups Specified
The Pulse: Rough Roughness Reasoning