-
- News
- Books
Featured Books
- pcb007 Magazine
Latest Issues
Current IssueInventing the Future with SEL
Two years after launching its state-of-the-art PCB facility, SEL shares lessons in vision, execution, and innovation, plus insights from industry icons and technology leaders shaping the future of PCB fabrication.
Sales: From Pitch to PO
From the first cold call to finally receiving that first purchase order, the July PCB007 Magazine breaks down some critical parts of the sales stack. To up your sales game, read on!
The Hole Truth: Via Integrity in an HDI World
From the drilled hole to registration across multiple sequential lamination cycles, to the quality of your copper plating, via reliability in an HDI world is becoming an ever-greater challenge. This month we look at “The Hole Truth,” from creating the “perfect” via to how you can assure via quality and reliability, the first time, every time.
- Articles
- Columns
- Links
- Media kit
||| MENU - pcb007 Magazine
Estimated reading time: 19 minutes
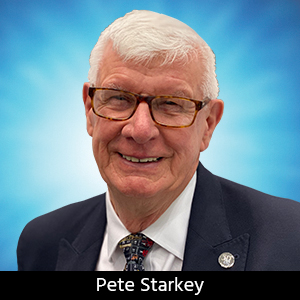
Contact Columnist Form
Europe Update: The 2008 EIPC Summer Conference in Dresden, Germany
Sitting majestically astride the River Elbe in the east of Germany is the beautiful city of Dresden, historically the capital of Saxony, now a center of excellence for microelectronics, information and communication technology, an appropriate venue for the European Institute of Printed Circuits 2008 Summer Conference.
Tourists take in the sights of Dresden, Germany. (Photo courtesy of In his opening address, EIPC Chairman, Rex Rozario, announced that both EIPC and his own company, Graphic plc, would be celebrating their 40th anniversaries during 2008, and reflected upon the many changes that had taken place during those four decades. External circumstances continued to affect the fortunes of the European PCB manufacturing industry, and the increasing strength of the Euro was a current concern. However, on a brighter note, 5.6% growth had been forecast for the coming year. Rozario acknowledged the support of the delegates and sponsoring companies and declared the commitment of EIPC to continue to seek ways of working with other associations world-wide to secure the future of the industry.
EIPC Chairman, Rex Rozario, delivers the opening address. (Photo courtesy of Global EMS was a mixed picture; many of the big companies were getting bigger, while some smaller companies were disappearing. World output of PCBs in 2007 was 50 billion USD, with Europe accounting for 8% and U.S. representing 9%. Walt advised some caution in interpreting trends indexed in US dollars because of distortions due to the continuing weakness of the currency. Having said this, Germany represented 36% of the European figure, with automotive, industrial controls and mobile phones being the core business. Some automotive PCB work was being withdrawn back to Europe from China because of quality concerns. PCB materials, and anything else with a petrochemical content, would inevitably cost more--Dow announced that they would raise resin prices by 20% in June. In addition, tin, copper, gold and silver prices continue to increase.
Walt's world PCB model forecast that 2008 would represent a low point in the business cycle, and very little growth was expected, although the Asian share would continue to increase. He predicted that, provided the industry could survive 2008, 2009 should be a recovery year.
Hans Freidrichkeit presented, "Less choice - the impact of a shrinking number of PCB manufacturers to European OEMs." Against a background of the growth of China's GDP, such that it now had the world's third largest economy, and the fact that, over the last twenty years, Japan's share of world PCB production had only fallen from 29% to 23%, whereas over the same time period Europe's share had slumped from 25% to 6%, Freidrichkeit posed the question, "What is Japan's secret?"
The answer began to emerge when he focused not on the overall PCB market, but on the technology sector, where Japan is number one both in microvia, with 37%, and in flex, with 28%. The differentiators were that Japanese OEMs value their PCB suppliers as an integral part of their own team; that the Japanese electronics industry has concentrated on highly sophisticated products which need highly innovative PCB suppliers; and that the concentration on innovative technologies leads to high growth rates and presents major obstacles to would-be new entrants into the market.
Europe presently has less than 200 PCB manufacturers left with turnover greater than 2 million Euro--less than half the number of ten years ago. The number of "small" companies, with 2 to 10 million Euro turnover, decreased by 20% over the same period, to a current estimated total of 143. "Medium" companies, with 10 to 50 million Euro turnover, decreased by 40% to an estimated 53, although the decline now appears to have levelled out. From the PCB buyer's point of view, the result was less choice of suppliers, less choice for technologies such as HDI, flex and flex-rigid and difficulty in finding a good source--very few choices and very few alternatives.
Referring to the apparent cost benefits of buying-in PCBs from China, Freidrichkeit used the "priceberg" analogy to demonstrate that lowest unit price is rarely reflective of total landed cost, with a major proportion of real cost lying below the waterline in areas such as lead times, missed sales, service levels, currency risks, inventory costs and quality costs. Additionally, there could be "country risks," examples being the knock-on from the Chinese earthquake and the restriction on power station operation to reduce pollution levels ready for the Beijing Olympics. The decline in prices was not primarily driven by pressure from buyers--it mainly resulted from cut-throat competition between manufacturers desperate to fill under-utilised capacity.
Conference attendees listen intently to a presentation. (Photo courtesy of http://cordis.europa.eu/, and how to structure a basic project proposal.
The first technical presentation was by Dr. Bart Degroote, a patent examiner at the European Patent Office in the Netherlands, who gave an intellectual property perspective on the way in which a patent application is examined, taking as his theoretical example the recently announced Occam process for solder-free electronics assembly. Dr. Degroote made it clear that his responsibility was as an examiner, not as an engineer, and that he was obliged to interpret and apply, meticulously and from a position of neutrality, the rules of the European Patent Convention, particularly in respect of the clarity of the claim under Article 84, and whether the concept could be considered prior art under Article 54. In the Occam example, based on the concept of "packaging a package" by embedding components in a substrate and then building the interconnect in situ, a prior-art study revealed two instances where comparable ideas had been described, both in 2003: Nathan and Shephard had made a patent application for a concept titled "Integrated assembly protocol," and a short while later Imbera had published one entitled, "Method for embedding a component in a base and forming a contact." There were many similarities with the principles of the Occam process and some grey areas, for example the conundrum of whether a chip-scale package could be defined as a bare die or as a package within the definitions of the individual claims.
Markus Karpach, from Fela Leiterplattentechnik in Germany, discussed survival strategies for European PCB manufacturers to secure a future in a declining industry. Fela had chosen to diversify into niche markets. Having listed the characteristics of an ideal niche, which included fast entrance in known and existing markets, low or no competition, USPs, low investment, use of existing production facilities and operator skills, Karpach described an innovative technology named Felam Glasline, a means of incorporating capacitative electronics directly on to the reverse side of glass panels, with many applications in medical and laboratory instrumentation and building controls--front panels, switches, access terminals, vandal-proof keypads and entrance controls for example. The product was elegant, durable and hygienic, and could be personalized and manufactured from lot-size 1. Fela had developed all of their own processing machinery and operated their own glass factory so that they had control of the whole value chain. They were presently building a network of partners in Europe--an interesting business perspective for other PCB manufacturers.
Pierre Emmanuel Goutorbe, from CIRE Group in France, described PCB technologies developed under a European project named EURIPIDES, in which CIREP were co-operating with six partner companies in Germany, Switzerland and Spain, to achieve EMC compliance in high-density avionics applications. The standard multilayer board was no longer adequate to satisfy the requirement, length and geometry of conductors was becoming increasingly critical and to decrease weight and size, as well as increasing product quality and decreasing assembly cost, it had become necessary to move decoupling capacitors into the structure of the board. A series of technology demonstrators had been constructed, incorporating fine-pitch PBGA geometries, up to four SBU layers, embedded decoupling capacitors, laser drilled PTH and filled copper microvias and an EMC tool had been developed for modelling impedance. Further work included the building of a series of functional avionics demonstrators in three alternative constructions, based on the same electronic schematic, to facilitate dynamic measurement and comparison of EMC characteristics.
Dr. Giordano Di Gregorio, from Somacis in Italy, discussed the selection of optical materials and the effects of manufacturing tolerances on coupling effects in PCBs with buried optical interconnects. Multimode waveguides had been fabricated by photolithographic patterning of proprietary epoxy materials, and electromagnetic modelling and experimental testing had been used to measure optical confinement, attenuation, waveguide dispersion and near-field distribution. The results demonstrated the importance of precise control of manufacturing parameters to avoid parasitic optical coupling effects, which could induce crosstalk between buried channels even when the dielectric guides were widely spaced. Variations in exposure time, UV curing and baking conditions could induce small changes in the refractive index of the waveguide material. The introduction of new geometries and compounds more compatible with the manufacturing process would reduce these effects without damaging the optical quality of the waveguides.
Nils Arendt, of Ormecon International in Germany, explained the chemical mechanism by which organic nanometal, when used as an active pre-dip for immersion tin, acted as a catalyst to prevent the oxidation of copper and modified the immersion tin exchange reaction to yield a very dense and homogeneous white tin deposit. Furthermore, the organic metal continued to act as a barrier which dramatically reduced the rate of diffusion of tin into copper and, when used in conjunction with an organic metal post-treatment, yielded a solderable finish which could survive multiple lead-free reflow operations at significantly reduced tin thicknesses--typically 0.4 microns compared with 1.2 microns for conventional immersion tin processes. An alternative organic metal finish incorporated a small proportion of silver and yielded a complex surface layer of silver, copper and organic metal, approximately 50 nanometres thick. This gave extremely high ageing resistance and good solderability after storage. Wetting force was almost double that of conventional OSP and solder joints showed no evidence of microvoids or black pad effects.
Mustafa Ozkok, from Atotech in Germany, reported the results of recent investigations comparing the solder joint reliability of electroless nickel-immersion gold, electroless nickel-electroless palladium and electroless nickel-electroless palladium-immersion gold finishes with respect to lead-free soldering with tin-silver-copper alloy. Samples of the three finishes were prepared with a range of thicknesses of nickel, gold and palladium components, using as a test vehicle a ball grid array pattern with solder-mask-defined pads. After ball attach, with or without additional reflow cycles, testing was carried out by high-speed ball shear and cold ball pull equipment. The nickel-palladium finishes out-performed nickel-gold on both ball-shear and ball-pull tests, and metallographic examination of solder joints revealed a direct correlation between joint failure and the extent of growth of (Cu,Ni) 6Sn5 intermetallic compound at the interface.
Jurgen Schmidt, from KIV ProfiChem in Germany, described a range of copper activation processes designed to be environmentally friendly and to give better uniformity and controllability than traditional sodium persulphate based chemistries. Different formulations were available for single-step degreasing and micro-etching of inner layer material, single-step cleaning and activation of inner layers prior to bonding and single-step pre-treatment prior to solder mask application. In each case, activation was achieved with minimal copper removal, and SEM photographs illustrated the fine-grain, uniform surface structure achieved. The system was automatically replenishable and could be installed safely in equipment with stainless steel or titanium components.
David Ormerod, from Enthone in Germany, discussed improvements in inner-layer bonding to meet the requirements of lead-free assembly applications. Delamination failures in advanced multilayer and sequential-build products, resulting from the conversion to lead-free soldering conditions, had driven the need for improved oxide-replacement technology. One limiting factor in older alternative-oxide chemistries was the tendency of the copper-oxide-organic complex to break down at excessive reflow temperatures and, although post-treatment could increase peel strength, peel strength had been found not to give a good indication of potential assembly-soldering failure. Based on statistically designed experiments, a process had been developed which delivered a more resilient copper conversion coating. This had shown improved bonding performance and greater stability at high temperatures, and was able to withstand multiple lead-free reflows at 270 degrees C and 280 degrees C.
John Maguire, of March Plasma Systems in the Netherlands, described equipment enhancements and performance improvements in vacuum gas plasma systems, designed to take into consideration gas distribution, flow direction, electrode design, exhaust diffusion and material temperature control--all critical factors in satisfying the demands of leading-edge technologies in PCB manufacturing, specifically in achieving maximum process uniformity without sacrificing etch rate. He reviewed advances in gas manifold and exhaust baffle configuration to create uniform gas flow, and in electrode design to achieve uniform gas ionisation. A new platform plasma tool had been developed based on data collected from initial experiments. Each of the changes was studied in detail by both weight loss and microsection of mechanically drilled through-holes, on materials and panel constructions representative of current state of the art. Electrode configuration, gas delivery, gas distribution and gas removal all affected uniformity and changes in each had a collective effect. Etch rate was closely dependent on temperature. Each material had a characteristic "etch window," which was related to glass transition temperature, and accurate temperature control was necessary to prevent under- or over-etching.
David Wayness, of Rohm and Haas in UK, reviewed forty years of the evolution of electroless copper plating processes, and how a whole range of different variations had resulted in response to the demands of different market and technology sectors. He made a well-reasoned argument in favor of a universal electroless copper process designed to meet the requirements of today's printed circuit designs and manufacturing complexities, and described how such a process package had been developed. Characteristics of materials and the mechanisms of solvent swelling and desmearing, catalysation and acceleration, and the electroless chemistry itself had all been studied in detail, and issues such as base dielectric adhesion promotion, and balancing coverage and adhesion, had been optimised using designed experimentation. The outcome was a process capable of low build or high build operation, in vertical or horizontal process lines, with the benefits of a 40 to 60% reduction in volume of chemistry consumed, faster start-up and improved bath stability, improved thermal cycle and solder shock performance and reliability gains over a wide range of base materials and designs.
Volker Klafki, from Technolam in Germany, opened the session on laminates with an update on second-generation halogen-free materials. Halogen-free was still not for free--there was a price premium because the resins were more expensive than their brominated equivalents. Misleading information continued to generate concerns about brominated flame retardants, and environmental groups like Greenpeace persisted in their efforts to pressure the industry to avoid the use of "dubious substances." The primary driving force toward halogen-free came from OEM activities in Japan, and although halogen-free laminates as yet represented only a small percentage of the world market, the share was growing rapidly--from 4.9% in 2006 to 6.8% in 2007. The limitations of first-generation halogen-free materials had been acknowledged, and products were now available with better peel strength and reduced brittleness. Improvements had been made in processability, but drill-bit wear remained a major issue although developments in filler technology would bring about some improvement. Tailor-made halogen-free materials were becoming available for specific purposes such as high speed and mobile phone applications, and it was predicted that halogen-free would progressively emerge as the total solution towards the green requirement.
Dr. Albert Angstenberger, from Taconic Germany, expounded the virtues of metal-back PTFE laminates for radio link and power amplifier applications, particularly at frequencies above 5GHz. He reviewed the benefits of RF and microwave linearity, grounding and thermal dissipation, and emphasised the mechanical and thermal reliability and ease of manufacture of PCBs fabricated from pre-bonded metal-back materials.
Dr. Veronique Steukers, from Albermarle Belgium, speaking on behalf of EBFRIP, the European Brominated Flame Retardant Industry Panel, asked the question, "Who can tell me what green means?" Not surprisingly, there was no rush of volunteers from the audience to offer a definition. Dr. Steukers suggested that those bodies who would condemn brominated flame retardants might take the trouble to understand the scientific facts about substances they targeted--properties, effects on human health, effects on the environment. Taking the example of tetra-bromo-bisphenol-A (TBBPA), present in 90% of FR4 boards, it was the only flame retardant for printed circuits to have undergone the rigorous scientific evaluation as would be required by REACH, and had been approved for unrestricted use in PCBs by the European authorities. She reviewed the final conclusions of the of the risk assessment for TBBPA, the risk management discussions and the transition to the impending REACH regulation. Dr. Steukers also discussed the product stewardship initiative VECAP, the Voluntary Emissions Control Action Program, which has set new standards on chemical management in the workplace and has been acknowledged by the authorities as a very good example of how the industry can work together through the supply chain.
Jerome De Boysere, from Clariant in Germany, gave an update on current legislation, trends and driving forces in the halogen-free laminate market and described the experiences of major EDM and EMS companies with halogen-free transitions. It was clear that the push toward halogen-free was coming from OEMs rather than from legislation. The question was not "if?" or "why?" but "how?" and "when?" and the transition was picking up momentum, with Asian countries the front-runners, and an increasing level of activity in the U.S. Several major programs were ongoing: the High Density Packaging User Group was producing halogen-free guidelines and a database, iNEMI were carrying out a technical assessment of halogen-free PCBs, and the U.S. EPA Flame Retardants in Printed Circuit Boards Partnership was assessing halogen-free alternatives.
Martyn Gaudion, of Polar Instruments in UK, described work that had been undertaken jointly with Intel to develop a PCB production-floor metric for go/no-go testing of lossy high-speed transmission lines. Root Impulse Energy (RIE) testing, using a conventional time domain reflectometer, had been evaluated as a straightforward alternative to complex Vector Network Analyser (VNA) methods. A simple coupon had been designed which enabled the reflection of a test line, 8" to 12" in length, to be compared with that of a short reference line. Stripline configurations had shown better material differentiation than microstrip, and RIE measurements had shown good correlation with VNA loss figures. Polar were presently working with National Physical Laboratory in London to establish a universal loss standard for worldwide cross-comparison and acceptance.
Dr. Agnes Chaillot, of EADS in France, reported the progress of a reliability study undertaken to gain a better understanding of factors influencing the robustness of HDI PCBs in an avionics environment. To determine the root cause and failure mechanism of defects, such as laminate cracks in structures featuring microvias, buried vias and plated through holes, a finite element modelling technique had been applied. The complete thermo-mechanical parametric model had been drawn of a representative bare board structure, to enable numerical stresses and strains to be calculated for different geometries and materials, at temperatures below and above glass transition, with the final objective of optimising design rules and material choice for tin-lead and lead-free assembly conditions. The FEM model was now available for other parametric studies, and work was proceeding in the further characterization of material properties, with a view to extending the program to include a study of the behaviour of assemblies, as well as bare boards, through reflow processes.
Tom Bresnan, from R&D Circuits in the U.S., gave an insight into the realities of manufacturing ATE boards used for package testing, as BGA pitches reduced to the 0.4 mm level and finer. These boards were typically large-format, thick, many-layered structures with fine, high-aspect-ratio holes (aspect ratios of 40 and more were increasingly encountered). R&D Circuits had overcome particular challenges in drilling registration and through-plating presented by these high-aspect-ratio holes, and could demonstrate their reliability by 100-cycle Interconnection Stress Testing. "Space transformers," increasingly used as interface adapters to translate the fine pitch pattern of the package under test to a pitch compatible with that of the ATE probe card, have traditionally been built using ceramic processing. R&D Circuits have developed the capability to build these space transformers with printed circuit board materials and techniques, realizing cost and time savings by allowing rapid tester-platform interchangeability.
Dr. Rita Chiodini, from UL's Conformity Assessment Department, explained how the constructional and performance requirements of UL796 were interpreted in the case of printed wiring boards with plugged holes, and multilayer boards based on pre-fabricated mass-laminated cores. Regarding hole plugging, UL796 Section 14 concerned the possible effects of plugging materials compromising the flammability characteristics of the PWB, or interacting chemically with the solder mask. Only organic hole-plugging materials required to be tested. Regarding mass-laminated multilayers, Section 18 of UL796E permitted that, provided that the mass-laminate came from a UL-recognised supplier, the resulting multilayer could be considered as a "single-layer" board within the definition of UL796 for the purposes of UL submission. Dr. Chiodini demonstrated the ULIQ Web site, and how its search engine could be used to locate a recognized supplier of mass laminate of a particular specification.
Dr. Maria Nikolova, from MacDermid in the U.S.,explained how new developments in acid copper plating could enable the filling of blind microvias of multiple geometries while simultaneously plating through-holes on the same panel. The principle could be applied both to panel plating and to pattern plating processes. A range of customers' boards was shown as examples of real designs and customers' own reliability data was presented. A separate development had originated in response to problems of accelerated breakdown of organic additives consequent upon the trend to increasing PCB production in tropical climates. A new generation of additives had been introduced, which were tolerant of electrolyte temperatures up to 40 degrees C.
Lars-Eric Pribyl, from Atotech Germany, concluded the technical program with a presentation discussing solutions for highest-reliability PCB production to meet the demands of the automotive industry. The trend continued toward increasing electrification of the motor car, with electronics getting more and more into essential functions. The safety and reliability of the vehicle depended strongly upon the reliability of the electronics, which were required to function in increasingly harsh environments. The integrity of plated-through-hole interconnection to inner layers was considered the most critical feature influencing the reliability of the PCB, and Atotech had investigated which attributes of the plating-through-hole process had the greatest impact on the incidence of interconnection defects. The electroless copper bath itself was identified as having the most significant influence and, of its ingredients, the stabilizer was the key component. Various stabilizers had been evaluated, using severe solder-shock testing to induce interconnection failure, and one, whose composition was not discussed, was found to be associated with zero failures in customer tests. This new stabilizer had been incorporated into Atotech's latest generation of high-reliability electroless coppers.
As a forum for members of the industry to share information on business and market trends, technology and environmental legislation, this EIPC Conference was, as has come to be expected, a resounding success. Between conference sessions there was a buzz of activity, in the exhibition area, the restaurant and the bar, as delegates made the most of the opportunity to network with their peers and to visit the tabletop exhibits of the sponsoring companies. Many new lines of personal communication were established and the outstandingly positive spirit of the event clearly demonstrated the energy, enthusiasm and determination in the European PCB industry to build its strength to face the future.
More Columns from The European Angle
CircuitData: A New Open Standard for PCB Fab Data ExchangeI Never Realised It Was So Complicated!
The European Angle: Institute of Circuit Technology 43rd Annual Symposium
Ventec International Group's Martin Cotton Celebrates 50 Years in PCB Design
Reporting on the Institute of Circuit Technology Spring Seminar
EuroTech: Raw Materials Supply Chain—Critical Challenges Facing the PCB Industry
EuroTech: ENIPIG—Next Generation of PCB Surface Finish
EuroTech: Institute of Circuit Technology Northern Seminar 2016, Harrogate