-
- News
- Books
Featured Books
- design007 Magazine
Latest Issues
Current IssueProper Floor Planning
Floor planning decisions can make or break performance, manufacturability, and timelines. This month’s contributors weigh in with their best practices for proper floor planning and specific strategies to get it right.
Showing Some Constraint
A strong design constraint strategy carefully balances a wide range of electrical and manufacturing trade-offs. This month, we explore the key requirements, common challenges, and best practices behind building an effective constraint strategy.
All About That Route
Most designers favor manual routing, but today's interactive autorouters may be changing designers' minds by allowing users more direct control. In this issue, our expert contributors discuss a variety of manual and autorouting strategies.
- Articles
- Columns
- Links
- Media kit
||| MENU - design007 Magazine
Estimated reading time: 5 minutes
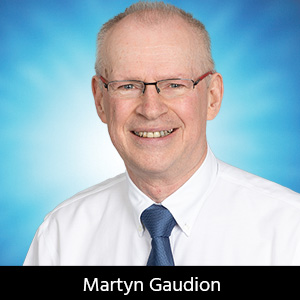
Changing, Yet Changeless
With The PCB Magazine’s request to write a summary of 2012 from a PCB signal integrity perspective, I was immediately taken back to “Sir Henry at Rawlinson End,” a mostly spoken-word, solo comedy recording by the late Vivian Stanshall:
“Changing yet changeless as canal water…”
The last 12 months have seen plenty of change, but the change is matched with repeating technical hurdles that in many cases are easy to jump; but like the whack-a-mole game where the moles keep popping up at random after being knocked back into their holes, the same old questions keep surfacing.
Underlying all of this is the comforting fact that the laws of physics are unchanging. The challenge is that as technology changes, each new technology generation is exposed to a different facet of those laws. The old doesn’t go away, simply depending whether the challenge is low, medium, or high speed, or large, medium, or small geometry; the physics interplays with the physical and the knowledgeable engineer needs to focus on the characteristic most important for the prevailing technology.
Aside from the challenges of signal integrity, and despite turbulent economic times, the talk of onshoring or reshoring does seem--at least, in our customers’ eyes--to be gathering some traction. Many of our customers in Europe and the U.S. seem to be holding their own and in some cases we see capability reappearing, which previously looked as though it was sliding, never to return. In the U.K., the welcome sight of Option Technologies rebuilding its masslam services is a small but welcome visible indication that some rebalancing is afoot. In other areas we hear whispers of skilled people, long thought to have left the industry for good, who are starting to reappear.
Much closer to home, at Polar we have welcomed back Andy Burkhardt after a 10-year interlude in the commercial world; it is good to bring his knowledge back into our industry. Other talk is of companies starting apprenticeships and working with universities to bring in the next generation of specialists. For a long time it was felt that the pendulum had swung too far and now the recognition is growing that both local manufacture and skills base, alongside offshored capability, can lead to a more interesting and commercially balanced future.
Back on the subject of signal integrity, and in the arena of lossless lines (e.g., circuits running up to 2GHz or thereabouts), it is interesting to see how much continuing education is necessary on an ongoing basis; accepted information that I would have imagined had become engrained over the last decade seems to have been lost, and the past year has been one of re-education--on familiar ground. Maybe this just comes down to the fact that, especially in Asia, staff turnover seems to be high in some areas of the PCB industry and the same process has to be repeated for each new intake of staff.
Changing, yet changeless? Well it’s not all quite so straightforward, and though many PCBs still run in the up to 2GHz arena, the relentless drive for smaller geometries sees an increasing number of PCBs, which run at up to these frequencies, where the lines that would have been considered “lossless” are now exhibiting significant DC resistance, and hence what was once considered to be slow enough to be treated as an ideal transmission line now needs to be looked at with more care. These situations tend to exhibit themselves when the TDR traces start to take on a slope as the pulse transitions along the line.
Lean manufacturing is a popular concept right now, and it is helping many companies regain a competitive edge by keeping costs honed razor sharp and to a minimum, allowing competition where once it seemed impossible to compete. As new technologies emerge there needs to be a careful balance between lean and the ability to roll out and test new methods; in the past, most companies had enough wiggle room to allow a few projects that were more research-based, but now the focus is purely on maximising quality output at minimum cost. This presents challenges where technology is changing: Should the R&D costs of rolling out the new process/chemistry/modeling/test methods fall on a) the OEM, b) the supplier, c) the fabricator, or d) should everyone close their eyes and allow hope to be the strategy for rollout of new methods?
Right now we find ourselves in an interesting situation where new technologies are being rolled out in Asia prior to the rest of the world; with previous technologies much of the shake down occurred in the U.S. or Europe, but with the leaned out manufacturing in those areas an interesting situation is occurring where no one is really prepared to accept a “bedding in” period for a new technology. I have found this to be the case in test and modeling environments, and I am sure other suppliers in unrelated areas will also share this dilemma.
IPC standards have seen an active year, and not least of which is IPC-2581 [1]. which proposes a common data format for PCB data transfer and appears to have gained a momentum at the committee level, the likes of which I have never experienced at the IPC. Standards often meander their way towards completion at what seems like a glacial pace. The IPC-2581 committee seems to have life, drive and pace that are rarely experienced in a committed, driven environment. It will be interesting to chart the progress of IPC-2581 during 2013. As always, it would be a positive experience if more fabricators could be persuaded to appear--just to ensure they get their say, as in the long haul fabricators who stand to benefit most from a common and open format.
Last, but not least, let’s get back to signal integrity and insertion losses. This area is growing in interest, and there is an ongoing increase in interest in modeling and predicting insertion losses. Watch for DesignCon [2] papers on this early next year. As interest in measurement also gathers pace, there will likely be lively debate in the industry regarding the tradeoff between measurement techniques, the detail of analysis necessary and the interplay between equipment, probing techniques and coupon design, all of which makes it seem like we have been here before (with the introduction of impedance control). Controlled insertion loss is here to stay and the future is interesting indeed.
References:
1. www.ipc-2581.com.2. www.designcon.com.
Editor's Note: This article originally appeared in the December 2012 issue of The PCB Magazine.
More Columns from The Pulse
The Pulse: Design Constraints for the Next GenerationThe Pulse: Ultra Upgrade Unknowns—What’s Coming for UHDI?
The Pulse: Commonsense Cost Cutting
The Pulse: Overconstraining: Short, Slim, and Smooth
The Pulse: Drilling Down on Documentation
The Pulse: New Designer’s (Partial) Guide to Fabrication
The Pulse: Simplest Stackups Specified
The Pulse: Rough Roughness Reasoning