-
- News
- Books
Featured Books
- pcb007 Magazine
Latest Issues
Current IssueThe Hole Truth: Via Integrity in an HDI World
From the drilled hole to registration across multiple sequential lamination cycles, to the quality of your copper plating, via reliability in an HDI world is becoming an ever-greater challenge. This month we look at “The Hole Truth,” from creating the “perfect” via to how you can assure via quality and reliability, the first time, every time.
In Pursuit of Perfection: Defect Reduction
For bare PCB board fabrication, defect reduction is a critical aspect of a company's bottom line profitability. In this issue, we examine how imaging, etching, and plating processes can provide information and insight into reducing defects and increasing yields.
Voices of the Industry
We take the pulse of the PCB industry by sharing insights from leading fabricators and suppliers in this month's issue. We've gathered their thoughts on the new U.S. administration, spending, the war in Ukraine, and their most pressing needs. It’s an eye-opening and enlightening look behind the curtain.
- Articles
- Columns
- Links
- Media kit
||| MENU - pcb007 Magazine
Estimated reading time: 5 minutes
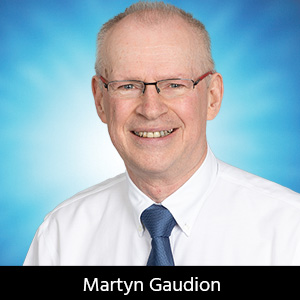
The Pulse: Fitting Physics to Fact
Driving down cost has always been the goal of modern engineering. The phenomenal reduction in manufacturing cost we’ve enjoyed over the past 50 years is primarily the outcome of engineers whose goal it is to make a good, affordable product. Economic cost-effective production benefits us all, including consumers, defense, aerospace, and automotive sectors.
Composites
Composite materials are incredibly versatile; they blend the characteristics of the component parts and are engineered to result in a product with the benefits of both the composite parts with few of the disadvantages of the individual constituents. In our PCB world, the use of composites gives access to PCB substrates with as many or as few layers as desired and with a wide variety of flavors, from low cost to high reliability and high speed, whilst at the same time juggling the safety and regulatory challenges of the available fire-retardant properties.
Statistics
At a large scale, many of the variations of composite materials, from an electrical perspective, are small enough to be dismissed, but with feature dimensions and interconnect geometries shrinking, it’s important to be aware of the inherent variation of the electrical properties of the substrate. These have been dealt with in much detail by the many authors of this column. However, the result for designers of inherent electrical differences distributed in the substrate is that as a designer you must look at the statistical effect on your design. How much variation is there and how much is that likely to affect prop delay, impedance, or insertion loss over a typical production run?
Monte Carlo Gives a Reality Check
It is easy to focus on one parameter and how that will impact the desired electrical characteristic, however, a far better approach is to set a tolerance for each primary dimension which may impact the circuit, then run a Monte Carlo analysis. This allows you to simulate a production run. I have used characteristic impedance of a 93-ohm differential pair in this example, but the Monte Carlo holds true for any characteristic which is impacted by a number of factors. In this example (Figure 1), I set each raw material dimension a 10% tolerance, and then simulated building 250 PCB transmission lines with a normally distributed, randomly selected set of parameters. This gives a far better impression of how production will vary over a batch of boards rather than simply focusing on one or two characteristic dimensions or looking at the worst case. It does allow you to experiment with which a particular dimension should be more tightly controlled to achieve a higher yield.
Figure 1 demonstrates that with a 10% tolerance on every characteristic over a production run, the majority of impedance results will fall well within 5-6%, but there will be outliers just out of the 10%.
In Figure 2 you can see that in this simulation the tightening of the trace separation specs significantly tightened the distribution with a significant peak on the nominal.
In Figure 3, purely for illustration, I pushed the dielectric constant tolerance out to an exaggerated ±20% and the more benign effects of Er, having only a 1 square root effect, show a minimal flattening when compared with the 10% illustration in Figure 1. These three illustrations demonstrate how a signal integrity engineer needs to balance the material properties of a base material with varying constituent properties and use statistics to see whether there is the potential for good yields based on the simulation. Making a good yielding design from materials which have inherent variability is one of the key areas where a design or SI engineer can add value to the production process and ensure a product is either profitable—if commercial—or within budget for contractual purposes.
When the Going Gets Rough
In the first part of this column, I looked at how an understanding of statistics helps maximise yields when working with composite materials. But copper is not a composite; it is a “pure” element. However, in high frequency designs the signal largely moves to the surface of the copper, and here it engages with the surface finish. For boards to be useful they must bond and survive assembly, possibly some rework, and then the environment that they will be used in.
This means that the copper must bond sufficiently to the epoxy in the prepreg to ensure that the board does not delaminate during either assembly or its working life. If you are using Gigabit speeds, then you will know that the roughness impacts insertion loss. The complex nature of electroplated surfaces means that it is far from practical to field solve the EM fields and associated losses at the surface, so empirical models are used to make predictions of loss owing to skin effect which are “good enough” for the SI engineer to work with when considering the loss budget.
Chemistry suppliers are gradually improving the pre-treatments in use to permit the use of ever smoother copper, which is easing this modelling situation, but most designs need to take care of roughness modelling. Designers new to the subject may think that they can obtain all the roughness data they need from a datasheet. However, more seasoned professionals will know that, depending on the stackup and the drill arrangements, only some of the surfaces are as in the datasheet; some will be pre-treated for bonding, and others will be plated as part of the plated through-hole process. This adds a layer of electrodeposited copper on the foil or core material and awareness of the stackup and the PCB fabrication process. It also adds the knowledge that maybe one fabricator prefers one approach over another and that for good modelling the SI engineer needs an understanding of both the specified materials and the stackup, as well as the approach of the fabricator. It’s not as simple as sitting in a darkened room studying datasheets.
Conclusion
Good use of modelling tools, a knowledge of PCB fabrication, and, even better, a close relationship with your fabricator perhaps will help you answer why “the laws of physics” don’t always seem to apply. The fact is that they do, but the materials we use and the geometries that are used mean that SI engineers, PCB designers, and PCB technologists need to know how material composition and interaction with the PCB fabrication process will impact a successful design. With careful use of simulation, your chances of a high yielding reliable design are increased whilst at the same time reducing your need for repeated prototype builds.
This column originally appeared in the November 2022 issue of Design007 Magazine.
Additional content from Polar:
- The Printed Circuit Designer’s Guide to… Secrets of High-Speed PCBs, Part 1 by Martyn Gaudion
- The Printed Circuit Designer’s Guide to… Secrets of High-Speed PCBs, Part 2 by Martyn Gaudion
- You can also view other titles in our full I-007eBooks library.
More Columns from The Pulse
The Pulse: Ultra Upgrade Unknowns—What’s Coming for UHDI?The Pulse: Commonsense Cost Cutting
The Pulse: Overconstraining: Short, Slim, and Smooth
The Pulse: Drilling Down on Documentation
The Pulse: New Designer’s (Partial) Guide to Fabrication
The Pulse: Simplest Stackups Specified
The Pulse: Rough Roughness Reasoning
The Pulse: Industry Organizations Keep Knowledge Alive