-
- News
- Books
Featured Books
- pcb007 Magazine
Latest Issues
Current IssueInventing the Future with SEL
Two years after launching its state-of-the-art PCB facility, SEL shares lessons in vision, execution, and innovation, plus insights from industry icons and technology leaders shaping the future of PCB fabrication.
Sales: From Pitch to PO
From the first cold call to finally receiving that first purchase order, the July PCB007 Magazine breaks down some critical parts of the sales stack. To up your sales game, read on!
The Hole Truth: Via Integrity in an HDI World
From the drilled hole to registration across multiple sequential lamination cycles, to the quality of your copper plating, via reliability in an HDI world is becoming an ever-greater challenge. This month we look at “The Hole Truth,” from creating the “perfect” via to how you can assure via quality and reliability, the first time, every time.
- Articles
- Columns
- Links
- Media kit
||| MENU - pcb007 Magazine
Estimated reading time: 12 minutes
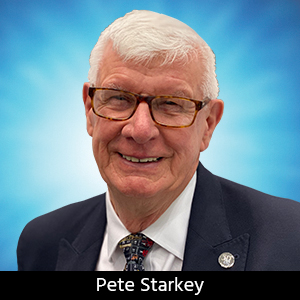
Contact Columnist Form
An Inside Look: SMART Group European Conference 2013, Day 1
Since the 16th Century the Spread Eagle Hotel, in the vibrant and historic market town of Thame in Oxfordshire, UK has been hosting eminent guests, King Charles II perhaps being the most famous. This year it once again hosted SMART Group’s European Conference, eminent guests from the electronics manufacturing community travelling from far and near to network with their peers and increase their understanding of material and process selection and yield improvement techniques.
The conference was opened by SMART Chairman Keith Bryant, who welcomed delegates and introduced a stimulating programme of 16 presentations covering a broad and relevant topic range. How relevant was it that the initial presentation came from the bank manager? Fundamentally relevant! Whatever your technical knowledge, how can you drive your business forward if you can’t finance expansion?
Richard Holden, head of manufacturing at Lloyds Bank, gave a frank and informative explanation of the bank’s role in supporting UK manufacturing industry. Admitting that the recent media profile of banks had been far from positive, he made it clear that his intention was not to apologise or defend, but to describe what actions Lloyds had taken to gain a real understanding of manufacturing. Typical manufacturer’s perception had been that banks did not understand manufacturing, and their managers were not sufficiently knowledgeable about investment cycles and supply chains, or why manufacturers needed access to asset-backed and export finance.
Lloyds responded by developing a manufacturing training programme, in cooperation with the Engineering Employers Federation, the Manufacturing Technologies Association and Warwick Manufacturing Group. 170 of their managers had already attended a five-day course at Warwick University and there was an ongoing commitment to improve managers’ understanding through training and continued professional development. Holden was realistic enough to acknowledge that his managers were not experts, although they did have a good knowledge of local manufacturing businesses and continued to work with internal and external partners and specialists to provide them with support and guidance.
Quoting figures as illustration, he indicated that the bank’s net lending to SMEs has grown 5% year-on-year against a net reduction of 3% across the industry, that managers had £500,000 local lending authority, that eight out of 10 overdraft and loan requests were approved, and that more than £24 billion in gross funds had been committed under the Government’s Funding for Lending scheme.
Acknowledging that overall there was optimism that the economy was showing early, but real, improvement, Holden was conscious of future challenges that would hinder sustainable growth, skills shortage being a major issue. He believed that the Government had a big role to play in the industrial strategy of the UK which would help grow the UK manufacturing sector and rebalance the economy. And this approach would need to be consistently applied over many years regardless of which party was in power.
“Raspberry Pi: the Benefits of Onshoring” was an encouraging and inspiring case history from Gareth Jones, senior manager at Sony’s UK Technology Centre at Pencoed in South Wales. Sony had been one of the early inward investors in the UK electronics industry, but, sadly, one of very few remaining. Jones gave a then-and-now comparison of how a leading manufacturer of CRT colour televisions saw the market overtaken by flat screen technology and made the decision to survive by diversification, learning a lot of new skills in the process. From sausage-machine mass production to the manufacture of professional specialist broadcast equipment: Complex, low-volume product which required multi-high skills in production, service, and support. The UK Technology centre also offered collaborative manufacturing services, education media solutions and business incubation opportunities.
Looking at the potential benefits of reshoring, he first made it clear that there was no one-size-fits-all universal solution; every case needed to be considered individually. But there were some general factors such as increasing unit cost due to wage inflation, a long in-flexible supply chain which was expensive to fund, poor delivery achievement due to labour instability, and high cost of engineering support and supervision.
Jones recounted the Raspberry Pi story. The product was a low-cost mini-computer platform designed to encourage young people to develop programming and engineering skills. Manufacturing had been contracted to Chinese EMS companies in the expectation of low unit cost. In reality, this proved to be an expensive mistake. There were major supply problems, the launch was disrupted and the first 10,000 units had to be reworked. Sony took over manufacture in July 2012 and had made over a million units to date, with failures at the low parts-per-million level, and no substantial increase in total cost.
There were some areas of caution in re-shoring: Local supply chain limitations, investment considerations, demand fluctuations, and cost pressure, but on the positive side were excellent public relations benefits in marketing and manufacturing image. In Sony’s case, they also made the most of the opportunity to engage the next generation, by encouraging factory visits from schools and demonstrating that engineering and manufacturing had moved beyond the oily-rag image of the past, and now presented exciting career prospects.
Professor Martin Goosey, industrial director of the Innovative Electronics Manufacturing Research Centre (IeMRC), examined the challenges of environmental legislation and resource utilisation, and discussed whether these presented threats or opportunities for the electronics industry. He stated that since the 1990s there had been a growing realisation that the electronics industry used materials that were both toxic and potentially harmful to the environment, and growing pressure from consumers to make products safer and more environmentally benign. Large quantities of waste electrical and electronic equipment were generated in Europe and the rest of the world and there was an overall desire to adopt more sustainable approaches, and a need to recover and reuse more materials.
With reference to the toxic materials identified in the RoHS regulations, he quoted Paracelsus, the German-Swiss physician and alchemist of the Middle Ages: “All things are poison, and nothing is without poison; only the dose permits something not to be poisonous.” Lead had already been banned as a fuel additive and in applications such glasses and paints, brominated flame retardants were persistent in the environment, hexavalent chromium was a known carcinogen, mercury was long known to be toxic, and cadmium was more toxic than lead or mercury.
The key impact of RoHS on the electronics industry had been on lead, as lead-containing solders had been in common use in most electronics assembly operations. It was an interesting fact that in 2002, the actual usage of lead in solder had been less than 0.5% of total world consumption. And lead was relatively easy to recover and recycle. Nevertheless, the cost to the electronics industry of initial compliance with the RoHS Directive had been estimated at $32 billion and component, module and manufacturing costs had increased by an average of 12%, with companies reporting lost sales averaging $1.84 million, due to delays in new product sales and lost business in the EU. The average cost per company was $2.64 million to achieve initial compliance, and another $482,000 to maintain annual compliance.
There were some positive outcomes: Hazardous materials were being replaced, new materials and processes were being developed, and companies had used the RoHS Directive to improve their supply chain process, to gain market share by developing new products and new processes. But was it really possible to benefit from the legislation? Legislation was driving the development of new and improved materials and processes, but every change cost money and, because producers had to comply, end users would have to pay and European industry was likely to suffer.
Professor Goosey turned his attention to issues of resource utilisation. There was a growing awareness of the finite availability of some materials, and limited access to some sources of key materials which could impact the ability to produce both existing electronics and some newer technologies. The demand for several elements, including helium, phosphorus, indium, and gallium was predicted to exceed supply in the near future. Most of the world’s rare earth elements were sourced from China, and many of these elements were critical to the future of electronics: Tellurium, hafnium, and gallium in semiconductors; tantalum in capacitors; indium in displays; and neodymium and dysprosium in magnets. As an example, the electric motor for Toyota’s Prius hybrid car contained one kilogram of neodymium. The IeMRC’s research agenda addressed key areas where the UK electronics industry had strength and future needs, with an underpinning theme of "Sustainability and Environmental issues." A key thematic area was Sustainable Manufacture, Products, and Processes, and four new projects in sustainable electronics had been awarded funding.
A logical follow-on from Martin Goosey’s references to RoHS was the presentation entitled “RoHS Recast and Beyond,” from Gary Nevison, head of legislation and compliance at Farnell. He summarised the changes in the scope of the directive, which had been extended to all electrical and electronic equipment including medical devices, monitoring, and control instruments, and products not covered under the previous 10 categories unless specifically excluded, such as wardrobes with internal lighting, gas cookers and petrol lawnmowers!
The original RoHS Directive restricted the use of six substances: Lead, mercury, hexavalent chromium, cadmium, polybrominated biphenyl flame retardants, and polybrominated diphenyl ether flame retardants. The recast did not yet restrict additional substances, but certain plasticizers would probably be included in the future. Nevison did his best to clarify the salient details of the directive, with particular reference to Article 2.2 “Non-compliant EEE that was outside the scope of RoHS1, but within the scope of RoHS2, may continue to be made available on the market until 22 July 2019. Non-compliant EEE that was not in scope of RoHS1 cannot be sold after 22 July 2019,” which indicated that the entire supply chain must be cleansed of non-compliant electrical and electronic equipment by July 22, 2019 if Article 2.2 is not changed. “Read it through a few times!” he advised.
Finished products and components required a CE mark, a Declaration of Conformity, and a Technical File, and Nevison gave examples of how these should be presented. Declarations of Conformity had to be kept on file for 10 years and signed by someone in authority. Nevison suggested that this should be the person with the most technical awareness--the technical director rather that the CEO. And the only acceptance symbol of compliance was the CE mask. None of the plethora of ad-hoc “RoHS-Compliant” labels would be permitted.
Martin Baxter, an executive director of the Institute of Environmental Management and Assessment, reviewed the revision of ISO 14001, due to be published as an international standard in May 2015, and discussed how it could help to deliver business value.
ISO 14001 was a global standard that supported international trade, second only to ISO 9001 in the extent of its adoption: there were now 267,000 certified organisations in 158 countries. An international study group had produced a report on environmental management standards to address future challenges and made 24 recommendations for improvement. ISO had now adopted a new uniform structure for all of its management system standards, using common clause titles and numbering, clause content, terms, and definitions. Discipline-specific content could be added, for example environment or quality, and the whole standard was now focused on outcome rather than on systems.
The overall context required organisations to consider a broad range of internal and external factors, consider external environmental impacts on the organisation, including how these would impact on wider organisation, and to determine the expectations of interested parties, including those outside of the organisation. Enhanced requirements for top management involvement required the environmental management system to be aligned with the organisation’s strategy, and environmental performance to be considered in strategic planning. “We hope that people will find it a useful standard.”
Counterfeiting in the electronics supply chain was an issue discussed by Roger Rogowski from the UK Electronics Alliance. He gave an overview of the size and shape of the problem, what organisations were doing something about it, and where companies could go to get support.
He began with statistics: The number of reported counterfeit‐part incidents reached a record high of 1,363 worldwide in 2011, an average of 25 suspected counterfeit parts had been reported to the Anti-Counterfeiting Forum database in 2013, and there were 1,800 cases of suspected counterfeit parts in the U.S DoD supply chain. 57% of counterfeit parts reported between 2001 and 2012 were obsolete or obsolescent.
Rogowski described the methods used to actually manufacture counterfeits, and how reclaimed components were sold as new or remarked to pass off as a higher-specification part, or to pass off as RoHS compliant, or marked with updated date codes. Counterfeiting was not restricted to high-value components: Almost every imaginable part was known to have been counterfeited, as well as electronic equipment like battery chargers and computer accessories.
What was being done about it? Rogowski listed relevant organisations in the UK: The BEAMA Anti-Counterfeiting Working Group, the European Semiconductor Industry Association Anti-Counterfeiting Task Force, the Intellectual Property Office IP Crime Group, the MoD Counterfeit Avoidance Working Group and the UKEA Anti-Counterfeiting Forum. There were International standards: IDEA‐STD‐1010B, IEC/TS 62668‐1 Parts1 and 2, ISO 12931:2012, and SAE ARP6178, AS5553A , AS6081, AS6171, and AS6174. Practical advice could be obtained here and here.
The first conference day concluded with an excellent technical presentation from Dr. Jeremy Smallwood of Electrostatic Solutions Ltd., who discussed how to profit from knowledge and experience in ESD control.
Many components or assemblies were susceptible to ESD damage and it was vital to protect them from damage by handling only in an ESD-protected area, and using protective packaging when they were outside the area. Inadequate ESD control could lead to product failures, either in-house or in the field, and incur the costs of failure analysis and rework, or delays while replacement components were sourced, as well as causing damage to product and company reputation.
Dr. Smallwood listed the costs of implementing effective ESD control: Planning and development of the ESD control program, EPA equipment and control measures, ESD protective packaging, ESD training, compliance verification, and product failure-rate tracking, and analysis. Most of these costs could be viewed as investments, provided the system was installed and operated with knowledge and understanding, and there would always be some trade-off between cost and effectiveness. Cutting the cost too fine, underestimating the ESD risk, or inadequate specification of the ESD programme could lead to possible ESD failure modes remaining unaddressed. Inadequate ESD training could result in lack of awareness, improper or unreliable use of equipment, poor following of procedures, and low priority being placed on ESD control. Inadequate compliance verification could lead to undetected equipment failures and non-compliant materials and tools, leading to poor ESD control
He recounted several case histories, some of which were examples of the most elementary mistakes resulting in a waste of investment money. Successful strategies required knowledge and understanding of ESD risks and protection techniques, of standards and of operations and processes in the facility. And if systems and procedures were designed to be convenient to operate, the procedures were much more likely to be followed reliably.Editor's Note: To view the conclusion of Pete Starkey's write up, click here.
More Columns from The European Angle
CircuitData: A New Open Standard for PCB Fab Data ExchangeI Never Realised It Was So Complicated!
The European Angle: Institute of Circuit Technology 43rd Annual Symposium
Ventec International Group's Martin Cotton Celebrates 50 Years in PCB Design
Reporting on the Institute of Circuit Technology Spring Seminar
EuroTech: Raw Materials Supply Chain—Critical Challenges Facing the PCB Industry
EuroTech: ENIPIG—Next Generation of PCB Surface Finish
EuroTech: Institute of Circuit Technology Northern Seminar 2016, Harrogate