-
- News
- Books
Featured Books
- design007 Magazine
Latest Issues
Current IssueProper Floor Planning
Floor planning decisions can make or break performance, manufacturability, and timelines. This month’s contributors weigh in with their best practices for proper floor planning and specific strategies to get it right.
Showing Some Constraint
A strong design constraint strategy carefully balances a wide range of electrical and manufacturing trade-offs. This month, we explore the key requirements, common challenges, and best practices behind building an effective constraint strategy.
All About That Route
Most designers favor manual routing, but today's interactive autorouters may be changing designers' minds by allowing users more direct control. In this issue, our expert contributors discuss a variety of manual and autorouting strategies.
- Articles
- Columns
- Links
- Media kit
||| MENU - design007 Magazine
Estimated reading time: 3 minutes
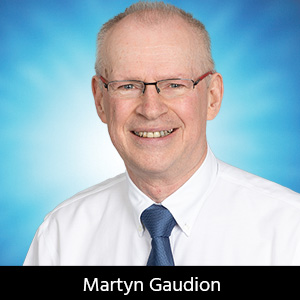
The Pulse: Ultra Upgrade Unknowns—What’s Coming for UHDI?
As we enter the second quarter of the 21st century, there appears to be a new chapter in PCB technology. Ultra high density interconnect (UHDI) has become a buzzword, but it’s actually not that new; many of the processes were already established in the high-volume production of Asian cell phones and tablets. What is new and challenging, however, is migrating the line widths and stackups—once the domain of handheld consumer products—into the lower volume specialized environment of the commercial world.
In the high-volume world, the quantities mean that prototyping and fine-tuning are more economical, given that unit production volumes will be in the hundreds of thousands or millions. Low- and medium-volume manufacture is more complex as the economics mean that prototyping can be expensive. Trace widths have languished between 50–75 microns for several years, but the drip of progress is pushing into the 10–40-micron arena.
New Chemistries, New Processes
Modified semi-additive process (mSAP) and semi-additive process (SAP) are emerging with some leading-edge PCB fabricators. Once reserved for organic substrate interposers (as a lower-cost alternative to silicon interposers), these processes are now seen on specialist PCBs. Traces are vertical, and the copper foils are thin to match the shrink-down in trace widths.
Modeling and Measurement
The downward shift in geometries means there will be increased impacts of trace resistance, but it is also time to take a fresh look at inductance, as this, too, is affected as trace separations come down. Additionally, because materials are thin, we may need to look at the impact of inductance as we model narrower plane separations. These are areas for future writing. For now—as has happened with previous downward shifts in geometries—additional factors that people previously ignored come into play. For example, it’s now possible for the copper trace to be embedded in the PCB’s surface layer rather than sitting on the top layer of prepreg. This allows for ultra-flat surfaces and facilitates the attachment of active devices.
UHDI: Two Tracks, Two Levels of Investment
UHDI is a generic term for PCBs with line widths under 75 microns. There are two main branches. The first is from 75 to 25 microns, which is expensive but reasonably viable for PCB fabricators to invest in. This still uses conventional (albeit very thin) glass-reinforced prepregs and slightly modified chemistry and equipment. However, step below 25 microns, and UHDI enters a different world. It requires specialized machinery, new factories with cleanroom capability, and a host of new chemical processes. The clue to when someone is discussing sub-25 micron is the use of build-up films. People often use the term ABF® to refer to Ajinomoto Build-up Film, as Japan’s Ajinomoto effectively dominates the market for the thin, unreinforced film used in building sub-25-micron PCB traces.
Ajinomoto developed ABF as a side product related to the production of umami seasoning in the food industry. ABF is a film-type insulator developed with amino acid technology. I find it fascinating to dig into the roots of innovation and how creative products sometimes cross unrelated industries.
Adaptation: Taking up This Technology
In the U.S., this technology is primarily being deployed in facilities with government support to buffer the significant investment in plants and systems. Time will tell if the initial capability becomes more widespread as the industry and supply chain find innovative ways to reduce the adoption costs.
What’s Next?
It will be exciting to see whether this technology becomes mainstream. The challenge for suppliers of equipment and measuring and modeling tools will be to discover whether working at these smaller geometries on conventional materials will expose us to physical effects that, until now, we have been able to sweep aside.
Martyn Gaudion is managing director of Polar Instruments Ltd. To read past columns, click here. Martyn is the author of The Printed Circuit Designer’s Guide to… Secrets of High-Speed PCBs, Parts 1 and 2.
This column originally appeared in the January 2025 issue of Design007 Magazine.
More Columns from The Pulse
The Pulse: Design Constraints for the Next GenerationThe Pulse: Commonsense Cost Cutting
The Pulse: Overconstraining: Short, Slim, and Smooth
The Pulse: Drilling Down on Documentation
The Pulse: New Designer’s (Partial) Guide to Fabrication
The Pulse: Simplest Stackups Specified
The Pulse: Rough Roughness Reasoning
The Pulse: Industry Organizations Keep Knowledge Alive