-
- News
- Books
Featured Books
- pcb007 Magazine
Latest Issues
Current IssueInventing the Future with SEL
Two years after launching its state-of-the-art PCB facility, SEL shares lessons in vision, execution, and innovation, plus insights from industry icons and technology leaders shaping the future of PCB fabrication.
Sales: From Pitch to PO
From the first cold call to finally receiving that first purchase order, the July PCB007 Magazine breaks down some critical parts of the sales stack. To up your sales game, read on!
The Hole Truth: Via Integrity in an HDI World
From the drilled hole to registration across multiple sequential lamination cycles, to the quality of your copper plating, via reliability in an HDI world is becoming an ever-greater challenge. This month we look at “The Hole Truth,” from creating the “perfect” via to how you can assure via quality and reliability, the first time, every time.
- Articles
- Columns
- Links
- Media kit
||| MENU - pcb007 Magazine
Estimated reading time: 6 minutes
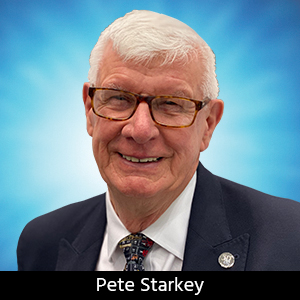
Contact Columnist Form
Inside the Orbotech European PCB Executive Forum
On Monday, June 23, 2008, Yoav Harel (pictured left), President of Orbotech SA, welcomed over forty senior members of the European PCB manufacturing industry to Orbotech's headquarters in Yavne, Israel to share with them the company's vision and future direction, and to introduce the latest developments in equipment and software.
Lior DePicciotto, Corporate Vice President for Business Development, gave a brief business update, with reminders that almost every electronic device in the world is built with the help of Orbotech systems, that of 1,600 employees world-wide, 400 are scientists involved in research and development, backed by an annual budget equivalent to 18% of Orbotech's total revenue, and that 90% of current sales are of products introduced during the last 24 months. From its beginnings 25 years ago in automated optical inspection of printed circuits, Orbotech has evolved in two dimensions--deeper into technologies related to PCB engineering, imaging, inspection, repair and process control and broader into applications in flat panel displays, PCB assembly, recognition solutions and medical imaging. The company continues to explore prospects in new markets, and are in a strong financial position to pursue merger and acquisition opportunities.
Hanan Gino, President of PCB Division, acknowledged the European PCB industry as early adopters of new technology. Their demanding requirements in high-tech, high-mix, low-volume production were well understood and supported by Orbotech, who continued to reinvest 15% of PCB Division's revenues in R&D. He recognized the slowdown in the global economy and commented that the strength of the Shekel against the dollar was of some concern, but he was confident there would be no repetition of the 2001 bubble in the electronics industry. Growth rate in 2008 would be less than 2007, but should still be positive at about 5%, with a recovery forecast for 2009.
After a series of product-specific presentations, from Micha Perlman on automated optical repair, Dubi Abraham on inkjet legend printing and Dr. Werner Eschke on new LDI features and models, a tour of the facility was conducted and guests were given the opportunity to see equipment at various stages of manufacture, with detailed explanations and live demonstrations.
Guests receive an up-close demonstration of Orbotech's LDI equipment. Of the new developments demonstrated, perhaps the most innovative was the PerFix(TM) Automated Optical Repair (AOR) System, an industry first. This technique offers a solution to the problem of removing copper shorts on fine-line layers without damage to conductor pattern or substrate, and combines Orbotech's expertise in optical image capture and analysis with controlled laser ablation. The PerFix unit receives its information either direct from AOI or from the verification station, locates the defect and removes it incrementally in a series of closed-loop ablate-copper/capture-image/analyse-image cycles until the superfluous metal has been completely eliminated.
An industry first, the PerFix(TM) Automated Optical Repair (AOR) System is inspected by forum attendees.Removing copper a thin layer at a time enables extremely precise control and ensures that damage to the laminate is kept to an absolute minimum; penetration of only 4 to 10 microns into the surface is typical. Each cycle takes about one second, and the entire repair process can be completed in ten seconds, restoring the conductor pattern to correspond exactly with CAM data, however inaccessible the feature may be to traditional repair techniques. Even complex multiple shorts can be removed within 20 to 40 seconds. A low-power laser sweep provides the final clean-up to de-smut the copper surface.
Clear leaders in laser direct imaging, with over 310 systems installed world-wide, Orbotech continue to advance their LDI capability. First revealed a few days earlier at the JPCA show, the Paragon(TM) Ultra 80 has been developed to enable manufacturers of BGA and CSP substrates to work at 40-micron pitch: 18-micron lines and 22-micron spaces in 25-micron photoresist, with edge roughness better than +/- 1 micron at 3 sigma. Completely new optics and electronics have been necessary to achieve this level of precision, and address resolution has been improved from 2.5 microns to 1 micron. In readiness for automation, a universal interface has been established so that the equipment can be operated stand-alone, in-line, or robotically.
A characteristic of Orbotech's Large Scan Optics is their extremely high depth-of-focus, minimizing surface topography effects. The Paragon Ultra 80 is capable of operation at exposure energies from 10 to 2,200 millijoules per sq cm. By using an 8-watt solid state laser; the system can expose 500 mm x 400 mm images at a throughput of 30 panels per hour. Registration accuracy of +/- 5 microns and side-to-side registration of 10 microns are routinely achieved. An additional feature is the facility to mark individual serial numbers, date and scale-factor stamps and bar codes.
Tour guests were able to closely investigate systems at Orbotech's facility.Since their acquisition of New System in 2007, Orbotech has directed substantial resources to the engineering of improved ink-jet printing machines, and are about to launch their new Sprint(TM)-8 legend printer to the open market. Two units have already been established in successful production operation--one in Germany and one in Italy. The Sprint-8 features new industrial inkjet heads with a total of 1,024 nozzles and a unique ink-management system giving very low ink consumption and zero waste. The advanced raster image processor is Orbotech's own design, as is the flexible and fully-programmable electronic control system and the user-friendly software. Resolution is selectable from 360 to 1440 dpi and at standard resolution of 720 x 720 dpi, print time for an 18" x 24" panel is 39 seconds, with a practical throughput of 52 panel-sides per hour.
One feature of Orbotech's technology that brings real benefits in throughput, handling and flexibility is the integration of UV curing with the printing operation. A high-energy collimated UV source is close-coupled behind the print-head so that as the head traverses the panel to generate the image, the ink is dried an instant after hitting the substrate. As a result, the panel can be handled immediately after printing the first side, and flipped if desired to enable the second side to be printed without delay. When printing double-sided on semi-cured solder mask, this means that only one, rather than three, oven curing operation is required. A combination of a new clamping system and automatic print-head height setting enables the Sprint-8 to overcome panel warpage problems, and its 1.5 mm depth-of-focus facilitates the printing of uneven surfaces such as those of flex-rigid designs. The machine can print legend characters as small as 0.5mm with 75 micron lines, and offers the capabilities of automatic label printing, individual image serialisation and custom bar-coding.
Elsewhere on the tour of Orbotech's immaculately-presented facility, visitors were able to see the new LP(TM)-9 laser plotter, which offers 30% higher throughput than the present top-of-the-range LP(TM) 9008 model, with resolution up to 50,000 dpi and 15 micron accuracy, the Paragon(TM) 8800 laser direct imaging system, and the Discovery(TM) OLB AOI machine with integrated verification bridge, intended for quick turnaround producers. Additionally, it was extremely interesting to be given the opportunity to take a privileged look at how Orbotech has applied AOI expertise to other sectors of the electronics industry. Particularly impressive are the large-format InVision(TM) and SuperVision(TM) systems for the inspection of flat panel displays.
With a perspective on software, Avi Glasberg, co-President of Frontline PCB Solutions, described the latest developments in Frontline's range of CAM and engineering products for automating the PCB pre-production process. Established in 1998, Frontline now has an installed base of over 6,000 CAM seats world-wide, backed by a team of over 120 people. The company is heavily committed to R&D with 45 software engineers--the largest team in the field. The Genesis 2000 CAM system continues to evolve, the latest release being Version 9.3, and its GenFlex(TM) derivative has become the favoured CAM for flex and flex-rigid manufacturing, with more than 200 seats in production. Enhancements to Frontline's widely-used InPlan(TM) pre-production engineering system and InPlanFlex(TM) engineering for flex and flex-rigid boards, now include automatic stack-up design InStack(TM), all with over 400 seats installed, and a new automatic impedance coupon generator module InCoupon(TM).
A group shot outside Orbotech's headquarters in Yavne, Israel. Not only did this Executive Forum serve to demonstrate the breadth and depth of the company and its products, it provided a remarkable opportunity for the leaders of the European PCB industry to meet and share their opinions and experiences in a relaxed environment. Many acquaintances were renewed and new friendships formed, and it is an acknowledgement of Orbotech's standing as a leading supplier that so many key people enthusiastically accepted the invitation to attend.
More Columns from The European Angle
CircuitData: A New Open Standard for PCB Fab Data ExchangeI Never Realised It Was So Complicated!
The European Angle: Institute of Circuit Technology 43rd Annual Symposium
Ventec International Group's Martin Cotton Celebrates 50 Years in PCB Design
Reporting on the Institute of Circuit Technology Spring Seminar
EuroTech: Raw Materials Supply Chain—Critical Challenges Facing the PCB Industry
EuroTech: ENIPIG—Next Generation of PCB Surface Finish
EuroTech: Institute of Circuit Technology Northern Seminar 2016, Harrogate