-
- News
- Books
Featured Books
- pcb007 Magazine
Latest Issues
Current IssueInventing the Future with SEL
Two years after launching its state-of-the-art PCB facility, SEL shares lessons in vision, execution, and innovation, plus insights from industry icons and technology leaders shaping the future of PCB fabrication.
Sales: From Pitch to PO
From the first cold call to finally receiving that first purchase order, the July PCB007 Magazine breaks down some critical parts of the sales stack. To up your sales game, read on!
The Hole Truth: Via Integrity in an HDI World
From the drilled hole to registration across multiple sequential lamination cycles, to the quality of your copper plating, via reliability in an HDI world is becoming an ever-greater challenge. This month we look at “The Hole Truth,” from creating the “perfect” via to how you can assure via quality and reliability, the first time, every time.
- Articles
- Columns
- Links
- Media kit
||| MENU - pcb007 Magazine
Estimated reading time: 13 minutes
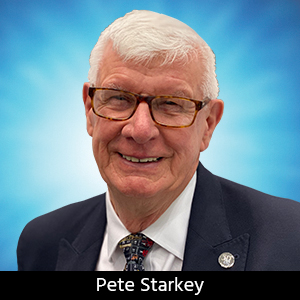
Contact Columnist Form
IeMRC Conference: One Day of Education to Last a Lifetime
Henry Ford College at Loughborough University was a popular and appropriate venue for the 7th Annual Conference of the Innovative Electronics Manufacturing Research Centre (IeMRC), the UK’s internationally recognised provider of world-class electronics manufacturing research.
IeMRC Coordinator Dr. Darren Cadman made the opening remarks, gave a brief update of the status of past, current, and future projects, and introduced keynote speaker Professor Roger Whatmore from the Tyndall National Institute in Cork, Ireland, who presented “Recent advances in pyroelectric materials and their applications: People Counting, Cooling, and Energy Harvesting.”
The pyroelectric effect is the change in polarisation of a polar material with temperature, which was first recognised over a century ago, leading to the discovery of the piezoelectric effect. From the basic physics of pyroelectric and related electrocaloric effects, derived from interactions between electric displacement, electric field, temperature, and entropy, Professor Whatmore explained the construction and operation of pyroelectric infrared detectors and how they were sensitive to very small changes in infrared flux, which made them particularly suitable to sensing and monitoring the movement of people.
Performance and cost were a function of the materials used and, from a wide range of candidate materials, pyroelectric ceramics offered advantages in array fabrication and could be chemically doped to modify their properties. Professor Whatmore discussed tape-casting methods for producing functionally gradient lead zirconate titanate (PZT) ceramics, then described low-temperature sol-gel processes for depositing ferroelectric thin films direct on silicon ASICs to make integrated arrays and fabricate MEMS-based structures. Arrays of thin-film pyroelectric detector elements could be combined with three-dimensional radiation collectors to improve their efficiency.
In an alternative application, pyroelectric energy harvesting had been shown to be significantly higher in efficiency than thermoelectric methods.
Converse of the pyroelectric effect was the electrocaloric effect: The change in temperature which occurred when an electric field was applied to a pyroelectric material, and the electrocaloric effect in thin films offered potential for solid state refrigeration.
It seemed the business of supplying aircraft to the military had undergone a radical transformation. No longer did manufacturers simply supply a product; they were now required to provide an availability of the product. In a two-part presentation, Paul Green from BAE Systems and Dr. Linda Newnes from University of Bath described how a collaborative of universities and industrial partners, representing the supply chain from concept design through to manufacture and disposal, was working to provide a set of modelling tools to enable the manufacturer to estimate the cost of providing a long-term availability contract. Green began by outlining the differences between traditional and modern support solutions. Effectively, all the military now wanted to do was fly the aircraft and it was the responsibility of the industry to keep the aircraft available. “What are the cost relationships we need to understand?” he asked, then added, “Can you give me a crystal ball?”
Dr. Newnes listed and examined cost estimating relationships and described the challenges of acquiring quality data for through-life costing: A paradigm shift was necessary and one of the first questions to ask was what should be done differently now if designing for service. She emphasised the need to provide evidence-based decisions in terms of identifying a methodological approach that could be utilised to model a true representation of cost of availability that encompassed the factors influencing the cost of providing a service. Taking as an illustrative example a very simple scenario of a hand dryer on an availability contract to dry 100 pairs of hands per day, she demonstrated the enormous number of factors involved, questions to be asked, and decisions to be made. In particular, how would success and performance be measured and how would the provider would be paid for providing the service? Would it be on the basis of performance or availability? She advocated “system thinking” in an operations-based approach and gave an indication of how the Costing for Avionic Through-life Availability (CATA) team of academic and industrial partners was addressing its extraordinarily complex task.
The theme of the second conference session was assembly and test, and the first speaker, Professor Mark Johnson from University of Nottingham, gave a presentation on high-performance low-cost power modules for energy smart network applications. Predicting that by 2050 the UK would be supported by an integrated smart energy infrastructure, he discussed the role of power electronics in the conversion of electricity from one form to another, and the control of energy flow to provide for grid quality and security, whilst underpinning the low-carbon energy supply chain. Against this background, he focused on the characteristics and limitations of power modules, specifically voltage source converters for high-voltage DC transmission. These converters were typically based on insulated-gate bipolar transistor switches, connected in series or in chain-link modules to withstand voltages in excess of 11kV. It was necessary to build-in a degree of redundancy, but preferable that in the event of a switch failing it should fail to a short-circuit condition. Historically, this requirement had been addressed by complex “Press-Pack” or “StakPak” devices which were expensive and had limited flexibility. The challenge was to develop a low-cost alternative which would still fail-to-short-circuit, using existing die technology, existing PCB processes, and appropriate high-reliability bonding processes. Planar modules offered many potential advantages, particularly the elimination of weaknesses associated with bond wires and the opportunity for more efficient cooling, and work was under way to simplify the assembly process. Sintered silver nano-particle pastes were the preferred bonding medium, with polyimide flexible PCB interconnects using nano-paste filled vias providing alignment and circuit functions.
The requirement for ultra-fine pitch interconnects for micro-BGAs and flip-chip devices presented major challenges, particularly in achieving acceptable yields on large-format devices such as high-resolution sensors. Changqing Liu from Loughborough University reported the progress of a project investigating the feasibility of using to metal-coated polymer microspheres to replace traditional solder joints and achieve interconnection at pitches as fine as 10 microns. The capability already existed to manufacture mono-sized microspheres and to coat them with nickel-gold, and these materials had been used in anisotropic conductive adhesives. The objective of the project was to find a way of selectively depositing controlled quantities of these particles directly onto the bond pads of integrated circuits. Various routes had been considered: Physical, chemical, mechanical, electrical, electromagnetic, and electrochemical. Chemical methods using self-assembled octanethiol monolayers had been evaluated, but yields were low. Electrophoretic deposition appeared to be a viable method, but required the microspheres to carry an ionic charge and a process had been developed to acid-etch the surface of the nickel-gold coating. This resulted in a positive surface charge through the formation of Ni2+ ions and, hence, enabled the microspheres to be deposited electrophoretically. Once conditions were optimised it had been demonstrated that 100% deposition yield could be achieved on full 6” wafers with pads as small as 40 microns on 75-micron pitch, and low-temperature thermocompression bonds had been successfully formed between bumped devices and gold substrates.
Through-life, non-destructive monitoring of flip-chip solder joints in automotive electronic systems was the subject of the presentation from Ryan Swee How Yang from Liverpool John Moores University. He began by stating that 20% of the value of a typical automobile was in its electronics, and 80% of automotive innovation involved electronic systems. Flip-chip-on-board assemblies were widely used in automotive electronics, which were expected to operate reliably in harsh environments, and flip-chip solder interconnections tended to be the weak link because of thermal expansion mismatch between silicon die and organic substrate potentially resulting in fatigue failure. The project objective was to track the condition of solder joints from manufacture to failure using non-destructive techniques, and to assess how reliability was influenced by joint position. Acoustic micro-imaging was most effective in detecting gap-type defects, but was not sensitive to volumetric defects where X-ray was the preferred method. Using the two techniques in combination offered the basis of a complementary method for automatic inspection and non-destructive monitoring of solder joints. An FR4 test board with double-sided flip chips had been used as a test vehicle in a 96-cycle accelerated thermal cycle test, with samples checked at 8-cycle intervals by ultrasound, X-ray and microsectioning. Analysis and feature extraction from individual and combined ultrasound and X-ray images had yielded information about the characteristics of good joints and fractured joints and enabled discrimination between fracture and voids. It was possible to plot three-dimensional failure distribution to determine how reliability was related to the position of the flip chip on the board.
Another aspect of interconnection reliability was addressed in the presentation from Maria Mergkizoudi of Loughborough University on wire-bond reliability under extreme environments. She explained that qualification tests for wire-bonded devices were typically carried out in separate environments. For example: Temperature storage, temperature cycling, and vibration, and this approach could fail to detect the effects of combined parameters. Her work was aimed at testing gold-wire-bonded components under a combination of thermal loading up to 180ºC and mechanical loading in the form of high frequency vibration. The investigation covered bond strength and mechanical integrity, electrical resistance changes, microstructural defects induced, the role of wire orientation on wire degradation, and the effect of applied conditions on loop geometry, using wire-pull and ball-shear testing, electrical resistance measurement, and metallographic examination. Results revealed significant differences between thermal testing without vibration and testing in thermal-vibration combination. Observations on gold-wire ball-bonded devices indicated an appreciable decrease in electrical resistance after testing, which could be attributed to annealing of the wire, a reduction in the shear force to failure of the ball bonds, particularly at higher temperature and low frequency vibration, and a more severe distortion of wire loops when testing at low frequencies. Future work would focus on extending the vibration-temperature regime and examining the effect on wire bond pull strengths.
PCBs were the theme of the afternoon conference session and the keynote presentation was given by Alun Morgan, Chairman of EIPC and Director of OEM Marketing with Isola Europe. Noted for his ability to present complex technical issues in plain language, he gave a detailed insight into the characteristics, applications, and limitations of low-loss, high-speed PCB materials, starting with an explanation of the causes of signal losses and where they occurred and what could be done by the laminate manufacturer to reduce them.
Losses fell into two major categories: Conduction and dielectric. Conduction losses occurred in the copper and, as signal frequency increased, were increasingly associated with the surface of the copper because of a phenomenon known as the “skin effect.” This was the tendency of an alternating current to distribute itself within a conductor such that its current density was highest near the surface. As a result, current flowed mainly at the "skin" of the conductor, and the depth of the skin varied enormously with frequency. For example, for copper it was 9.3mm at 50Hz, 6.6 microns at 100MHz and 0.66 microns at 10GHz. The skin effect effectively reduced the current carrying capacity of the conductor and increased its resistance at higher frequencies. Copper foils for PCB laminates were “treated” during manufacture to give a rough surface to promote good bonding to resin: Standard foil had a treatment depth of about 10 microns. At low frequencies, the treatment had little effect on signal loss but because of the skin effect it could have a dramatic effect at high frequencies, which was why low-profile foils were available for high-frequency applications.
Dielectric losses resulted from alternating signals causing polarisation and molecular vibration within the glass and resin components of the laminate, generating heat, a familiar example being the microwave oven. The dielectric constants of glass and resin were different, which meant that in a glass-fabric reinforced laminate the microimpedance effects of filament distribution could cause problems with signal integrity ay high frequencies. Laminate manufacturers had begun to use square-weave fabrics with spread fibres to minimise this effect. Morgan listed loss factors for a range of PCB substrate materials. Standard FR4 had a loss factor of 0.015 at 1GHz, compared with 0.002 for PTFE and 0.003 for certain ceramic-filled materials. New-generation, non-PTFE, non-filled PCB substrate materials were becoming available with loss factor around 0.003 at 1 GHz as a lower-cost, easier-processing alternative to traditional solutions.
Axel Bindel from Loughborough University stressed the importance of clear and easy-to-access information about the manufacturing history of a product in supporting traceability requirements and decision making at end-of-life, as well as providing scope for re-use and re-manufacturing. He explained that information could be stored in an electronic product by embedding an RFID tag within the structure of the PCB, with the facility to read or write data wirelessly, and described how this had been successfully achieved. During the manufacture of a multilayer PCB, the RFID chip was assembled on to an inner layer by a flip-chip process, and became fully encapsulated within the epoxy resin during the laminating process. The only significant modification to the PCB layout was the incorporation of an antenna in the periphery of the design. The embedded RFID had been shown to withstand harsh environments and multiple thermal shocks. Product information could be stored from the very beginning of the manufacturing supply chain and during subsequent production processes for each individual product and accessed with a hand-held reader even when the PCB assembly was enclosed within a piece of equipment.
The effect of ultrasound on electroless copper plating was the subject of the presentation by Amirah Kassim from Coventry University, who reported the progress of the IeMRC-funded ULTIEmet project. Using a commercially available EDTA-based self-accelerating electroless copper process, initial studies had examined the effect of ultrasound of different frequencies on the stability of the bath, and 40KHz had been chosen as the working frequency for plating-rate experiments as it caused no spontaneous precipitation of copper. Plating rates were measured over a range of operating temperatures, with and without ultrasonic agitation, and only slight increases were observed when ultrasound was applied from the start of the process. It had been shown that, in the early stages of deposition, ultrasonic agitation was tending to scrub the palladium activator off the surface and reduce the plating efficiency. When a delay was introduced to enable complete initiation before the application of ultrasound, a significant increase in plating rate was observed. Ultrasonic agitation also appeared to yield a finer-grain deposit with improved mechanical properties.
The final presentation was given by Dr. Karl Ryder from University of Leicester, a partner in the EU Framework 7 funded ASPIS project. His department specialised in developing applications for ionic liquids and as part of the ASPIS project was investigating immersion gold processes based on deep-eutectic solvents as an alternative to aqueous processes which were known to have been contributed to “black pad” effects on traditional electroless nickel-immersion gold solderable finishes. Immersion gold had been deposited on a standard aqueous electroless nickel surface from solutions in a deep eutectic solvent based on readily available choline chloride and ethylene glycol. Three different gold salts had been used: Gold chloride, gold cyanide, and potassium cyanoaurate, and their electrochemical behaviour had been studied.A standard aqueous solution based on citric acid had been used as a control and plating rates had been measured with a quartz crystal microbalance. Immersion gold deposited from the gold cyanide–ionic liquid formulation was bright and uniform in appearance, and gave faster and more reliable solder wetting than the deposit produced from the aqueous control formulation. Addition of cyanide to the ionic liquid formulation had been observed to improve plating rate and deposit appearance. Future work would include further investigation of the effect of additives other than cyanide and the effect of ageing on solderability.
The 7th Annual Conference was yet another outstanding IeMRC event and a great credit should be given to the team at Loughborough. If I might steal a few words from the IeMRC mission statement to capture the spirit: “….focus on sustaining and growing high value manufacturing in the UK by delivering innovative and exploitable new technologies…,” and reflect upon a statement attributed to Henry Ford, displayed on a wall in the conference venue: “If I had asked people what they wanted, they would have said faster horses.”Editor's Note: All photos courtesy of Vin Scothern, Loughborough University.
More Columns from The European Angle
CircuitData: A New Open Standard for PCB Fab Data ExchangeI Never Realised It Was So Complicated!
The European Angle: Institute of Circuit Technology 43rd Annual Symposium
Ventec International Group's Martin Cotton Celebrates 50 Years in PCB Design
Reporting on the Institute of Circuit Technology Spring Seminar
EuroTech: Raw Materials Supply Chain—Critical Challenges Facing the PCB Industry
EuroTech: ENIPIG—Next Generation of PCB Surface Finish
EuroTech: Institute of Circuit Technology Northern Seminar 2016, Harrogate