-
- News
- Books
Featured Books
- pcb007 Magazine
Latest Issues
Current IssueInventing the Future with SEL
Two years after launching its state-of-the-art PCB facility, SEL shares lessons in vision, execution, and innovation, plus insights from industry icons and technology leaders shaping the future of PCB fabrication.
Sales: From Pitch to PO
From the first cold call to finally receiving that first purchase order, the July PCB007 Magazine breaks down some critical parts of the sales stack. To up your sales game, read on!
The Hole Truth: Via Integrity in an HDI World
From the drilled hole to registration across multiple sequential lamination cycles, to the quality of your copper plating, via reliability in an HDI world is becoming an ever-greater challenge. This month we look at “The Hole Truth,” from creating the “perfect” via to how you can assure via quality and reliability, the first time, every time.
- Articles
- Columns
- Links
- Media kit
||| MENU - pcb007 Magazine
Estimated reading time: 13 minutes
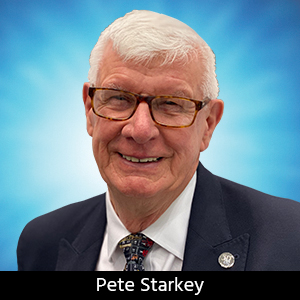
Contact Columnist Form
A Walk on the Technical Side: SMART Group's 2012 European Conference, Day 2
The second day of SMART Group's 2012 European Conference got underway in Thame, a charming old market town close to the Chiltern Hills in Oxfordshire, UK with a second grouping of industry experts ready to present and attendees eager to learn. Technical Editor Pete Starkey made the trip for I-Connect007 and continues his report.
SMART Group Technical Vice Chairman Nigel Burtt welcomed delegates and introduced the first speaker of the day, Sue Knight, chair of the technical committee, presenting “Why can’t people communicate?” Knight began by telling the audience, “We’re doing well! We got you in the room--you’ve acknowledged the need to communicate!” then, quoting C. Northcote Parkinson: “The void created by the failure to communicate is soon filled with poison, drivel, and misrepresentation,” and Seth Godin: "The less people know, the more they yell!”
Probably the most appropriate quote was one attributed to George Bernard Shaw: “The problem with communication is the illusion that it has occurred.” Reflecting upon the communication challenges she encountered in her work as a manufacturing engineering manager, she listed a set of guideline advice: Listen and understand, talk early and often, define common ground and goals, cooperate and collaborate, compromise, focus, and understand the whys as well as the whats. Finally, she encouraged the audience not to be afraid of asking the dumb question, something to bear in mind for the rest of the day. Certainly, plenty of questions were asked and answered during the discussion sessions between presentations, none of them dumb, and everyone benefited from the knowledge and information that was exchanged.
Back to the technical stuff: SMART Technical Director Bob Willis gave an excellent practical overview of the introduction of package-on-package assembly technology, which had in fact first been used in cell-phones as long ago as 2004 and was now accelerating rapidly, driven by growth in smartphones and tablets. He described assembly processes, fundamentally BGA on BGA, with as many as four packages in a stack, beginning with printing paste and placing the first package, then dipping the second package in a fluid--either a flux or a thin solder paste--and placing it on top before reflowing. It was critical to ensure that all the balls on the second package were fluxed, to avoid the possibility of dry joints, and assemblers had the option of subcontracting this operation to specialists who would return the components pre-stacked and aligned. Willis described next-generation packages, with particular reference to Amkor’s through-mould-via concept, as enablers of higher device speeds and package densities, and advances in solder paste technology, which had resulted in improved assembly yields. His videos showed clearly what happened during package-on-package assembly reflow, and demonstrated the consequences of in-process thermal distortion of packages. He also illustrated what to expect and what could be achieved by optical and X-ray inspection, as well as giving an abundance of practical hints and tips on material selection and machine housekeeping.
“Who’s assembling QFNs?” asked Alan Colquhoun, Principal Engineer DfM at BAE Systems Maritime Services. Several hands went up in the audience. “Who’s having problems?”--the same show of hands! Colquhoun had first seen QFNs introduced into production five years ago. They were thought to offer a simple solution to space constraints and FR-style devices and were adopted by most of BAE Systems’ customers without warning, and with little or no up-front solder or life trials being conducted. Colquhoun and his colleagues had highlighted concerns about reliability and, although no issues had been expected, they had encountered unsoldered pads, voids in base solder, insufficient solder on side terminations, tilted components, and tombstoning. Problems associated with thermal expansion coefficient, solder opens and shorts, flux entrapment, and voiding had been systematically investigated and resolved. It was now known that, because of their small package size and fine pitch, QFN devices required specific footprint geometries to enable successful soldering. BAE Systems had worked closely with several customers to enhance the manufacturability and reliability of QFN assemblies through the use of tailored soldering processes and pad-design features. Some concerns still existed about successful cleaning under low stand-off packages and thermal expansion mismatch. Manual X-ray had proved a useful inspection technique, although it did depend on highly experienced operators.
Current status was that BAE Systems Maritime Services were placing QFN devices on 40% of their product, and seeing few or no defects. Colquhoun maintained that QFNs were not simple devices that could be easily soldered. They presented a lot of technically challenging problems which could be overcome but needed investment in process and pad design to get it right. He advised working closely with designers and explaining assembly issues to them. The device manufacturers’ recommendations for footprints were often performance related and not process driven. His concluding words were: “Know the limitations of your process, or you’re on a hiding to nothing!”
Colquhoun’s reference to difficulties in cleaning under low stand-off packages provided a topical lead-in for Rob Murphy from Zestron to discuss how these issues could be addressed. Lead-free soldering temperature profiles resulted in harder residues and high packaging densities and low component stand-offs made the residues more difficult to access with cleaning processes. Moreover, partly attacking residues was probably more undesirable than not attacking them at all, because of effects like bringing activators to the surface after having been effectively sealed within the bulk of the residue. Murphy explained that a typical flux contained resin or rosin, activators, thixotropic agents and solvent. After soldering the only component missing was solvent. The remains of the rest of the formulation stayed on the surface of the assembly as residue, presenting a challenge to the cleaning process. He described various aqueous, semi-aqueous and water-free cleaning options, and showed how a test matrix had been designed to study the effectiveness of different processes for a range of component stand-off heights. Test results were evaluated on the basis of: the influence of process type with a consistent 0.1 mm stand-off, constant cleaning cycle times and constant bath temperature; the influence of stand-off; the influence of time and temperature for equal amounts of contamination and stand-off, and the influence of component geometry. After reviewing the results in detail, Murphy concluded that there was no obvious winner for mechanically supported cleaning methods. The cleaning process had to be developed to suit the flux residues on the board, like the key for a lock, and residue-free rinsing emerged as a significant contributor to overall cleaning performance. He considered test trials to be essential, and that before selecting a particular process a detailed definition of all the process requirements as well as individually tailored cleaning trials should be carried out. In essence: “Get your chemistry matched to what you’re trying to remove and do your trials up-front!”
Martin Wickham came from the National Physical Laboratory to report work which he and Dr. Chris Hunt had done to assess re-terminated RoHS components for tin-lead applications. There had long been concern in some market sectors that tin finish on component terminations could lead to product or system failure through tin whiskers. Changing the solderable finish on components after supply had been seen as a solution, but some questions needed to be answered about the impact and reliability of the re-termination process, which involved immersion of the component terminations in tin-lead solder. A test programme had been designed around a representative selection of component package styles, all from RoHS-compliant sources. There were 15 surface mount package styles, ranging from chip components through QFPs to BGAs up to 256 I/Os, and 10 through-hole styles up to 14 I/Os. Components were characterised before and after re-termination by XRFS, microsectioning, solderability testing and BGA ball-shear measurement, then assembled onto test boards and thermal cycled 55ºC to +125ºC with constant monitoring and periodic shear testing and microsectioning. The solderability of the re-terminated components was found to be equal to or better than that of original tin-finished components. Ball shear results for BGA components were acceptable and thermal cycle solder joint reliability was improved for re-terminated components. Some issues were observed during visual inspection of through-hole components: some body configurations were unsuitable for immersion in tin-lead solder and this could lead to component damage or incomplete conversion of the termination in these areas
Next presentation came from the other partner in the Rockwell Collins Doug-and-Dave double-act. Doug Pauls reported on lessons learned from the introduction of aqueous-based conformal coatings. Environmental legislation and health and safety considerations had driven Rockwell Collins to contemplate a change from their established solvent-based one-part acrylic conformal coating to a non-VOC alternative rather than try to substitute more benign solvents, and trials of aqueous based materials had started as early as 2001. The company had begun implementing aqueous based coatings on products in 2006 and they were currently used on 40 different products with varying degrees of success. Compared with the one-part acrylic standard coating, the aqueous-based materials were tougher, more chemically resistant and were capable of operating at higher temperatures, but had the disadvantages of slower drying time, especially for thick accumulations, and remaining electrically conductive or semi-conductive until all the water had been removed. Re-workability was an issue with design engineering and prototype laboratories.
Reflecting upon the lessons he had learned, Pauls commented that thin, flat films on thin, flat substrates gave best-case results, but did not tell the full story about three-dimensional aspects of coating. He advocated using a test vehicle representing actual product, such as the IPC-B-52 design and recommended cyclic humidity testing to examine how a coating reacted to changes in the environment. The second important consideration was a proper understanding of the curing of aqueous based processes, which were electrically conductive in their liquid form and passed through a semi-conductive to a no-conductive state during the cure. Pauls pointed out that all three states could exist simultaneously in a three-dimensional coating mass, and that attempts to force the cure with a higher temperature in a shorter time could cause excessive bubbling and voiding. Perhaps the most important lesson of all was that material changes were easy, but cultural changes were not…
Lead-free paste characterisation was the topic of the presentation from Joerg Trodler of Heraeus, who examined the factors influencing wetting and the creation of voids, and their effects on reliability. A series of DOEs had been devised in cooperation with the Technical University of Dresden to study the effects on voiding of variables including stencil, printed circuit board, component, solder paste, printing, pick-and-place and soldering. Test boards were finished with immersion tin and ENIG, and two SAC solder pastes with different powder sizes were used. A general observation was that a solder paste that gave good wettability would create more voids. However, large components with heat-sinking tendencies required good wettability, so some compromise was necessary. For BGAs, the worst wetting appeared to give the least voids and John Lau had explained that this was a function of whether the ball or the paste melted first. Heraeus had cooperated with Siemens and AT&S to study the influence of voids on reliability and concluded that it did not matter provided a good solder joint had been made.
Charles Cawthorne from missile systems developer MBDA discussed the application of DfM and DfR in high-reliability electronics manufacture. He explained that DfM and DfR were aspects that should be considered during the product concept and definition phase to optimise manufacturing methods, processes and practices to reduce cost, and to improve reliability. His presentation illustrated many of the principles associated with DfM and DfR and included examples of the methodologies employed by MBDA. It was essential to begin the process as soon as possible within the design cycle, and certainly before PCB layout. The essential elements of DfM were: Keep it simple, minimise bill of materials, minimise device complexity, ensure compatibility with the manufacturing process, and use established and approved components. MBDA had created their own component guide list, which catalogued authorised packages and assembly recommendations. They took a multidisciplinary approach to DfM and included electronic design, manufacturing, procurement, reliability, and quality engineers in a Design Component Check List Review, which identified assembly risks, potential obsolescence risks and potential ruggedisation requirements. IPC-7351B was used as the standard for calculating surface mount footprints, IPC-7251 for through-hole land patterns, and IPC-2221, IPC-2222, IPC-2223 and IPC-2226 as appropriate, for general design and layout rules. Regular meetings were held between manufacturing and design and comprehensive first-build results were fed back. MBDA’s DfR procedure considered aspects such as component selection rules, including LCCC precautions, re-balling of BGAs to avoid metallurgical conflicts, and a tin whisker mitigation strategy based on GEIA-STD-0005-2. For lead-free soldering, they specified FR4 laminate with Tg higher than 170ºC and defined CTE and thermal endurance. The basic DfR rules for PCB design and specification were to keep it as simple as possible, to minimise layer count and to avoid sequential builds and microvias.
Controlling electrostatic discharge in automated assembly and handling systems was the subject of the presentation from Dr. Jeremy Smallwood, founder of Electrostatic Solutions Ltd. He began by explaining the nature of ESD, and how a high level of electrostatic charge could easily be built up then released suddenly as a high-current ESD event, typically lasting no more than 200 nanoseconds, but possibly involving a peak current of tens of amps. In electronics manufacture, people were the greatest source of ESD damage in manual handling and assembly. Charged metal objects could also be a source of ESD and these could occur in manual handling as ungrounded metal tools, or in automated handling, through ungrounded machine parts. Charged devices could discharge to other items, especially in automated assembly. The equivalent electric circuit used to model ESD susceptibility had three elements: Charge storage, series resistance, and series inductance. The Human Body Model had a typical charge storage capacity of 100pF and peak power of about 1 Watt at 500 volts. Figures for the Machine Model were typically 200pF and 400 Watts at 500 volts, and for the Charged Device Model 1-30pF and 2 kilowatts at 500 volts. And the three models had quite different waveforms. The measure of ESD susceptibility was ESD Withstand Voltage, and most ESD programmes were designed to protect devices down to 100 volts Human Body Model ESD Withstand. Dr Smallwood explained the details of the ESD control strategies and precautions required to create an ESD-protected corridor around the PCB or device path through equipment.
Last to speak in the conference programme was Dave Hillman, returning to the rostrum to read “The Last Will and Testament of the Lead-Free BGA Void.” Those who had attended the 2011 conference may have had a sense of deja-vu: Hadn’t Hillman done this presentation before? Yes, but that had been tin-lead, this was lead-free. The current IPC J-STD-001 specification still called for voids in BGA solder joints to be 25% or less of ball X-ray image area, and this applied to lead-free as well as to tin-lead. There was still controversy in the industry as to whether or not voids represented a reliability issue, and Hillman had been given the opportunity to repeat his previous work, this time studying lead-free, in order to derive lead-free BGA solder joint void criteria for submission to the IPC J-STD-001 Committee. Voids were actually very difficult to create deliberately, and it had been necessary to use SAC 387 instead of SAC 305 to encourage their formation. He had succeeded in creating voids up to 42% of X-ray image area, on test vehicles based on BGA 256 packages, with and without via-in-pad. After thermal cycle testing as before, it was significant that none of the joints failed--those with large voids behaved the same as those with no voids at all.
Based on the conclusion that a single set of BGA solder-joint-void process control limits was applicable for both tin-lead and lead-free joints, two options had been presented to the IPC J-STD-001 Committee. Option 1 was to remove the current 25% maximum requirement from J-STD-001, and eliminate it completely; Option 2 was to define a series of actions based on the size of voids and their position within the BGA package footprint. The Committee had discussed the proposal at IPC Midwest in August 2012, but had decided to defer a decision until IPC APEX EXPO 2013…..
SMART Group are once again to be congratulated for organising a truly excellent conference, with a well-constructed programme, papers and presenters of exceptional quality, and a high level of audience participation. Webinars may be the fashion, and they certainly have their place, but nothing can match the real-time opportunity to meet face-to-face with like-minded people, listen to and learn from the experts, and discuss and debate pertinent issues in the electronics manufacturing industry.
More Columns from The European Angle
CircuitData: A New Open Standard for PCB Fab Data ExchangeI Never Realised It Was So Complicated!
The European Angle: Institute of Circuit Technology 43rd Annual Symposium
Ventec International Group's Martin Cotton Celebrates 50 Years in PCB Design
Reporting on the Institute of Circuit Technology Spring Seminar
EuroTech: Raw Materials Supply Chain—Critical Challenges Facing the PCB Industry
EuroTech: ENIPIG—Next Generation of PCB Surface Finish
EuroTech: Institute of Circuit Technology Northern Seminar 2016, Harrogate