-
- News
- Books
Featured Books
- pcb007 Magazine
Latest Issues
Current IssueInventing the Future with SEL
Two years after launching its state-of-the-art PCB facility, SEL shares lessons in vision, execution, and innovation, plus insights from industry icons and technology leaders shaping the future of PCB fabrication.
Sales: From Pitch to PO
From the first cold call to finally receiving that first purchase order, the July PCB007 Magazine breaks down some critical parts of the sales stack. To up your sales game, read on!
The Hole Truth: Via Integrity in an HDI World
From the drilled hole to registration across multiple sequential lamination cycles, to the quality of your copper plating, via reliability in an HDI world is becoming an ever-greater challenge. This month we look at “The Hole Truth,” from creating the “perfect” via to how you can assure via quality and reliability, the first time, every time.
- Articles
- Columns
- Links
- Media kit
||| MENU - pcb007 Magazine
Estimated reading time: 5 minutes
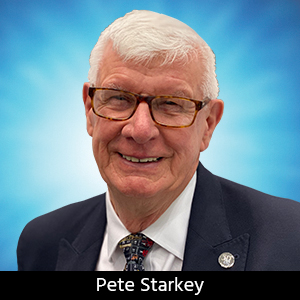
Contact Columnist Form
Adventures in Non-Conformance at SMART Group Seminar
How to make case studies in non-conformance interesting and enjoyable? Doug Pauls and Dave Hillman know the secret, and kept an audience of 80 engrossed for three hours in October with their keynote presentation at the SMART Group 25th Anniversary Seminar in Thame, Oxfordshire UK.
Doug and Dave are Principal Materials and Process Engineers with Rockwell Collins in Iowa, as well as being active members of IPC. Amongst other responsibilities, Doug is Chair of the IPC 5-30 Cleaning and Coating Committee: Dave is Chair of the IPC JSTD-002 and -003 Solderability Committees. They modestly describe themselves as "The Goops and Glues Guy" and "The Metals Guy," respectively.
With a presentation entitled Manufacturing Wrong, their stated mission was to engage, educate and entertain. Their relaxed and informal approach put delegates at ease from the outset, so no one was shy about getting involved in interactive discussion--each individual case study prompted its own question and answer session, and audience participation was eager and enthusiastic.
Doug and Dave took turns to recount the lessons learned from a series of eight case studies illustrating the consequences and costs of non-conformance--failing to do the job right-first-time, either through ignorance or by taking shortcuts. In Rockwell Collins' operating environment of high-reliability life-critical and flight-critical equipment, the costs of non-conformance--lost productivity, engineer time and additional labour to investigate, identify and rectify a problem - could easily run to hundreds of thousands of dollars.
Their first example, labelled "Bloody Bubbles" related to adhesives and conformal coatings and demonstrated how the demands of Lean Manufacturing could require processes to be operated at the limit of a control range in order to maximise throughput, at the expense of introducing variations in interaction between materials and resulting in downstream defects that required months of detective work to trace the root cause, in this instance the unpredictable appearance of bubbles in a conformal coating after environmental stress testing, even though the assemblies had been processed and inspected to specification.
It transpired that the solvent absorption characteristics of a urethane adhesive used in the assembly process varied with curing conditions. Rapid curing at higher temperature increased the tendency to subsequently absorb toluene from the coating lacquer, which was then released as bubbles during the ESS test. Curing more slowly at a lower temperature resulted in no problem. This investigation also demonstrated the value of proper evaluation and characterisation of materials, individually and in combination, before specifying them for a particular application for which they might not have been recommended in the first place.
"Look at the Pretty Finish" was a lesson in selecting metal finishes for their functionality and reliability rather than their cosmetics, with a strong recommendation to avoid bright acid tin in any electronics application.
Test coupons offer a practical means of monitoring conformal coating thickness and adhesion. But when a coupon fails an adhesion test, is it indicative of a failure in the production process it is intended to represent, or a variation in the nature of the coupon itself? "Stupid Coupons" was an illustration of what can go wrong when certain physical characteristics are not taken into account in materials qualification. In this case, a batch of coupons had been manufactured with a solder mask that, although on the qualified materials list, had an unusually low surface energy. And this resulted in apparently marginal adhesion of conformal coating, whereas there was no actual problem with production assemblies.
Good intentions sometimes have bad outcomes, a case in point being the operator who used rubber bands and sticky labels to secure packages of silver-finish PCBs, not knowing that the sulphur content negated the protective qualities of Silver-Saver wrapping paper. Or the OEMs obsessed with cleaning assemblies to the point that the surface of the solder became depleted in tin and took on a purplish "Barney the Dinosaur" hue. Talking of solder, the supplier who imposed a two-year shelf life on cored wire solder did so to satisfy the auditor who did not have a tick-box for "indefinite." Dave Hillman challenged the audience to guess which-was-which of four samples subjected to a JSTD-004 spread test. Ironically, the best-looking result came from a solder sample 30 years old.
The effects on product reliability of hand sanitizers and lotions, and the effects on solderability of pencil erasers and glass-fibre brushes were other areas of discussion. It was a tale of a particularly difficult customer that especially got delegates' heads nodding in concurrence. The customer is never wrong, except perhaps when the "white residues" he observed at x200 magnification and presumed must be the cause of an isolated failure that was not substantiated by data. The white residues were alleged to be due to a "contaminated" process, a holdover from the days where any visible flux or flux residue was bad. The true cause of the failure was eventually determined to be the customer's own test chamber, but not before losinghundreds of engineer-hours and weeks of lost production time. The lessons learned were two-fold: firstly that test chambers are often as much as fault as the device under test, and secondly that had the company not significantly invested in their understanding of their chosen materials and manufacturing processes, the customer would have imposed a wide array of non-value added controls.
"Quality takes time" was a significant point emphasised by this Manufacturing Wrong presentation, but "Quality takes knowledge" was probably the more serious message. Retirement of long-serving engineers was progressively draining in-depth knowledge from the industry and this had been recognized by companies like Rockwell Collins, where there was a focus on education to ensure that the know-how and information accumulated over decades of experience was properly passed down to complement the talents of the upcoming generation.
The Doug and Dave Roadshow could very easily have held the attention of the audience for the rest of the day if SMART Group Vice Chairman Graham Naisbitt had not reluctantly closed the session to keep the programme on schedule.
Pauls and Hillman got little opportunity for rest and refreshment afterwards: They remained surrounded by people keen to continue to compare, discuss and exchange their knowledge and experience.Editor's Note: For more military/aerospace news, visit our dedicated site here.Follow I-Connect007 on Twitter here.
More Columns from The European Angle
CircuitData: A New Open Standard for PCB Fab Data ExchangeI Never Realised It Was So Complicated!
The European Angle: Institute of Circuit Technology 43rd Annual Symposium
Ventec International Group's Martin Cotton Celebrates 50 Years in PCB Design
Reporting on the Institute of Circuit Technology Spring Seminar
EuroTech: Raw Materials Supply Chain—Critical Challenges Facing the PCB Industry
EuroTech: ENIPIG—Next Generation of PCB Surface Finish
EuroTech: Institute of Circuit Technology Northern Seminar 2016, Harrogate