-
- News
- Books
Featured Books
- pcb007 Magazine
Latest Issues
Current IssueInventing the Future with SEL
Two years after launching its state-of-the-art PCB facility, SEL shares lessons in vision, execution, and innovation, plus insights from industry icons and technology leaders shaping the future of PCB fabrication.
Sales: From Pitch to PO
From the first cold call to finally receiving that first purchase order, the July PCB007 Magazine breaks down some critical parts of the sales stack. To up your sales game, read on!
The Hole Truth: Via Integrity in an HDI World
From the drilled hole to registration across multiple sequential lamination cycles, to the quality of your copper plating, via reliability in an HDI world is becoming an ever-greater challenge. This month we look at “The Hole Truth,” from creating the “perfect” via to how you can assure via quality and reliability, the first time, every time.
- Articles
- Columns
- Links
- Media kit
||| MENU - pcb007 Magazine
Estimated reading time: 7 minutes
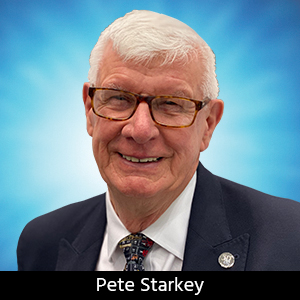
Contact Columnist Form
An Inside Look: UK's ICT Arundel Seminar
The Annual General Meeting (AGM) of the Institute of Circuit Technology (ICT) was held in the historic market town of Arundel, in the South Downs of West Sussex, England, famous for its castle and cathedral. The AGM was followed by a very well attended evening seminar, which included updates from two RTD partners in the ASPIS FP7 project, a look at developments in re-usable electronics, and a user view of a revolutionary solderable finish.
After a welcome and introduction by ICT Chairman Professor Martin Goosey, who commented that the Institute, now in its 39th year, had seen its membership exceed 300, despite the contraction of the UK PCB industry and its supply chain over the past decade, the first presentation was given by Tim Gee, technical director of Stevenage Circuits. His company was the first European PCB fabricator to install Semblant’s innovative SPF nanofinish, and were cooperating in Semblant’s Premier Partner programme, to facilitate quick-turn evaluation, prototyping, and production for OEMs in high-reliability product segments.
Gee considered that SPF brought a totally new perspective to solderable finishing and long-term protection of PCBs. It was applied by a dry, room-temperature plasma polymer deposition process, which resulted in microscopically thin coating of an unreactive, highly cross-linked fluoropolymer. The process was pervasive and coated the entire surface area, giving unprecedented environmental protection and shelf life. The process was capable of high-volume operation at low unit cost, involved no hazardous waste or conflict metals, consumed no water, and had minimal energy requirements
He explained the principles of operation of the plasma deposition system, commenting that the equipment was ready for use only one minute after switching on. Deposit thickness was between 40 and 50 nanometers, and was measured using a Fourier Transform infra-red spectrophotometer.
SPF could be used as a protective solderable finish in its own right by applying it directly over bare copper, or could be applied over existing metallic finishes such as immersion silver and electroless nickel immersion gold to enhance their shelf life. The finish had “solder-through” capability--it was displaced as the solder wetted the underlying metal, but was robust enough to maintain solderability through multiple reflow operations.
Gee showed the results of a wide range of third party corrosion tests, which demonstrated the remarkable protective capability of SPF.
Several of Stevenage Circuits’ customers specialised in RF work and were particularly concerned with minimising signal losses through the “skin effect.” Electroless nickel immersion gold finishes did not perform well in RF applications. Immersion silver had more suitable characteristics, but its corrosion resistance was limited. However, immersion silver coated with SPF gave very favourable performance.
Although Stevenage Circuits’ primary interest in SPF was as a solderable finish, Semblant had also developed a range of associated products for conformal-coating applications, applied by the same plasma-ploymerisation process with no masking required, which had many advantages over traditional coatings.
Dr. Chris Hunt, who leads the Electronics Interconnection Group at the National Physical Laboratory (NPL), discussed a novel application of printed electronics principles to improve electronics sustainability, reporting the progress of the TSB-supported ReUSE project. The project needed little justification, considering that an estimated 100 million electronic units were discarded annually in the UK alone, that 85% of scrap PCB assemblies ended up in landfill, and that most of this was non-metallic substrate material that offered little opportunity for recycling.
The ReUSE project aimed to develop reusable, unzippable, sustainable electronics interconnection technology, with circuits based on recyclable thermoplastics and rigidisers, with special polymer layers and binders designed to allow straightforward, end-of-life disassembly with easy reuse and recycling.
One of several demonstrators that had been constructed was an inverter assembly for an electroluminescent lamp, which consisted of a thin flexible circuit assembled with standard tin-finished components by normal SMT techniques using an isotropic conductive adhesive and bonded to a rigid base. This assembly had been extensively tested for reliability, with satisfactory results.
Dr. Hunt showed a video illustrating how, at nominal end-of-life, a simple immersion in hot water allowed the assembly to be “unzipped,” the components removed without damage to leads or terminations and the flex circuit separated from the rigid base. He believed that recovery levels in typical assemblies would be improved to at least 90%, and that the ReUSE technology would lend itself readily to rigid, flexible and 3D structures.
Dr. Andy Ballantyne from University of Leicester gave the first of the two presentations on the ASPIS project. His research group specialised in exploring applications for ionic liquids and were evaluating immersion gold processes based on ionic-liquid chemistry as a potential means of overcoming the hyper-corrosion effects observed when aqueous gold chemistries were used in the ENIG process.
Ionic liquids were typically composed of organic cations with halide anions. They differed from molecular solvents, particularly with metal salts, where they exhibited unusual solvation properties and changed their electrochemical behaviour. The ionic liquid used in this investigation was known by the proprietary name Ethaline 200, made from ethylene glycol and choline chloride in a 2:1 molar ratio. The components were environmentally benign and readily available.
A series of immersion gold formulations had been prepared, using Ethaline 200 and gold in the form of gold chloride AuCl, gold cyanide AuCN and potassium gold cyanide KAu(CN)2 . These had been used to deposit gold on electroless nickel plated from a standardised laboratory formulation. Plating rates had been measured using a quartz crystal microbalance technique, and surface morphology studied with scanning electron microscopy and atomic force microscopy. The deposits had been examined visually and tested for solderability with a wetting balance. Nickel corrosion effects had been studied and compared with the equivalent effects when gold was deposited from aqueous chemistries.
The gold chloride based solution had not given good results, but results from the cyanide-based solutions were more encouraging. It had been observed that AuCN gave bright uniform coatings, KAu(CN)2 gave comparatively thin coatings and that increasing cyanide content improved coating quality, but decreased deposition rate. The roughness of deposits from ionic liquids was less than the equivalent from aqueous solutions, and there was less evidence of corrosion of the electroless nickel.
Soldering tests had indicated that coatings from ionic liquids wetted faster and more reliably than those from the aqueous reference process. It had been shown that certain additives designed to activate electroless nickel surface could have a dramatic impact on coating morphology, and this was being studied further.
The final presentation came from Chris Fisher, a specialist corrosion scientist from ITRI, who had been studying some fundamental aspects of electroless nickel deposition to determine the causes of the hyper-corrosion effect in ENIG processing. Proprietary electroless nickels all had a tendency to deposit with a cellular morphology, and the inter-cellular regions were points of weakness.
For purposes of development work, non-proprietary formulations had been selected, and these had been verified against commercial PCBs produced by SME partners in the ASPIS project. The absence of unidentified additives allowed changes to be made more easily and effects of individual modifications to be isolated. Several variations had been produced to control certain parameters such as deposit chemistry, plating rate, stabiliser type, and a scaled-up pilot line had been built to enable the production of larger sample quantities.
The modification strategy had been to reduce the tendency for the immersion gold process to produce concentrated attack, to adjust the chemical properties of the nickel deposit to decrease the risk of concentrated corrosive attack, to increase the inter-cellular boundary volume to disperse the attack, and to eliminate inter-cellular boundaries to prevent attack. The most obvious method was to increase phosphorous content. Although other elements or compounds might also have beneficial effect, most had been reported to be detrimental for other ENIG functionality. It was well known that increasing phosphorus content would improve corrosion resistance, although this might reduce solderability and increase the risk of brittle joints.
It had been found that the phosphorus content of coatings produced by a range of temperatures and pH’s resulted in coatings with minimal differences in phosphorus content, and that addition of lactic or acetic acid increased deposition rate but did not change phosphorus content.
The morphology and characteristics of the coatings were dependent on nucleation events and subsequent growth, and it was hypothesised that if nucleation or growth could be altered then a more resilient microstructure could be developed. Electrolytic nickel growth was initiated by catalytic treatments, and the coating characteristics were partially determined by the condition of the underlying substrate. It was suggested that reducing the size of the nickel deposit cells could have beneficial effects, and that reducing the ratio between intracellular and inter-cellular region would reduce the driving force for differential attack. A larger area would distribute the necessary corrosive attack required for the immersion gold process, avoiding maximum level of attack being experienced in any one location.
Studies of copper pre-treatments and activation methods had shown that increasing the nucleation rate of nickel deposition was difficult, and might prevent sufficient size reduction in deposit cells to produce positive effects. Inhibiting nickel nucleation was possible and boundary-free nickel deposits could be produced, but a low-energy nucleation additive inhibitor was needed, and investigations were now proceeding in this direction.
ICT Technical Director Bill Wilkie brought proceedings to a close, thanked presenters for their contribution and delegates for their attention, and the ASPIS project for supporting the event.For more information, visit www.aspis-pcb.org and www.instcp.org.
More Columns from The European Angle
CircuitData: A New Open Standard for PCB Fab Data ExchangeI Never Realised It Was So Complicated!
The European Angle: Institute of Circuit Technology 43rd Annual Symposium
Ventec International Group's Martin Cotton Celebrates 50 Years in PCB Design
Reporting on the Institute of Circuit Technology Spring Seminar
EuroTech: Raw Materials Supply Chain—Critical Challenges Facing the PCB Industry
EuroTech: ENIPIG—Next Generation of PCB Surface Finish
EuroTech: Institute of Circuit Technology Northern Seminar 2016, Harrogate