-
- News
- Books
Featured Books
- pcb007 Magazine
Latest Issues
Current IssueInventing the Future with SEL
Two years after launching its state-of-the-art PCB facility, SEL shares lessons in vision, execution, and innovation, plus insights from industry icons and technology leaders shaping the future of PCB fabrication.
Sales: From Pitch to PO
From the first cold call to finally receiving that first purchase order, the July PCB007 Magazine breaks down some critical parts of the sales stack. To up your sales game, read on!
The Hole Truth: Via Integrity in an HDI World
From the drilled hole to registration across multiple sequential lamination cycles, to the quality of your copper plating, via reliability in an HDI world is becoming an ever-greater challenge. This month we look at “The Hole Truth,” from creating the “perfect” via to how you can assure via quality and reliability, the first time, every time.
- Articles
- Columns
- Links
- Media kit
||| MENU - pcb007 Magazine
Estimated reading time: 3 minutes
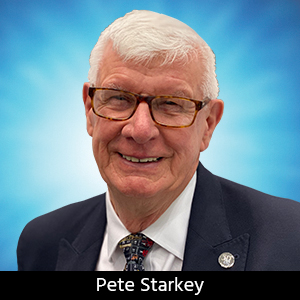
Contact Columnist Form
An Inside View: The Wurth Elektronik Design Conference
I doubt whether many high-specification PCBs were designed in the north of England on 10 October 2011 - most of the top designers from the region appeared to be in Manchester at the Würth Elektronik Design Conference!
I was privileged to be invited to sit in on what has become an annual road show event, with a succession of dates in UK, Netherlands, Belgium, France and Spain.
Würth Elektronik Circuit Board Technology is the largest manufacturer of circuit boards in Europe, with over 1000 employees and three production plants in south-west Germany, specialising in prototypes and small and medium-sized orders, service orientated and respected for innovative circuit board technologies and system solutions.
Würth’s product specialists and applications experts came to Manchester to share their knowledge and expertise, to bring design engineers up to date with current developments and capabilities, and to explain how to produce optimised circuit board designs and specifications by understanding the realities of manufacturing processes and material properties. “If you don’t know how it’s made, how can you possibly design it?”
The designers who filled the conference room had a genuine desire to learn and made the most of the opportunity to escape from the cosy security of the drawing office for a few hours, even though it involved braving the wind and rain of an October day. The cost to their employers of a few hours absent from work would be repaid in value many times over by the real-world knowledge they would take back, which would help them to design more functional, cost-effective and reliable circuit boards.
Apologies if I sound over-sentimental: I spent many years as a PCB fabricator actively encouraging designers to try to understand what we could and could not achieve, what was cost-effective and what not, and to involve us in discussion at the earliest possible stage of the design project. Sometimes I succeeded, sometimes not. The good guys were the ones who spread their initial ideas on the table and asked a lot of “what-if” questions before they ever started their layout or got carried away by numbers on material suppliers’ data sheets. The bad guys always knew better and presented us with fait-accompli designs and specifications that presented all sorts of manufacturing problems and yield issues. So I could identify very closely with Würth’s objectives.
The event was organised with characteristic German precision and attention to detail. Responsible for international sales, Gerolf Heldmaier introduced the company and its range of services, before handing over to product managers Andreas Schilpp, Bert Heinz and Roland Schönholz, to deliver comprehensive tutorials on 3D technology (flex, flex-rigid and semi-flex), heat management, HDI microvia technology, signal integrity and future technologies.
What impressed me most was the willingness to share information and the openness with which the Würth people disclosed the fine details of their engineering and manufacturing capabilities and limitations for the benefit of the very attentive audience. It was real-world stuff! They even asked spot questions to check whether people had understood what had been said, and awarded little prizes for correct answers – a neat ploy, which made people all the more attentive.
And some exciting leading-edge technology was presented, particularly Roland Schönholz’s explanation of what could be achieved with a CO2 laser and some creative thinking, to produce precisely dimensioned cavities in FR-4 PCBs into which flip chips and IGBT devices could be placed and interconnected. There was enormous scope in RFID applications, for example implanting the manufacturing and testing history of a PCB, together with a unique signature, was a very effective anti-counterfeiting procedure for high-value electronic devices.
I felt inspired and motivated by Würth’s design conference. It made me wish I was back in the industry. They did an excellent job. The designers in the audience received some excellent knowledge and guidance and, as a bonus, had a great opportunity to network with other designers
Those who came were the winners: the losers were the ones who didn’t make the effort – but you probably couldn’t teach those guys anything about design anyway.
More Columns from The European Angle
CircuitData: A New Open Standard for PCB Fab Data ExchangeI Never Realised It Was So Complicated!
The European Angle: Institute of Circuit Technology 43rd Annual Symposium
Ventec International Group's Martin Cotton Celebrates 50 Years in PCB Design
Reporting on the Institute of Circuit Technology Spring Seminar
EuroTech: Raw Materials Supply Chain—Critical Challenges Facing the PCB Industry
EuroTech: ENIPIG—Next Generation of PCB Surface Finish
EuroTech: Institute of Circuit Technology Northern Seminar 2016, Harrogate