-
- News
- Books
Featured Books
- pcb007 Magazine
Latest Issues
Current IssueInventing the Future with SEL
Two years after launching its state-of-the-art PCB facility, SEL shares lessons in vision, execution, and innovation, plus insights from industry icons and technology leaders shaping the future of PCB fabrication.
Sales: From Pitch to PO
From the first cold call to finally receiving that first purchase order, the July PCB007 Magazine breaks down some critical parts of the sales stack. To up your sales game, read on!
The Hole Truth: Via Integrity in an HDI World
From the drilled hole to registration across multiple sequential lamination cycles, to the quality of your copper plating, via reliability in an HDI world is becoming an ever-greater challenge. This month we look at “The Hole Truth,” from creating the “perfect” via to how you can assure via quality and reliability, the first time, every time.
- Articles
- Columns
- Links
- Media kit
||| MENU - pcb007 Magazine
Estimated reading time: 10 minutes
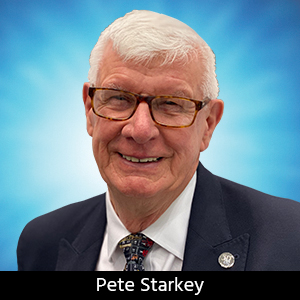
Contact Columnist Form
EIPC Winter Conference: Specialization - Europe's Advantage, Part II
Editor's Note: This is the second half of Pete Starkey's report on the EIPC Winter conferece. Over 90 delegates from 16 countries attended the 2013 EIPC Winter Conference in Berlin, Germany, to exchange information on market conditions and future innovations in interconnection and packaging.Session Three of the conference was moderated by Pete Starkey, and included five presentations on aspects of novel plating and patterning processes.
First to speak was Jacko Pijper from Magneto Special Anodes in the Netherlands, who explained the benefits of insoluble titanium anodes for sustainable copper plating in PCB manufacture. Coated titanium anodes had many applications in metal finishing, corrosion protection, and water treatment, and in reference to PCB manufacture were used in copper foil production and increasingly in copper panel plating and pattern plating, especially in horizontal plating lines. Their main advantages over soluble anodes were constant geometry and reduced additive consumption, leading to cost savings and improved process control.
Pijper explained that titanium was actually a very reactive metal, but rapidly formed a protective oxide layer. To make it function as an anode, it was coated with a mixed-metal-oxide formulation, typically containing oxides of tantalum and iridium. This formulation was prepared in the form of a paste in alcohol, applied as a very thin coating to the prepared titanium surface, then dried and stoved at temperatures of 400 to 600ºC, taking on a “mud-cracked” structure. The coating was then built up in a series of layers, between 10 and 60 coat-dry-stove operations, depending on the particular application and customer requirement. The coated anodes were typically mounted on carrier frames with bus-bar connections. Strict quality control and traceability procedures were observed.
In addition to the benefits of constant geometry and reduced brightener consumption, mixed-metal-oxide coated anodes gave savings in handling and metal costs and reduced production downtime.
Dennis Price, from Merlin Circuit Technology in the UK, had been working with Heriot-Watt and Greenwich Universities on a project named ASPECT, studying the effects of megasonic agitation in the fabrication of high-aspect-ratio blind microvias. Megasonics was a form of ultrasonics, but operating at higher frequencies and giving a gentler action, with less destructive cavitation effects. The objective of the project was to reduce the number of sequential bonding operations required to build complex microvia designs. The example he showed was a 26-layer board for a defence application, and the manufacturing process involved six bonding and 10 drilling operations. The principle of the proposed alternative process was to mechanically drill blind microvia holes to various depths to achieve layer-to-layer interconnection in a single operation, rather than through a series of drill, plate, and build-up stages. But this depended on having the ability to reliably metallise and electroplate high aspect-ratio blind holes, and conventional solution agitation was not adequate to guarantee consistent results. Megasonic agitation had been evaluated and had proved to facilitate the break-up and extraction of entrapped air bubbles and gave continuous ion replacement in the electrolyte solution. The resultant copper deposition was void-free and met the requirements of IPC specifications. Elegant methods had been developed for modelling, observing and measuring the flow of solution in and around the via holes.
Professor Martin Goosey kindly stepped in on short notice to deliver the presentation of Professor Sudipta Roy, who was unable to attend the conference. The topic was a maskless electrochemical surface modification process known as EnFACE--an abbreviation for electrochemical nano and micro fabrication using novel chemistry and engineering--which had been developed within the EU-funded MESMOPROC project. The process used a specialised electrochemical reactor for the transfer of micro-scale patterns onto bare substrate with no photolithographic resist image. Instead, the resist pattern was placed on the tool, with the bare substrate in close proximity. The tool and substrate were connected to an electrical power supply and electrolyte was pumped through the system to deliver fresh chemistry to anode and cathode and to remove reaction by-products. Metal was selectively plated onto or etched off the substrate depending on the polarity of the power supply, and a single tool could be used for many pattern transfer operations, greatly reducing the cost and time of photolithographically imaging individual substrates.
The technique had been used to fabricate micron-scale structures of copper and nickel on metallic substrates using bench-scale apparatus, and process parameters for effective pattern transfer had been determined from modelling experiments.
The two presentations that concluded the session concerned direct imaging processes and two different viewpoints were addressed
Karel Tavernier from Ucamco in Belgium described the application of a multi-wavelength approach to the direct imaging of standard photoresists and solder masks. Two major concerns in the selection of a direct imaging system were whether it was possible to achieve good performance and throughput on conventional resist and whether the same machine could also expose solder mask and achieve a good throughput whilst effectively polymerising the whole thickness of the material and not just the surface. The equipment he described had been developed in Japan by Dainippon Screen, using an optical design based on UV-LEDs, with two arrays of different wavelength which could be modulated independently, generating a wavelength pattern comparable to that of a mercury lamp, but which could be tuned to enable optimised exposure of almost any resist or solder mask with high quality and high throughput.
Solder mask was particularly difficult to expose with a single-wavelength light source, because of differences between its absorption and transmission characteristics. There was a tendency for the surface to become polymerised but then prevent light from penetrating into the body of the material and completing the polymerisation through its thickness. Having two individually tuneable wavelengths overcame this problem and enabled the competing requirements to be satisfied. As a practical illustration of his point, Tavernier showed photographs of two hamburgers which appeared identical until cut in half to reveal that one was “medium-rare” whilst the other was “well-done.”
Uwe Altmann from Orbotech in Belgium described the advantages of large-scan optics, as used in all of Orbotech’s 750 laser direct imaging installations world-wide, over systems based on digital micro-mirror devices, of which the Dainippon Screen equipment described by Karel Tavernier was an example. Orbotech’s large-scan optics employed a single UV laser source and a long optical path, and the exposure was completed in a one-pass scan, which gave benefits in beam quality, resolution, accuracy, and depth of focus, leading to advantages in line and edge uniformity. Because digital micro-mirror systems used multiple heads, alignment was critical and temperature changes could lead to misalignment and stitching errors between overlaps. And there was a possibility that light intensity could vary between individual heads. The wide depth of focus of the large-scan optics system gave greater tolerance to variations in surface topography, and this was of particular relevance in flexible circuit manufacture.
Pete Starkey moderated a lively question-and-answer panel discussion as the relative merits of the two competing systems were debated.
The final conference session was entitled “Advanced Technologies – Pushing the Boundaries,” and was moderated by Oldrich Simek from Pragoboard in Czech Republic.
Les Round from Spirit Circuits in the UK discussed requirements of PCBs in solar and LED applications. He explained that, at the PCB level, a range of thermal management solutions was available and that fabricators should be prepared to advise on the best options based on performance versus cost. He reviewed available materials and popular design concepts, then described the characteristics of Nanotherm, a proprietary insulated metal substrate in which alumina ceramic was formed electrolytically on an aluminium base material, and copper deposited on to the ceramic so that the circuit could be formed directly without any additional dielectric, resulting in very low thermal resistance. He went on to list a series of different metal-core PCB solutions, including chip-on-board MPCB, which could be fabricated by bonding or milling routes and enabled the heat source to me mounted direct on the metal heat sink, and hybrid post-bonded MPCBs.
Round concluded by advising that IMS substrate materials were relatively expensive and that the choice of panel sizes was limited. Therefore it was important that designers worked closely with fabricators at the earliest stage to ensure best material utilisation from standard panels.
Lars Boettcher from Fraunhofer IZM in Germany then reviewed the development of embedded high-power electronics modules. He explained that the automotive industry had a strong demand for highly-reliable and cost-effective electronics and that the upcoming generations of hybrid cars and fully-electric vehicles needed compact and efficient 400V power modules. Space was a major concern, therefore small size and high level of integration of these modules was necessary. Conventional IGBTs and diodes were soldered to direct-copper-bond ceramic substrates and their top contacts were connected by heavy aluminium wire-bonds. Then the ceramic modules were vacuum-soldered to water-cooled base plates. Embedding of power switches and controller into compact modules using PCB technologies offered the potential to further improve the thermal management by double-sided cooling and reduction of the thickness of the module.
To replace direct-copper-bond ceramics, a structure of thermal laminate material between thick copper layers had been developed and the capability for thermal conduction and electrical insulation had been evaluated. New silver sintering pastes had been assessed for mounting large ICBTs. These enabled pressure-less sintering at 200ºC, compatible with PCB materials. Extremely heavy copper tracks were required to handle switching currents up to 200A, which necessitated some innovative fabrication procedures.
The chip embedding technique had become established as a mature technology, and the first low-power system-in-package modules were being manufactured in volume.
The next paper also concerned embedded technology, this time the embedding of RFID chips in PCBs, and was presented by Jeni Spillane from Graphic PLC in the UK. Graphic were working in collaboration with University of Exeter to develop embedded RFID technology that could be applied to different board designs with minimal requirement for redesign. The technology could be used for applications including traceability, secure tracking, technical data storage, counterfeit detection, stock control, and through-life monitoring.
Graphic had started from first principles, with a proprietary RFID tag known as the Alien “Squiggle” inlay and a standard multilayer bonding process. Initial yields had been low because of cracking of the chip, and the bonding process had been progressively refined until 100% yields had been achieved. Further development had been carried out using Alien “Strap” devices, embedding chips and attaching them to antennae. Quinetiq were cooperating in the design of suitable antennae to give improved read ranges.
The conference finished on a “green” environmental note, with the final presentation given by Karsten Shischke from Fraunhofer IZM in Germany, entitled “Environmental Assessment of Printed Circuit Board Production to Support Design Decisions and Facilitate Carbon Footprinting of Electronics Products.” Acknowledging the challenges faced by small and medium PCB manufacturers in providing environmental data on their production processes in a consistent manner and without revealing confidential information, and the fact that designers had no means of determining the likely production impacts of their design decisions, an FP7 project known as “LCA to go” aimed to provide a modelling method. The project was currently researching a streamlined data model to calculate selected environmental parameters such as carbon footprint, energy, and water consumption, based on technical production parameters. A comprehensive assessment of the usage of energy, water, chemicals, and materials for most common layer counts and surface finishes had been undertaken by project partners ITR and Polish PCB manufacturer ELDOS to calculate impacts per technology. The results had been used as the basis of a parameterised model for designers and specifiers of PCBs, and a model framework for use by other PCB manufacturers to establish customised environmental data inventories based on their own production data. These models would be made available as free web tools for SMEs to use to provide data for their customers.
Alun Morgan brought the conference to a close and gave his warm thanks to all who had participated and contributed.
I run out of superlatives when summing up EIPC conferences. They are consistently the highest standard in terms of content and organisation. The Berlin event was no exception: A carefully chosen and well-balanced programme, premier-division presenters, an interesting venue, the opportunity to visit world-class laboratory facilities. And all seamlessly and faultlessly organised by the ever-smiling and totally unflappable Sonja Derhaag and Kisten Smit-Westenberg. Just excellent.
More Columns from The European Angle
CircuitData: A New Open Standard for PCB Fab Data ExchangeI Never Realised It Was So Complicated!
The European Angle: Institute of Circuit Technology 43rd Annual Symposium
Ventec International Group's Martin Cotton Celebrates 50 Years in PCB Design
Reporting on the Institute of Circuit Technology Spring Seminar
EuroTech: Raw Materials Supply Chain—Critical Challenges Facing the PCB Industry
EuroTech: ENIPIG—Next Generation of PCB Surface Finish
EuroTech: Institute of Circuit Technology Northern Seminar 2016, Harrogate