-
- News
- Books
Featured Books
- pcb007 Magazine
Latest Issues
Current IssueInventing the Future with SEL
Two years after launching its state-of-the-art PCB facility, SEL shares lessons in vision, execution, and innovation, plus insights from industry icons and technology leaders shaping the future of PCB fabrication.
Sales: From Pitch to PO
From the first cold call to finally receiving that first purchase order, the July PCB007 Magazine breaks down some critical parts of the sales stack. To up your sales game, read on!
The Hole Truth: Via Integrity in an HDI World
From the drilled hole to registration across multiple sequential lamination cycles, to the quality of your copper plating, via reliability in an HDI world is becoming an ever-greater challenge. This month we look at “The Hole Truth,” from creating the “perfect” via to how you can assure via quality and reliability, the first time, every time.
- Articles
- Columns
- Links
- Media kit
||| MENU - pcb007 Magazine
Estimated reading time: 7 minutes
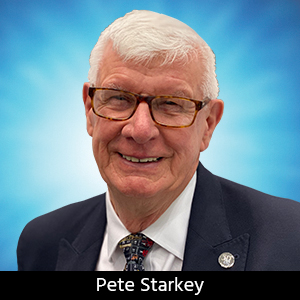
Contact Columnist Form
EIPC Winter Conference: The Keynotes
A truly international event, the 2013 EIPC Winter Conference in Berlin, Germany, was opened by Chairman Alun Morgan who welcomed over 90 delegates from 16 countries to a programme of two keynote speeches and 17 technical presentations with the theme “Specialisation for Added Value – Europe’s Advantage”.
The opening session focused on global business trends in the PCB industry, and Morgan introduced the first of two eminent keynote speakers, Dr. Hayao Nakahara, with his observations on the changing world of the world PCB industry.
Dr. Nakahara reflected upon his many years of association with EIPC and the European PCB industry--he gave his first EIPC conference presentation in 1973--and described how world PCB production, which had been dominated historically by North America and Europe, then by North America and Japan, had in recent years shifted rapidly towards Asia, particularly China. He set out to analyse these changes and to make forecasts for the future.
During the period 2000 to 2011, U.S. domestic PCB output had shrunk to one third of its value, Europe to one half and, taking exchange rates into account, Japan effectively to a half. Meanwhile, China had grown by a factor of 8, South Korea by 3.5 and huge growth was forecast for the South East Asian region. If domestic and overseas production for 2011 were combined, then 31.6% of the £59.2 billion world production came from Taiwanese-owned companies, and 23.6% from Japanese-owned. Dr. Nakahara’s top 20 league table, dominated in 2000 by American and Japanese names, now had five Taiwanese in the top 10, and the highest-placed American company was ninth.
Categorising Chinese PCB manufacturing by ownership, it was clear that Taiwan controlled the majority share with 43.7%. Chinese and Hong Kong companies owned 28.6%, U.S. companies 12.3%, and Japanese 10%.
By comparison with China’s figure of £25 billion, U.S. domestic production in 2011was about $3 billion, and its overseas production about $3.2 billion. Dr .Nakahara believed that domestic production would continue to oscillate in the vicinity of $3 billion per annum unless someone added capacity, which was unlikely. And the European situation was similar to that in the U.S.
Despite many difficulties in China, large investments continued to be made, mostly by Taiwanese and China-Hong Kong manufacturers, although these investments were proceeding at a slower pace than forecast two years ago. Dr. Nakahara presented a long list of new factories and extensions to existing PCB manufacturing plants in China, accompanied by photographs of enormous factory developments, the largest expansions being made by Taiwanese transplants. “At the end of the day, Taiwan’s share in China will be greater than 50% when all these expansions are realised.”
As Japanese electronics OEMs continued to go offshore and entrust manufacture of their products to EMS providers, particularly Taiwan-based EMS companies, PCB imports and exports continue to decline. And PCBs produced outside Japan in the Asia-Pacific region were now good enough to satisfy the notoriously stringent quality requirements of Japanese OEMs.
Domestic laminate production in Japan followed the same trend as PCB production, with almost half of Japanese laminate production now done overseas and only high-end materials still being manufactured domestically.
The Korean PCB industry was heavily dependent on cellphones, with Samsung and LG making more than 25% of world cellphone handsets and continuing to grow at a phenomenal rate. Dr. Nakahara believed that South Korea’s PCB output was unlikely to continue to increase in parallel with cellphone production, as Samsung started to buy more PCBs from non-Korean suppliers.
Taiwan continued to shift to China. “But after China, where next?” he asked. “South East Asia maybe?” Seventy percent of South East Asia’s PCB output was made by Japanese transplants, and Japanese companies continued to make enormous investments, particularly in Thailand, and also in Malaysia, the Philippines, and Vietnam.
How about India and Brazil? Both countries had huge populations, but very poor infrastructure to support PCB manufacture, with no local sources of materials and equipment and everything having to be imported. Particularly in India, chronic shortages of water and electrical power hampered large-scale investment.
Dr. Nakahara’s forecast for world PCB production, assuming constant exchange rates, was for steady growth between 2012 and 2016 from $59 billion to $66 billion, China’s share increasing from 43% in 2011 to nearly 47% by 2016, with half of this owned by Taiwanese companies, and Japanese production declining from about $9.5 billion in 2011 to about $7.5 billion in 2016.
He expected Europe and North America to remain relatively flat, oscillating around $3 billion each during this period. “The western world has technologies, but where is the market? Technology products do not produce a big market.”
It was against this background that Dr. Nakahara handed over the rostrum to Walt Custer, without whose up-to-the-minute business outlook on the global electronics industry no EIPC conference would be complete.
“Do you want comforting lies? I’ll give you the unvarnished truth--ignore it if you want!”
Never short of timely and relevant information, Custer set off at high speed through a series of 100 charts, graphs, and tables analysing supply chain business cycles for electronic equipment, semiconductors and passive components, EMS and ODM companies, PCBs, and process equipment and materials.
European PCB production had declined by about 10% during 2012, and Custer referred to the recent comments of German market analyst Michael Gasch to explain the background: “The general global problems have slowed down the electronic industry considerably. The U.S. debts, political deadlock, and the careful behaviour of consumers, and the debts in Europe and the negative rating of Moody’s and Co. have aggravated the problem for the Mediterranean countries. Reduced FIT for the PV sector reduced purchases of inverters and, consequently, sales of European (predominantly German) PCB manufacturers. The demand for premium cars in Asia had a certain special effect in Germany to electronics, but most of the PCBs in this sector are sourced in Asia. But earlier this year, Germany was able to take advantage of the floods in Thailand as the principal suppliers to the automotive segment (Draco, Fujikura and KCE) were under water and some substantial orders had been transferred to approved suppliers in Germany.”
“The German-speaking countries (Germany, Austria and Switzerland) cover about two thirds of European PCB production. Numbers received so far and the closure of some companies in Germany and Switzerland show a decline of PCB production in these countries of about 10% versus 2011. Especially under-capitalised companies feel the pinch as they have not been able in 2010/11 to overcome the losses of 2009. Switzerland has another problem: the rate of exchange of the Swiss Franc against the US dollar and the Euro makes them less competitive. Nevertheless, the Swiss PCB manufacturers have been successful in keeping their heads above the waterline. France and UK contribute about 7 to 10% each to the European production. Reduced military orders resulted in declining sales for French and UK manufacturers (about 15% less compared to 2011). Nordic and Central European countries have just a limited production; their decline is estimated as well in the region 10 to 15%. Ageing equipment results in lower technology, which consequently meets declining demand.”
Thankfully, the picture was not all gloom and there were some encouraging signs for the future. So far as Europe was concerned, Custer concurred with Dr. Nakahara, predicting that the European PCB industry would stabilise at current levels in the short term. The leading indicators were showing upward trends, although they had not yet passed the zero-growth line and would probably not do so until April or May of this year. Better growth was forecast for 2014.
In his summing-up, Custer commented that there was modest recovery in South East Asia and the U.S., but that the electronics industries in Europe and Japan were still struggling. The global leading indicators were pointing up, although capital equipment recovery would lag electronic equipment, components and materials by about six months. Major issues were Europe’s tighter fiscal policies, squeezed consumer purchasing power and sovereign-debt tensions. The U.S. had to contend with debt, high unemployment, and political wrangling. China was experiencing rising costs, labour unrest and weaker exports. Japan had a combination of weak domestic demand and a strong Yen that was hurting exports.
He suggested that individual companies could gather their own historical monthly data on key product lines, identify coincident and leading indicators, and use these to make meaningful forecasts of future sales.
The keynote session concluded with Alun Morgan stepping forward not only to thank both presenters heartily on behalf of the EIPC board, but also to acknowledge their commitment and long-term support by bestowing Honorary Fellowship of the Institute on each of them, presenting plaques and certificates in recognition of their wisdom and dedication.
More Columns from The European Angle
CircuitData: A New Open Standard for PCB Fab Data ExchangeI Never Realised It Was So Complicated!
The European Angle: Institute of Circuit Technology 43rd Annual Symposium
Ventec International Group's Martin Cotton Celebrates 50 Years in PCB Design
Reporting on the Institute of Circuit Technology Spring Seminar
EuroTech: Raw Materials Supply Chain—Critical Challenges Facing the PCB Industry
EuroTech: ENIPIG—Next Generation of PCB Surface Finish
EuroTech: Institute of Circuit Technology Northern Seminar 2016, Harrogate