-
- News
- Books
Featured Books
- pcb007 Magazine
Latest Issues
Current IssueInventing the Future with SEL
Two years after launching its state-of-the-art PCB facility, SEL shares lessons in vision, execution, and innovation, plus insights from industry icons and technology leaders shaping the future of PCB fabrication.
Sales: From Pitch to PO
From the first cold call to finally receiving that first purchase order, the July PCB007 Magazine breaks down some critical parts of the sales stack. To up your sales game, read on!
The Hole Truth: Via Integrity in an HDI World
From the drilled hole to registration across multiple sequential lamination cycles, to the quality of your copper plating, via reliability in an HDI world is becoming an ever-greater challenge. This month we look at “The Hole Truth,” from creating the “perfect” via to how you can assure via quality and reliability, the first time, every time.
- Articles
- Columns
- Links
- Media kit
||| MENU - pcb007 Magazine
Estimated reading time: 5 minutes
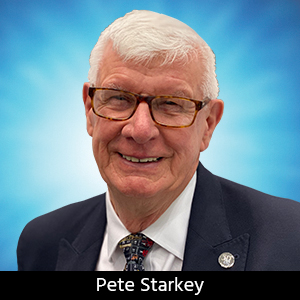
Contact Columnist Form
Semblant at Stevenage: The SPF Process Up Close
I first got to know about Semblant and its SPF technology during a conversation with Semblant Chief Technology Officer Tim Von Werne at IPC APEX EXPO 2011 in Las Vegas and since then I have taken every opportunity to follow the technology's progress in the market.
SPF is an ultra-thin surface finish for PCBs, based on fluorocarbon chemistry, which is polymerised in-situ in a plasma chamber. It can be used as a protective solderable finish in its own right by applying it directly over bare copper, or it may be applied over existing metallic finishes such as immersion silver and electroless nickel immersion gold to enhance their shelf life. The finish has “solder-through” capability, it is displaced as the solder wets the underlying metal, but is robust enough to maintain solderability through multiple reflow operations.
When it was announced in September 2012 that Semblant had formed a working partnership with Stevenage Circuits in the UK, the first European PCB fabricator to install and operate the SPF process commercially, to facilitate quick-turn evaluation, prototyping, and production for OEMs in the high-reliability electronics sector as part of Semblant’s Premier Partner programme, I keenly awaited the chance to take a look at the process in real life.
Stevenage Circuits’ Technical Director Tim Gee gave a presentation on SPF to the Institute of Circuit Technology at a seminar in Arundel, UK, February 6, 2013, explaining that it brought a new perspective to solderable finishing and long-term protection of PCBs, coating the entire surface area, and giving unprecedented environmental protection and shelf life. The process was capable of high-volume operation at low unit cost, involved no hazardous waste or conflict metals, consumed no water, and had minimal energy requirements. He showed the results of a wide range of third-party corrosion tests, demonstrating the remarkable protective capability of SPF.
Recognising my interest in solderable finishes in general, and my desire to learn about his practical experiences with SPF, Gee invited me to visit the Stevenage Circuits factory to see the process first hand. And that’s how I came to be standing in front of the Semblant plasma-deposition unit, an unspectacular-looking big grey box with a control panel and an access door at the front, a chiller unit, some gas bottles and regulators behind, and a PC for process monitoring and data recording alongside.
Well-experienced in operating plasma equipment--Stevenage already has two machines in production for de-smearing multilayers and activating PTFE--Gee explained the principles of operation of the SPF system. Start-up time was minimal, the unit was ready to use within one minute of initial switch-on, and cycle time was 20 minutes total per batch. The work was racked horizontally between arrays of RF electrodes, the chamber was pumped down to high vacuum, a charge of reactive gas was admitted and brought to an excited state by a high frequency discharge, then chemically modified molecules deposited on the surface of work. The actual chemistry was complex, but the practical result was a pervasive coating of inert, highly cross-linked fluoropolymer over the entire surface area.
The whole system was kept cool by circulating water from the chiller. At the end of the cycle, the chamber was purged with nitrogen, the door was opened and the work was removed. As a periodic maintenance routine, the chamber was cleaned by running a cycle with oxygen plasma. Deposit thickness was between 40 and 50 nanometers, which was measured using a Fourier Transform infrared spectrophotometer.
One small bottle of gas, although expensive to buy, was sufficient for approximately 1,000 cycles, and Stevenage’s chamber could accommodate 12 panels 18” x 12”. Gee pointed out that much higher-capacity equipment was available from Adeon B.V. who are the appointed European agent for March plasma machines, March being the sole equipment supplier for the Semblant process.
For copper surfaces, Stevenage used the same surface preparation procedure as for inner layers, a peroxide-sulphuric microetch, followed by thorough DI rinsing and drying.
The initial interest in SPF was as a solderable finish for copper, and it had shown remarkably good soldering performance through multiple reflows without any modification to normal SMT assembly parameters, pastes, or fluxes. To fully characterise and optimise its performance in production, Stevenage was engaged in cooperative exercises with EMS customers and flux suppliers. Also, to introduce the finish to existing customers, the strategy was to supply a few over-makes treated with SPF alongside a normal delivery, and to offer applications-engineering support to monitor them through assembly.
As Gee explained, applications engineering was key to developing the market for SPF. As well as being an excellent solderable finish for copper, it had been found to extend the shelf life and corrosion resistance of other metallic finishes. A particular case in point applied to RF and microwave work, where Stevenage had a long-established identity. Electroless nickel immersion gold finishes did not perform well in these applications because of signal losses through the “skin effect”. Immersion silver had more suitable characteristics, but its corrosion resistance was limited. However, immersion silver coated with SPF offered the ideal compromise. Similarly, the shelf life of immersion tin could be substantially extended.
Another observed property of SPF was its ability to restrict the flow of flux during reflow soldering. Flux residue remained on the solder, rather than spreading across the surface of the solder mask. On certain designs where the presence of solder mask detracted from electrical performance, or where the design pitch was so fine that it was impracticable to resolve minute solder dams, this could be offer significant advantages.
Stevenage had embarked upon a programme of workshops and roadshows to introduce the practical benefits of Semblant SPF to their OEM, CEM and EMS customers. Stevenage being able to offer a sub-contract service for coating boards or samples with the SPF process is helping interested parties gain access to the process, thus gaining further confidence. The initial responses had been encouragingly positive, although Gee was under no illusion that it would be an easy task to get the finish widely acknowledged, accepted, and qualified. But I think that will just be a matter of time, patience, and hard work.
More Columns from The European Angle
CircuitData: A New Open Standard for PCB Fab Data ExchangeI Never Realised It Was So Complicated!
The European Angle: Institute of Circuit Technology 43rd Annual Symposium
Ventec International Group's Martin Cotton Celebrates 50 Years in PCB Design
Reporting on the Institute of Circuit Technology Spring Seminar
EuroTech: Raw Materials Supply Chain—Critical Challenges Facing the PCB Industry
EuroTech: ENIPIG—Next Generation of PCB Surface Finish
EuroTech: Institute of Circuit Technology Northern Seminar 2016, Harrogate