-
- News
- Books
Featured Books
- design007 Magazine
Latest Issues
Current IssueRules of Thumb
This month, we delve into rules of thumb—which ones work, which ones should be avoided. Rules of thumb are everywhere, but there may be hundreds of rules of thumb for PCB design. How do we separate the wheat from the chaff, so to speak?
Partial HDI
Our expert contributors provide a complete, detailed view of partial HDI this month. Most experienced PCB designers can start using this approach right away, but you need to know these tips, tricks and techniques first.
Silicon to Systems: From Soup to Nuts
This month, we asked our expert contributors to weigh in on silicon to systems—what it means to PCB designers and design engineers, EDA companies, and the rest of the PCB supply chain... from soup to nuts.
- Articles
- Columns
Search Console
- Links
- Media kit
||| MENU - design007 Magazine
Estimated reading time: 4 minutes
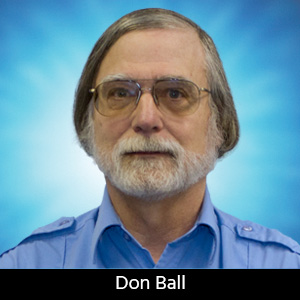
The Chemical Connection: Reducing Etch System Water Usage, Part 1
Water conservation has become an important component of the overall system design for most manufacturing operations today. Changing climate conditions and increasing populations are beginning to strain the freshwater supplies in many areas of the country. As a result, as equipment suppliers, we see an increasing number of requests for options that reduce water usage in proposed wet processing systems. Etching systems tend to use more water because of the need for close temperature control to maintain steady etch rates and the rinsing requirements for complete removal of corrosive etchants from the surface of the product before the next process step. This column contains some simple suggestions for reducing water usage in etch systems that won’t strain the budget too much.
Cooling Water
One large source of water usage in the etch system is cooling water to maintain the etchant temperature. Most cooling coils are made of titanium because of the corrosive nature of the etchant. Titanium is not the most efficient metal for heat transfer, so it is common practice to hook up a water feed to the cooling coil and run it wide open.
Checking the cooling water temperatures at the entrance and exit of the cooling coil under these conditions will usually show no temperature change. This is good if the etchant temperature is steady since it means the full length of the coil is being used efficiently. However, it may not be necessary to run the water at full flow. You should put a valve on the cooling coil input and slowly reduce the water flow until the difference in the temperature (ΔT) of the cooling water at the output is a degree or two higher than the input temperature while running the etcher at peak loading. This will reduce the amount of water used to the minimum needed to maintain the etchant temperature and cooling coil efficiency. (Believe it or not, higher ΔTs will decrease the efficiency of the cooling coil.) Depending on cooling coil design and plant water pressure, this simple step can cut cooling coil water usage by as much as 25%.
The ultimate reduction in cooling water use would be the addition of a chiller to the cooling water line. This is a well-established technology that chills the water to well below ambient, thus increasing cooling coil efficiency. It then removes the heat from the water from the output of the cooling coil and returns it to the system. In this way, the water usage for cooling is reduced to nearly zero. Note that there is no such thing as a completely closed water cycling loop.
Since the typical flow rate of cooling water in an etcher is four to five gallons per minute or more, you can see that this is a significant savings. The number of hours your etcher runs per day, along with the cost of water in your area, will quickly tell you if this investment is cost-effective for you. Also, keep in mind that the chillers can be used on other cooling water lines besides the etcher.
In 2000, for example, our injection molding equipment used 3 million gallons of cooling water for the year. In 2001, we added two chillers to the injection mold cooling water lines. In 2023, our water usage for injection molding shop cooling water was 96,000 gallons even though we have added a couple of injection molding lines over the years to keep up with increasing production.
Rinses
The other main consumer of water in the etching line are the rinses. When I first started in this business in the early 1970s, it was common to feed the spray rinses with fresh water and discharge it directly to the drain. Of course, this is not an acceptable practice today. The first effort at reducing water usage was to use lower flow rate nozzles when it was realized huge amounts of water weren’t needed to rinse the boards if the water was sprayed under pressure. If you can believe it, double-sided boards with 0.010" (250 µm) spaces were considered state-of-the-art. That solution didn’t last very long before more water savings were demanded. Retrofitting existing equipment is harder since reducing water flow usually means adding modules to the etch line, which isn’t always straightforward and easy. New lines, however, could be designed with built-in water-saving features.
A relatively easy retrofit was to add a sump under the flow-through rinse and feed fresh water into only the last spray tube while recirculating the water through the rest of the spray tubes and overflowing to the drain or in-house waste treatment system. This has the advantage of more efficient use of the water, reduced flow to waste treatment, and the last thing the panel sees as it exits the rinse is fresh rinse water. Depending on the number of spray tubes in the rinse water, usage can be reduced by as much as 50–75%.
In my next column, I will cover cascade rinses, flood rinses, and ways to reduce etcher water consumption to almost zero. See you then.
This column originally appeared in the March 2024 issue of PCB007 Magazine.
More Columns from The Chemical Connection
The Chemical Connection: Troubleshooting PCB Process ProblemsThe Chemical Connection: How We Deal With a Technology Roadmap
The Chemical Connection: Chemical and Equipment Control of High-density Circuits, Part 2
The Chemical Connection: Controlling an Alkaline Etch Bath With Low Copper Loading
The Chemical Connection: Chemical and Equipment Control of High-density Circuits
The Chemical Connection: Can the Limits of Subtractive Etching Be Extended?
The Chemical Connection: Reducing Etch System Water Usage, Part 2
The Chemical Connection: An Exhibitor’s View of IPC APEX EXPO