-
- News
- Books
Featured Books
- pcb007 Magazine
Latest Issues
Current IssueInventing the Future with SEL
Two years after launching its state-of-the-art PCB facility, SEL shares lessons in vision, execution, and innovation, plus insights from industry icons and technology leaders shaping the future of PCB fabrication.
Sales: From Pitch to PO
From the first cold call to finally receiving that first purchase order, the July PCB007 Magazine breaks down some critical parts of the sales stack. To up your sales game, read on!
The Hole Truth: Via Integrity in an HDI World
From the drilled hole to registration across multiple sequential lamination cycles, to the quality of your copper plating, via reliability in an HDI world is becoming an ever-greater challenge. This month we look at “The Hole Truth,” from creating the “perfect” via to how you can assure via quality and reliability, the first time, every time.
- Articles
- Columns
- Links
- Media kit
||| MENU - pcb007 Magazine
Estimated reading time: 5 minutes
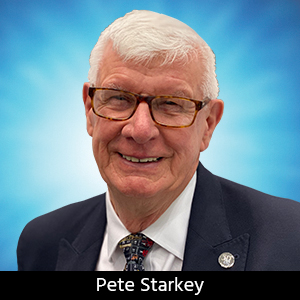
Contact Columnist Form
SMART Group Seminar on Materials and Finishes
The printed circuit board is fundamental to virtually every electronic assembly and is expected to behave predictably and reliably under the conditions of severe thermal stress experienced during soldering. But its essential attributes are often not well understood.
SMART Group borught together over 50 electronics industry professionals to Arundel on the south coast of England to participate in the seminar "Printed Circuit Materials and Finishes - What Assemblers Should Know!" SMART Group is a technical trade association dedicated to promoting education and training in the electronics manufacturing industry.
SMART Chairman Keith Bryant welcomed delegates to the seminar, which set out to address those characteristics of the printed circuit that directly affect the assembly process: The substrate material, the solder resist finish and the solderable finish, their capabilities and limitations, and methods for specifying appropriate materials. It included presentations from suppliers of laminates, solder masks and solderable finishes, and discussions of design for manufacture (DFM) and design for reliability (DFR), together with a visit to a printed circuit fabrication plant, to observe manufacturing and finishing processes from a practical perspective.
Martin Morrell, MD, of Artetch Circuits gave a comprehensive introduction to the printed circuit manufacturing process, making it clear that different manufacturers had their own preferences regarding equipment, materials and processes and there was no right or wrong way to manufacture a PCB, provided that the product met the requirement, specification and quality standard. He emphasised the need for the customer to provide complete and accurate information at the RFQ stage: Comprehensive mechanical drawing, board specification and design data, to reduce issues and delays later in the process.
Morrell's presentation certainly grabbed the attention of the audience, whose general reaction was, "I never realised it was that complicated!" And the realities of PCB manufacturing became even clearer during the ensuing tour of the Artetch factory in nearby Littlehampton, with explanations of sales office and pre-production engineering functions as well as step-by-step demonstrations of all of the principal processes and inspection and testing operations, right through to final packing and shipping. More than somewhat enlightened, delegates returned to the seminar to hear expert presentations on materials and finishes.
Isola's Alun Morgan started from first principles with his account of the characteristics and functionality of printed circuit laminates. The audience gained hands-on experience about the nature of glass yarns and fabrics, resins, pre-pregs and foils, and learned how they are manufactured as precursors then assembled together into laminates. Morgan described the properties, (mechanical, electrical and thermal) of a wide range of commercially available laminates, and reviewed their suitability for specific applications, with particular reference to thermal stability under lead-free soldering conditions. He also explained the IPC 4104B series of specifications for base materials for rigid and multilayer circuits.
Chris Wall of Electra Polymers reviewed solder mask processes and properties, and the criteria for selection of material and process to suit feature sizes and registration requirements of different design technologies. Liquid photoimageable solder masks have become the industry standard for all but the lowest-cost, low-technology applications, and high-pressure low volume air spraying was the method of choice for achieving best coating uniformity. Imaging was conventionally achieved by UV contact printing, but laser direct imaging techniques has become established where extreme registration accuracy is necessary. Wall listed many functional requirements of solder masks over and above their primary purpose of enabling mass soldering in PCB assembly, and commented that not only were they required to withstand significant additional temperature stresses when used in lead-free soldering, they encountered highly aggressive chemistry during the finishing processes of the bare board when coatings such as ENIG were specified. The recognised general performance specification for solder masks was IPC-SM-840-
Nigel White from Atotech gave an overview of electroless nickel immersion gold (ENIG), which had been adopted as a versatile solderable finish for surface mount assembly in the early 1990s and is still widely specified. The process involves preparing and activating the copper surface to initiate the autocatalytic deposition of a layer of nickel-phosphorus alloy approximately 5 microns thick, which was immediately sealed against passivation by a layer of gold 0.05 - 0.10 microns thick deposited by a chemical exchange process. During the soldering operation, the gold is dissolved in the solder and the actual joint is formed as a tin-nickel intermetallic bond. White reviewed deposition problems resulting from specific PCB layout features such as partially plugged via holes, and how they could be overcome. Careful process control is required to ensure optimum performance, but the finish has excellent shelf life and would withstand several lead-free reflow cycles, even in air, whilst maintaining its solderability.
An alternative to ENIG was presented by John Cornforth of Cookson Electronics who described their proprietary immersion silver process, which visitors to Artetch had earlier seen operating in a conveyorised horizontal line. He explained the chemistry of the silver deposition process, the significance of the preparation of the copper surface and the way in which additives and complexing agents were used to achieve fine-grained adherent silver deposits typically 0.2 microns thick. The finish gives excellent solderability with both leaded and lead-free solders and, provided recommended procedures are observed for storage and handling, has a shelf life of at least 12 months.
The final presentation of the seminar came from Matthew Beadel of Artetch Circuits, who provided a wealth of practical guidance on DFM. He urged designers to ask the advice of their PCB fabricators, making use of any available software and reading their DFM guidelines as early as possible in the design process in order to enjoy the benefits of reduced cycle times and design iterations, increased yield and reliability, reduced delay in communication of design issues, reduced time to market and reduced cost. Beadel discussed materials and multilayer constructions, design features, impedance calculations and tolerances. The essence of his message was: Only use what technology is required, never use finer features than necessary, and always talk to your fabricator.
Lively question and answer sessions, and the buzz of interactive discussion during the breaks between presentations were evidence of the success of the seminar in raising the awareness of design and assembly engineers, and giving them a good introductory insight into the realities of printed circuit manufacturing processes, materials and finishes, with particular relevance to those with a direct effect upon the cost and yield of bare board manufacture and the effectiveness of the assembly process.
More Columns from The European Angle
CircuitData: A New Open Standard for PCB Fab Data ExchangeI Never Realised It Was So Complicated!
The European Angle: Institute of Circuit Technology 43rd Annual Symposium
Ventec International Group's Martin Cotton Celebrates 50 Years in PCB Design
Reporting on the Institute of Circuit Technology Spring Seminar
EuroTech: Raw Materials Supply Chain—Critical Challenges Facing the PCB Industry
EuroTech: ENIPIG—Next Generation of PCB Surface Finish
EuroTech: Institute of Circuit Technology Northern Seminar 2016, Harrogate