-
- News
- Books
Featured Books
- pcb007 Magazine
Latest Issues
Current IssueInventing the Future with SEL
Two years after launching its state-of-the-art PCB facility, SEL shares lessons in vision, execution, and innovation, plus insights from industry icons and technology leaders shaping the future of PCB fabrication.
Sales: From Pitch to PO
From the first cold call to finally receiving that first purchase order, the July PCB007 Magazine breaks down some critical parts of the sales stack. To up your sales game, read on!
The Hole Truth: Via Integrity in an HDI World
From the drilled hole to registration across multiple sequential lamination cycles, to the quality of your copper plating, via reliability in an HDI world is becoming an ever-greater challenge. This month we look at “The Hole Truth,” from creating the “perfect” via to how you can assure via quality and reliability, the first time, every time.
- Articles
- Columns
- Links
- Media kit
||| MENU - pcb007 Magazine
Estimated reading time: 14 minutes
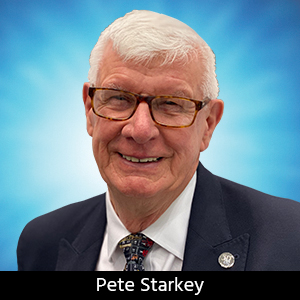
Contact Columnist Form
An Inside Look: SMART Group European Conference 2013, Day 2
The second—and intensely technical—day of the SMART Group 2013 European Conference was introduced and knowledgeably and assertively moderated by Technical Committee Chairman Sue Knight. The programme commenced with a session on solders, beginning with an overview of world solders by Dominic Lodge, leader of the Soldertec network at ITRI.
He explained that more than 50% of the world's tin production was used in solder, with 10,000 tons per annum now going into lead-free formulations, although the tonnages for bar and wire solder far exceeded the quantity used in solder paste. A surprising statistic was the amount of solder actually used in in high density assemblies; for example, an iPhone accounted for only 0.7 grams.
Lodge explored the reasons for the popularity of SAC 305 and SAC 405 alloys after the enactment of the WEEE and RoHS regulations in 2006, and the attributes of silver as an alloying metal. SAC 305 had been promoted as the nearest thing to a drop-in replacement for traditional tin-lead. It had a eutectic melting point of 217°C and the presence of silver reduced further silver dissolution, improved thermal fatigue resistance, gave good electrical and thermal conductivity properties, and promoted wetting to common PCB surface finishes.
But silver was a costly and politically sensitive metal, which increased copper dissolution rates, increased drossing and reduced the resistance of assemblies to drop-shock failure. Reducing silver content introduced a pasty melting range, reduced wetting speeds, reduced mechanical properties and thermal fatigue. Adding nickel to the alloy reduced copper dissolution and retarded intermetallic growth but could cause dewetting. Adding bismuth increased strength and creep properties, but introduced the risk of a low melting-point phase when lead was present. Addition of phosphorus and germanium both reduced oxidation in wave soldering, although too much phosphorus could cause dewetting. Germanium improved solder flow and made nice shiny solder joints, and addition of rare earth like cerium could decrease wetting time.
Lodge concluded that although lead‐free soldering would remain the major trend, there were still some concerns about reliability. Second generation technologies would generally be based on low silver and high reliability solders might include nanocomposites.
And so to the serious metallurgy lesson: Keith Sweatman, leading authority on solder alloys, senior technical advisor to Nihon Superior, active participant in HDPUG and iNEMI consortia projects relating to lead-free solder performance and reliability and member of several IPC standards committees relating to soldering technology, gave an enlightening presentation entitled "Economic Rationalism in Solder Selection - Toward Cost-effective Solder Formulation" which reviewed recent developments in the understanding of factors determining the performance of solder joints in service and identifid ways in which the challenges the electronic industry is facing in solder-based assembly could be met cost-effectively. He described the evolution of lead-free solder alloy formulation, how failure mechanisms in solder joints were becoming better understood, how solder alloy microstructure could be manipulated for the cost-effective enhancement of reliability, and what might be the characteristics of the next generation of solder alloys.
Sweatman stated, "To understand where we are going, we need to understand how we got to where we are now."
So where were we now? For reflow soldering the predominant alloys were SAC 305 or SAC 405, with an increasing trend towards "LowSAC" and "NoSAC," with similar trends for wave and selective and hand soldering and rework. He listed several typical NoSACs and LowSACs, commenting that more than a few appeared to have been formulated for patent avoidance rather than performance.
How did we get here? Long before WEEE and RoHS, legislation prohibiting the use of lead had been proposed in the U.S. and the industry had responded with contingency plans for lead-free solders, with all sorts of alloys proposed. The European IDEALS project aimed to develop lead-free soldering processes for implementation in 1999-2000, and suggested SnAg3.8Cu0.7 eutectic alloy for reflow soldering, SnAg3.8Cu0.7Sb0.25 for general purpose wave soldering use, and SnBi5Sb2Ag1 for single-sided wave assembly. In the late 1990s, the Japanese declared their intention to switch to lead-free soldering technologies. The turning point came in the mid-2000s when a round-robin evaluation programme coordinated by the IPC Solder Products Value Council concluded that SAC305 was the alloy of choice for the electronics industry, so it became established as a standard material for lead-free soldering.
But SAC305 had not proved to be the universal solution. Sweatman listed a catalogue of issues: Requirements for lower temperature reflow profiles, requirements for solders that could operate at higher temperatures, and improved drop-impact performance. Challenges in reflow soldering included voiding, head-on-pillow defects and increasingly long reflow profiles. Challenges in wave soldering included barrel fill on thick heavy boards and economic pressure to minimize the use of silver. The end results had been a proliferation of alloys and a downward trend in silver content.
Looking to the future, Sweatman believed that the key consideration in alloy development was the better understanding of solder joint failure mechanisms, so that progress could be made scientifically rather than empirically. He showed examples of accelerated thermal cycling and thermal fatigue failure, with particular reference to the metallurgical changes that were occurring during crack initiation and propagation, then explained in great detail how the crystal structure of the solder could be modified and controlled, how melting point could be lowered, how wettability could be improved and mechanical properties adjusted, all to the delight of the metallurgists in the audience and the wonderment of those with lesser qualifications.
Richard Boyle, Henkel's top soldering specialist, took the floor next, to talk specifically about high-reliability lead-free alloys for automotive applications, where the requirement was to withstand wide temperature cycling ranges and operating temperatures. Lead-free alloys available in the early 2000s were characterised by very high processing temperatures, and limited reliability in high operating-temperature applications. The automotive people demanded 15-year reliability, with a zero-failures target and a 30-year guarantee of continuity of supply.
To address these challenges, a German-based consortium of solder manufacturers, automotive electronics OEMs and academic institutions had started from first principles to develop a lead-free alloy that met the requirements of working at operating temperature up to 150°C, surviving thermal cycling of 1,000 cycles at -55°C to 150°C and reflowing at 230°C or below, meeting RoHS standards and being cost-competitive
They consortium found that these requirements could not be met with a three-component alloy. So, starting with SAC387, they modified the properties by adding bismuth, antimony and nickel as grain refiners, ending with s six-component alloy with a non-eutectic melting range of 209°C to 218°C, which they named Innolot. This material had high tensile strength, yield stress, and shear strength at both low and high operating temperatures, and performed remarkably well on thermal cycling and drop testing. Its reliability under vibration testing compared well with traditional tin-lead solders and was superior to other lead-free alloys. Boyle reviewed the metallurgy of Innolot alloy, and showed detailed results of temperature cycling and thermal shock testing in comparison with SAC387 and SN63.
Regular contributor to SMART Group events, Martin Wickham came from the National Physical Laboratory to discuss solderless interconnect for future electronics assembly, and review ongoing NPL projects. "What's wrong with solder anyway?" he asked. Solder had been developed for electronics by the radio industry in the early 20th century, and used on printed circuits since the 1940s. He considered solder to be an excellent interconnection material for a wide range of applications, which would still be used in electronics in the next century. But there was a range of applications at both higher and lower operating and fabrication temperatures where solder was not an ideal solution. The Electronics Interconnection group at NPL were encouraged to be innovative and to push the boundaries, and Wickham described the development of a range of alternative interconnection technologies designed to meet these demands.
At the high-temperature end, sintered interconnect metals had considerable potential and there was currently a high level of interest in sintering for die bonding. NPL were partners in the ELCOSINT project, Electronic Component Sintered Interconnections, with the objective of developing novel polymeric, sintered interconnection materials to replace high-lead-content materials and increase the operating temperature of electronic assemblies beyond 250°C. Nano-silver based materials were being evaluated. Although silver had a metallic melting point of 961°C, nano-silver was capable of being sintered at temperatures less than 275°C, and even lower if pressure was applied. The main area currently under investigation was how the sintered material interacted with other metallic surfaces. Mechanical performance and reliability had yet to be characterised.
At the other end of the operating-temperature scale, Wickham discussed developments in printed and plastic electronics, where interconnection was necessary, but soldering, even with low-melting-point alloys, was not appropriate and conductive adhesives techniques were preferred. Most conductive adhesives were silver-based, but a TSB-funded project at NPL aimed to substitute carbon for silver, for economic and environmental benefit. Addition of graphene substantially improved the conductivity of carbon-based inks.
Wickham concluded his presentation with a review of the REUSE project, where simple electronic circuits assembled with conductive adhesives could be "un-zipped" at end-of-life by immersion in hot water and over 90% of the constituent parts recovered for recycling.
Keynote for the afternoon session came from Pete Lomas, co-founder and trustee of the Raspberry Pi Foundation, which set out to provide a small cheap computer to encourage kids to experiment and develop computer engineering and programming skills. Lomas and his colleagues observed that young people have become consumers rather than the creators they had been 10 and 20 years ago, more interested in playing the latest arcade game than understanding how the computer worked and what they could make it do.
Against that background and after six years in its creation, "We had to wait for Moore's Law to catch up. We needed it to be cheap enough that you didn't have to worry about breaking it," the Raspberry Pi went into production, with the manufacturing contracted to China in an attempt to minimise costs. Elements of the cost model were components, PCB, assembly, test, yield, support, and monitoring. But there were many problems surrounding the launch, the product got off to a very shaky start, the project were unable to satisfy the demand and there were many quality and reliability issues, mainly related to the Chinese having sourced poor quality equivalent components.
The decision was made to reshore the manufacturing, trading-off the additional costs of BOM and assembly against savings in transport, the need for local quality monitoring in China, and field returns. Sony had been chosen as the EMS provider because of its desire to engage, its technical capability, its collaborative "can do" attitude, its quality based culture and its scalable capacity. In the end analysis, the bottom-line costs were almost identical, with the added brand kudos of "Made in UK." The higher UK labour cost could be mitigated by improved design-for-manufacture, and the higher BOM costs managed by international purchasing. Sales to date exceeded 1.8 million units, and defect rates were at the 0.03% level.
Failure analysis was the subject of the following presentation. Stewart McCracken, managing director of MCS, described an elegant technique for microsection preparation, which had enormous advantages over traditional mounting, grinding, and polishing techniques that could distort or obscure critical details as a consequence of the mechanical stresses involved. His technique was based on the application of broad ion beam (BIB) machining to the microsectioning process and in principle involved masking-off the functional area of the sample and machining away the rest with a beam of energised ions in the form of an argon gas plasma. Material was removed at the atomic level with absolutely no mechanical damage--no smearing or deformation--and the true structure of the material was revealed. No potting resin was required, so an additional benefit was that, as well as the cut face of the cross-section, the adjacent surface could be examined, whether by optical or scanning electron microscopy.
He showed several examples of sections prepared by BIB, and the clarity of detail and sharpness of edge definition were remarkable. The technique allowed the critical examination of thin surface layers, such as immersion tin and immersion gold, and, when combined with scanning electron microscopy and energy-dispersive X-ray spectroscopy, the compositions of surface and sub-surface structures could be determined. In cross-sections of BGA joints, the copper-tin intermetallic phases were clearly seen and extremely fine Kirkendall voids could be readily detected in aged solder joints. BIB machining could be used to reveal otherwise hidden damage at interfaces and to identify failure mechanisms. The techniques he described brought a new dimension of capability to defect investigation and failure analysis.
The final session of the conference was devoted to the science and technology of cleaning electronic assemblies after soldering and began with SMART Group Vice Chairman Graham Naisbitt, managing director of Gen3 Systems, who explored answers to the conundrum "To clean or not to clean?" with specific reference to supposedly "no-clean" fluxes. Although the perceived primary advantages of running a no-clean process were to save money and space by eliminating a process, Naisbitt made it clear that some cleaning was inevitable anyway: Pallets, stencils, and misprints for example, and that factors like product miniaturisation, increasingly hostile product operating environments, and particularly the introduction of lead-free soldering presented a new generation of electrochemical reliability issues. And the perception of cost saving through not cleaning was misguided; he asserted that cleaning would actually save money by improving end product reliability and reducing field returns.
Accepting that cleaning was making a comeback, how could the right process be selected and evaluated? The typical assembler did not have the time, the money or the staff, nor could he justify the disruption to production of carrying out a comprehensive and meaningful programme to explore all the variables. Help was at hand. Through ESCO, the British Electronics Systems Community, Naisbitt had proposed a collaborative project which would qualify for government-funded support and be carried out by an institution such as the Materials Technology Centre, which had the appropriate equipment and skills. He invited prospective industrial partners to register their interest.
Naisbitt having justified in principle the ongoing necessity for cleaning, it was the turn of the experts to describe the practical details and process alternatives. Martin Königer, senior process engineer with ZESTRON, emphasised the need for effective process monitoring and control of bath parameters, whatever actual process was chosen, to ensure consistency in operation. He reviewed indirect methods for measurement of cleaning agent concentration. Straightforward test kits were available based on colorimetry, or refractive index or conductivity measurement. Alternatively, the bath parameters could be monitored by automated methods, either off-line or on-line, and corrections to bath chemistry made by manual addition or automatic dosing. Automated on-line monitoring also gave the opportunity for real-time data recording. Good control gave higher process transparency and reduced cost through longer bath life. "The cleaning process is only as good as its monitoring!" But whatever technique was used for controlling the process line, the definitive measure of its performance was the cleanliness and freedom from ionic contamination of the product. Königer reviewed IPC, ISO, and J-STD standard test methods and commented upon their limitations, particularly that isopropanol was not necessarily a good solvent for extracting ionic material.
The final speaker was Mike Bixenman, from Kyzen Corporation, who gave encyclopaedic advice on how to design a batch cleaning process for electronic assemblies as demands for performance and reliability continued to increase. The primary considerations in designing a cleaning process were to start with a cleanable solder paste, then to make sure the reflow process was under control, then to select a cleaning agent that matched the soil and the intended cleaning equipment. And the cleaning machine itself was probably the main driver in making decisions. "It's not rocket science, it's process!" Bixenman used an Ishikawa diagram--with the main branches headed PCB design, solder paste or flux, cleaning agent, and cleaning machine--to illustrate all the process factors to be taken into consideration in order to achieve the ideal cleaning condition of no unwanted visible or ionic residue on the surface or under the components.
Six categories of soldering material to be taken into account in the selection of "cleanable soils" were SMT solder paste, SMT solder flux, wave-solder bar, wave-solder flux, rework solder wire, and rework solder flux, because these would directly impact the cleaning process. In addition to higher reflow temperatures, consequences of the move to lead-free soldering included the requirement for higher fluxing capacity, and higher molecular weight flux resins, some with polymer additives. The general result was that residues were harder to clean. "Soluble soils clean better" was a statement of the obvious, but a pointer toward careful matching of the cleaning agent to the nature of the residue as well as to the machinery, where considerations of concentration, temperature, pressure, speed, rinsing, and drying were all important factors. Optimisation of spray impingement and avoidance of shadowing were critical to achieving effective cleaning under large and low-stand-off components.
Sue Knight brought proceedings to a close, thanking the speakers for their contributions, the delegates for their attention and the table-top exhibitors for their support. And special thanks to Technical Committee members Nigel Burtt and Mike Fenner, for their efforts in putting together an excellent conference programme.
More Columns from The European Angle
CircuitData: A New Open Standard for PCB Fab Data ExchangeI Never Realised It Was So Complicated!
The European Angle: Institute of Circuit Technology 43rd Annual Symposium
Ventec International Group's Martin Cotton Celebrates 50 Years in PCB Design
Reporting on the Institute of Circuit Technology Spring Seminar
EuroTech: Raw Materials Supply Chain—Critical Challenges Facing the PCB Industry
EuroTech: ENIPIG—Next Generation of PCB Surface Finish
EuroTech: Institute of Circuit Technology Northern Seminar 2016, Harrogate