-
- News
- Books
Featured Books
- pcb007 Magazine
Latest Issues
Current IssueInventing the Future with SEL
Two years after launching its state-of-the-art PCB facility, SEL shares lessons in vision, execution, and innovation, plus insights from industry icons and technology leaders shaping the future of PCB fabrication.
Sales: From Pitch to PO
From the first cold call to finally receiving that first purchase order, the July PCB007 Magazine breaks down some critical parts of the sales stack. To up your sales game, read on!
The Hole Truth: Via Integrity in an HDI World
From the drilled hole to registration across multiple sequential lamination cycles, to the quality of your copper plating, via reliability in an HDI world is becoming an ever-greater challenge. This month we look at “The Hole Truth,” from creating the “perfect” via to how you can assure via quality and reliability, the first time, every time.
- Articles
- Columns
- Links
- Media kit
||| MENU - pcb007 Magazine
Estimated reading time: 18 minutes
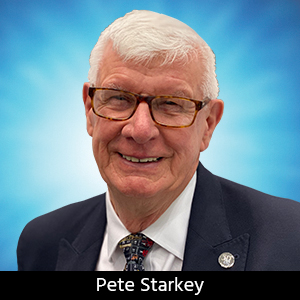
Contact Columnist Form
EIPC Winter Conference Review
With a thin layer of ice on its canals, and a bicycle for each of its three-quarters of a million inhabitants, Amsterdam, the financial and cultural capital of the Netherlands, was the venue for the EIPC Winter Conference. The comprehensive event took place February 12-13, 2009, offered 22 presentations and was remarkably well-attended with 13 countries represented.
EIPC Chairman Rex Rozario welcomed delegates and acknowledged their support at a time when the European PCB industry is facing an uncertain future: insolvency problems at major German manufacturers FUBA and Ruwel and the consequent effect on their material suppliers, massive layoffs and shutdowns in the EMS industry, many of the smaller PCB companies struggling to find work.
But, taking his own company Graphic PLC as example, Rozario offered some encouragement: Graphic had seen the early signs of recession back in 2007. Directors and managers had taken a pay cut, cost savings had been made wherever possible and all efforts had been made to improve yields. Prices had been maintained; the company was still profitable, with a full order book and was recruiting engineers.
Reflecting upon the combined effect of the shift of PCB production to Asia and the global collapse in confidence in the banking system, he believed that global output would take two years to recover, and employment four years. And no-one could predict at what point government recovery initiatives would begin to take effect. He introduced the keynote presentation with the question, "What are the challenges and risks of purchasing PCBs outside Europe?"
EIPC Technical Director Michael Weinhold set the scene for Ivan Ho, EIPC Director for Asian Pacific Activities, to discuss "China's PCB Industry: Friend or Foe? How to build partnership and to minimise risk and surprises," with statistics demonstrating how the Chinese contribution to the European PCB demand of around 5Bn Euro has grown from less than 10% in 2000 to more than 50% by 2007, remarking that EIPC has a responsibility to its members to make them aware of the opportunities and risks involved in trading with Chinese manufacturers, and to advise them how to build successful relationships to complement their value-added services to European customers.
Ho began by analysing the geographical, production and ownership data for the Chinese PCB industry over the last decade, and explained how it had matured from its opportunistic beginnings to a $14 billion business, although the short-term outlook is not good--soaring unemployment, extended holidays, pay cuts, reduced working hours. Ho predicted that China's economic recovery would probably be faster than in the Western world because of the prompt reaction of the Chinese government to inject liquidity, reduce interest rates, cut taxes and sponsor infrastructure projects.
Ho described the traditional mindset of Chinese entrepreneurs: opportunistic, willing to take risk with little regard for business models, dive in first then learn to swim and over-promise first and apologise later. But Ho said these attitudes are mellowing, and the Chinese have recognised the need to invest in talent, expertise and equipment to grow the business by getting into higher-value markets.
He advised European companies to leverage their own brand names, and to make the most of their customer relationships and technical knowledge, with the objective of offering a seamless, value-added local service to their customer base whilst using Chinese partnerships to fill the gaps. It was important for a company to understand its competition, to clearly identify where it wanted to position itself in the market, then seek the right partner to match its needs. Careful research was needed, followed by proper due diligence and the building of strong personal relationships with owners and top management.
As Ho explained, "Make friends first and business later. The Chinese are bonding people. Friendship is forever; business is there when you need it!"
The second presentation demonstrated how a European PCB manufacturer could adopt positive tactics and move forward, rather than retreat, in a time of recession. EIPC Vice Chairman Giacomo Angeloni described the Somacis "Strategy for Survival." He likened the current situation to the parable of the seven lean cows devouring the seven fat cows. The lean cows of the moment are global crisis, erosion of market share, failure to develop human resources, crippling European bureaucracy, quick profit takers and communication problems. What can be done to avoid them causing a catastrophic collapse of the European PCB industry?
Angeloni explored the challenges, and described how Somacis had set out to secure its future prosperity. Reductions in costs and lead times were priorities, together with innovative technology and value-added services. Somacis' new emphasis was on fast prototyping and production in the high-technology market, with substantial investment focused on the technical enhancement of their Castelfidardo factory and the establishment of a new 15 million Euro factory in Manfredonia with the capability to produce complex rigid boards and prototype chip packages on very short lead times. Investment continued in their Chinese operations with the objective of increasing their presence as a domestic supplier of medium-to-high technology PCBs, rather than producing at low cost for import into Europe. The company was exploring merger and acquisition opportunities in the U.S., particularly in Silicon Valley and the Boston area, as well as in Europe and possibly Japan.
Whatever economic problems the industry might have to worry about, there was no escape from health and environmental legislation. Johan Nouwen, leader of the guidance team of the European Chemicals Agency in Finland gave an update on the REACH (Registration, Evaluation and Authorisation of Chemicals) Regulations, and what challenges they presented to manufacturers of "articles." He explained that an article is an object which, during production, is given a special shape, surface or design that determines its function to a greater degree than its chemical composition, and that a company has the role of an article producer if it produces articles within the EU, regardless of how they are produced and where the articles are placed on the market.
An article importer is any company located inside the EU which imports articles from countries located outside the EU. An article supplier is a company which produces, imports or distributes articles and/or places them on the EU market. Nouwen went on to discuss the circumstances under which article producers and importers are obliged to register and notify substances, and their duties to communicate information along the supply chain, particularly regarding substances of very high concern. Guidance notes are available from the ECHA Web site.
The session on embedded components began with an analysis of potential markets by Hannes Stahr from AT&S in Austria. Opportunities have been recognised in mobile telecom, green energy, medical and safety-critical applications, with benefits of increased real estate for surface-mounted components, direct copper-to-copper interconnection, excellent RF properties and mechanical shock resistance. AT&S has been steadily developing technology for embedding discrete components over a 12-year period, and has met with some success and some frustration. Although they now have an established capability to embed more complex silicon devices, the barrier to industrialisation was not the technology, but nature of the supply chain.
With the PCB fabricator effectively becoming involved in the packaging business, there was concern about the management of and responsibility for silicon back-end processes and the transfer of know-how in component testing and applications.
In an effort to bring chip embedding to an industrial level, a European funded project was initiated with a consortium of industrial partners, under the name HERMES (High-density integration by Embedded chips for Reduced size Modules and Electronic Systems).
A partner in the HERMES project was Fraunhofer IZM in Germany, and Lars Boettcher described developments in pad pitch reduction of the embedded silicon, the resulting fine-pitch requirements for chip contact and the fine-line requirements for interconnection. Laser direct imaging and semi-additive techniques have enabled the patterning of lines and spaces down to 15 microns. Boettcher discussed the results of testing to demonstrate the reliability of the embedding technology, using QFN-type and BGA-type test vehicles.
Weinhold posed the question of whether this technology would bring packaging back to Europe. Hannes Stahr saw a possibility: To begin with simple components and be embedding modules within 10 years. Asked what would be the reaction of the assembler to the PCB fabricator taking away added value, Stahr believed that this was not a big problem. Boards would still need to be assembled, and if anything, the PCB fabricator would be saving the assembler the nuisance of handling small, low-value components, leaving the assembler to place higher-value surface-mounted devices. Testing, however, would remain a major issue and the fabricator would be responsible for supplying partially tested assemblies.
Dr. Konrad Wundt, EIPC executive director, introduced the session on progress in energy efficiency with an update on the EU-sponsored SurfEnergy project, whose goal was to achieve a stronger position for the PCB and surface finishing industries by efficient energy management. A detailed questionnaire had been developed for PCB production and energy statistics, which would enable participants to benchmark their processes with reference to similar PCB fabricators, against European and global averages and ranges.
Dieter Backhaus of MBT in Germany presented a new technology for multilayer pressing, aimed at reducing energy consumption and improving product quality through more uniform heat distribution, The Temperature Optimised Process (TOP) uses internally-heated press plates of three-ply stainless steel/aluminium/stainless steel construction and very thin separator plates of low-carbon steel. No press padding is needed, and the quick and even distribution of heat gave increased flexibility of production. As the target temperature was reached, energy input was reduced to maintain the temperature, and only 7KW of power was required for a load of 24 panels, with almost all of the heat created in the tooling going directly into the laminate. Energy savings of up to 90% were possible over conventional presses.
Nils Arendt of Enthone gave an update on applications of organic nano-metal conductive polymer as a versatile lead-free solderable finish, whether as a standalone or in combination with immersion tin. The organic nano-metal, a conductive polymer with metallic properties and primary particles of only 10 nanometres, acts both as a passivator for copper and as a catalyst for the controlled and homogeneous deposition of immersion tin. The most recently developed process variant gives a lead-free immersion tin of only 0.4 microns thickness, by the use of organic metal both as a pre-dip and a post-dip. The effects were to greatly reduce the diffusion rate of tin into copper, and hence the rate of intermetallic formation, and also to inhibit the oxidation both of copper and intermetallic such that wettability was maintained for three or four successive reflow cycles. This finish gave improved aging, soldering and signal transmission properties as compared with ENIG, a cost savings of approximately 30% and a process energy saving of up to 95%.
Randy O'Donnell of Kyocera-Tycom in the U.S. demonstrated how taking a scientific approach to drill re-sharpening could reduce drill-room costs. Using two approaches: Design of Experiment and Benchmark, Implement and Control, Kyocera-Tycom had been able to determine the combination of process settings and re-sharpening parameters which allowed significant cost savings without sacrifice of quality or capability. In China, a 0.3 mm drill was re-sharpened on average 3.5 times, whereas in the U.S., 4.2 was the average when automated techniques were used.
Willem Hofland, representing the European Brominated Flame Retardants Industry Panel in Belgium, reviewed the impact of REACH on PCB manufacturers and users. PCB manufacturers are required to provide information to their upstream chemical suppliers on how substances, particularly substances of very high concern, were used on PCBs. Also, PCB producers within the EU need to ensure that substances used to manufacture PCBs had been registered for their particular uses, and were obliged to implement all control measures communicated by their suppliers via Safety Data Sheets. He remarked that most of the substances used in PCB manufacture must still go through the REACH process and have not yet been evaluated. TBBPA, the flame retardant in FR4, was one of the few substances which had the necessary data for REACH registration.
Emma Hudson of Underwriters Laboratories in the UK gave an update on proposed changes to RoHS legislation. Since the introduction of the RoHS directive, the Enforcement Authorities have continued to find non-compliant products, with some resulting in prosecution, and proposed revisions included making RoHS compliance part of the CE Marking programme. Reducing the number of non-compliant products through strengthened and harmonised market surveillance has been considered a cost-effective way of increasing the environmental benefits provided by the directive.
Other proposed changes included the removal of the exemptions for medical devices and monitoring and control instruments. There were several methods that a manufacturer could employ to minimise the risk of receiving and selling non-compliant components: component supplier self-certification, in-house testing, management of the supply chain, third-party screening or third-party certification programmes. UL offers third-party screening or full third-party certification, and its certification programme could result in a company being allowed to apply the UL RoHS Mark to the products evaluated. Products found to comply with the requirements of the UL RoHS programme would be detailed on the open-access UL iQ Restricted Substances Database.
The session on new developments in imaging systems began with a presentation from Ilaria Pasquali of Elga Europe TOK Division on the development of dry film resists for specific applications. She explained the effects of polymer composition and molecular weight on glass transition temperature, viscosity and conformability, how the nature of the polymer determined chemical resistance and strippability, how the photoinitiator system influenced sidewall geometry and how additives could be used to improve adhesion without introducing contamination problems. A typical dry film formulation might contain between 20 and 25 different components, and by fine balancing of these ingredients, the performance of the resist could be optimised to suit particular imaging requirements.
Michael Muss, from ORC in Germany, gave a comparison of conventional exposure versus direct imaging in terms of resolution, alignment accuracy, productivity and yield for inner layer, outer layer and solder mask applications. With reference to ORC's equipment range, he described the characteristics of scattered light and collimated light sources, automatic registration and fully automatic exposure systems. ORC's direct imaging system uses a short-arc UV lamp system with a digital mirror device, rather than a laser, and different configurations and wavelengths are available to suit primary imaging resists or solder masks. Very fast photoresists were needed in order to achieve through-polymerisation. For large panel sizes, an automatic conventional exposure machine with partitioning could achieve alignment accuracy comparable with that of a direct imaging system. Although a good case could be made in support of direct imaging for yield improvement, many other factors need to be taken into consideration and it was for the customer to base his equipment choice on his own specific parameters and requirements.
Joerg Dilly from Mahr Multisensor in Germany explained how multisensor metrology differed from conventional AOI, and how the two techniques compare in terms of speed and versatility. He described a range of special sensors: Focused Laser Sensor (FLS), Measuring Laser Sensor (MLS), Chromatic White Light Sensor (CWS) and Interferometric White Light Sensor (IWS), and showed a series of application examples. A significant feature of CWL sensors was their ability to make very precise measurements in the Z-axis, which in PCB manufacture could enable more critical inspection of microvia hole quality than could be achieved by AOI. It was also possible to accurately measure features such as solder mask roughness, to nanometre dimensions if necessary.
David Ormerod of Cookson-Enthone gave the first paper on Conference Day 2, in the session on plating and hole plugging. His topic was "Environmental challenges to conventional PTH metallisation--a time for change?" He reviewed the impact of the scarcity of fundamental materials on the business and technology of the world PCB industry, with particular reference to China, where water consumption had tripled since the 1950s and demand was predicted to triple again by 2030 to 400 billion tons per annum. But water supply could not keep up with demand and the World Bank had warned that the situation would soon become unmanageable, with catastrophic consequences for future generations.
Another consideration was the possible withdrawal of certain materials used in metal finishing formulations as a consequence of RoHS and REACH legislation. Power consumption and waste generation were also critical issues. Against this background, Ormerod examined the status of electroless copper as the core metallisation process in PCB manufacture--precious metal catalyst, carcinogenic reducing agent, high water consumption, expensive waste treatment--and explained how direct metallisation systems could offer technical benefits as well as significant savings in process time, water consumption, energy consumption and waste treatment costs.
Of the direct metallisation systems available, the conductive polymer method offered the shortest process line and the greatest savings in water and energy. A characteristic of the process is that it deposited only on dielectric surfaces, eliminating the need to microetch to remove material from copper surfaces; this is a significant reliability benefit, particularly in microvia manufacturing. The process was long-established and had been refined and optimised over the past 15 years so that it offered a viable and reliable alternative to electroless copper, with substantial environmental and cost-of-ownership advantages.
Sven Kramer form Lackwerke Peters in Germany discussed experiences and challenges in hole plugging to meet industrial needs, beginning with a review of the IPC definitions of tented/covered/plugged/covered/filled/capped vias, and a comment that there remained some confusion between Europe and the U.S. as to the difference between filling and plugging. He described the formulation challenges in developing a plugging paste, particularly regarding the effects of viscosity and thermal expansion, and compared the various plugging techniques available--screen or stencil printing, roller coating and vacuum plugging--and the relative merits of each. Screen or stencil printing was effective on aspect ratios up to 4:1, roller coating to 15:1 and vacuum plugging to 40:1. Vacuum plugging is presently the most popular method, and was particularly good for blind holes and microvias.
The alternative to plugging holes with resin-based paste was to use electroplating techniques. Gerd Senge from Atotech in Germany discussed what was needed and the impact on cost. As an example of the state-of-the-art, he showed a 100 micron hole through a 400 micron core, plated full of copper but with only 19 microns plated at the surface. The Atotech preferred process was an acid copper working in a horizontal conveyorised plating machine with insoluble anodes and reverse pulse power supply at typical current density of 4-8 amps per sq dm. Senge explained how the ferrous-ferric redox reaction at the anode influenced the dissolution of copper in the ion-generator and the deposition of copper on the workpiece. Two distinct pulse-plating cycles were employed to achieve filling of through-holes, the first to form a bridge at the middle of the hole, and the second to fill the two resultant blind cavities in the same way as microvias. Copper-filled holes are extremely reliable, and can typically withstand 1,000 cycles -65°C to +150°C without failure.
Dr. Karl-Heinz Ognibeni from Sun Chemical in Germany described the development of a universal peelable mask for temporary protection of selective areas of the PCB through processing or soldering. Prerequisites were high temperature stability, good printability and print definition, high elasticity, low solder pick-up, RoHS and REACH compliance, good cohesion and easy, complete removal. A commercial product is now available which fulfilled these requirements. A novel method of application was by robot dispenser, allowing holes up to 6mm diameter to be tented, obviating the need for Kapton dots.
The final session of the conference introduced some novel plating technologies. First to speak was Dr. Karl Ryder from the University of Leicester in the UK, on developments in chemistries based on ionic liquids which had arisen out of the FP6 IonMet project in which EIPC had participated. Ionic liquids were defined as non-aqueous mixtures of salts which melted below 100°C, with unusual solvent properties and low vapour pressure. Typical examples were combinations of quaternary ammonium structures and hydrogen bond donors. An ionic-liquid-based immersion silver-plating process had been developed in cooperation with a PCB manufacturer, which overcame the problems of interfacial attack associated with proprietary nitric acid-based formulations. A pilot plant was being installed to enable the process to be scaled-up from laboratory to pre-production. The technology appeared generically applicable to metal finishing processes.
Dr. Andy Cobley from the Sonochemistry Centre of the University of Coventry in the UK described the effect of ultrasound on the gold plating of silica nanoparticles. The incorporation of small quantities of silica nanoparticles to solder had been observed to stabilise the microstructure and improve high temperature reliability, but the material was difficult to disperse unless metallised. A process was devised whereby the silica was seeded with gold then plated to form a complete gold shell around each particle. Problems of agglomeration and poor coverage could be overcome by sonification with pulsed ultrasound at the seeding stage. Low-frequency ultrasound tended to have a negative effect, but at frequencies of 1167 KHz good seeding was observed, leading to a full shell of gold at the plating stage. A UV absorbance technique enabled the progress of the seeding stage to be monitored.
Jaime Peraza Ordaz from Atotech in Spain explained the characteristics of Aurotech PEP, a versatile nickel-palladium-gold finish for soldering and wire bonding. This process enabled customers to run nickel-palladium gold on existing ENIG lines with the addition of an additional tank and a triple rinse. The palladium chemistry was very stable, with no tendency to plate out. Detailed test data was presented which indicated excellent cold ball pull, ball shear and gold wire bonding results over a wide range of bonding parameters. Multiple reflow cycles did not degrade solder joint integrity, and intermetallic formation was minimised. The process offered precious-metal cost savings over nickel-gold wire-bonding finishes.
The last presentation came from Georg Restel of MIE in Germany, on the subject of electrochemical evaluation of final surface finishes using a surface scan analyser based on the principle of sequential electrochemical reduction analysis. Using immersion tin as his example, he explained how the technique could be used to determine the quality of the coating and its surface condition, and to measure the concentration of oxides, sulphides and organic contaminants. It was also useful for studying aging effects and quantifying the growth of intermetallic layers. Results were repeatable and correlated well with focused-ion-beam measurements.
Michael Weinhold closed the proceedings and thanked presenters for their contribution and delegates for their attention. The next conference takes place in Austria, June 18-19, 2009, with a theme of cost reduction through innovation. There will be opportunities to visit the largest PCB factory in Europe, AT&S in Loeben and Europe's largest and most advanced drilling and routing service provider, Impex Leiterplatten.
More Columns from The European Angle
CircuitData: A New Open Standard for PCB Fab Data ExchangeI Never Realised It Was So Complicated!
The European Angle: Institute of Circuit Technology 43rd Annual Symposium
Ventec International Group's Martin Cotton Celebrates 50 Years in PCB Design
Reporting on the Institute of Circuit Technology Spring Seminar
EuroTech: Raw Materials Supply Chain—Critical Challenges Facing the PCB Industry
EuroTech: ENIPIG—Next Generation of PCB Surface Finish
EuroTech: Institute of Circuit Technology Northern Seminar 2016, Harrogate